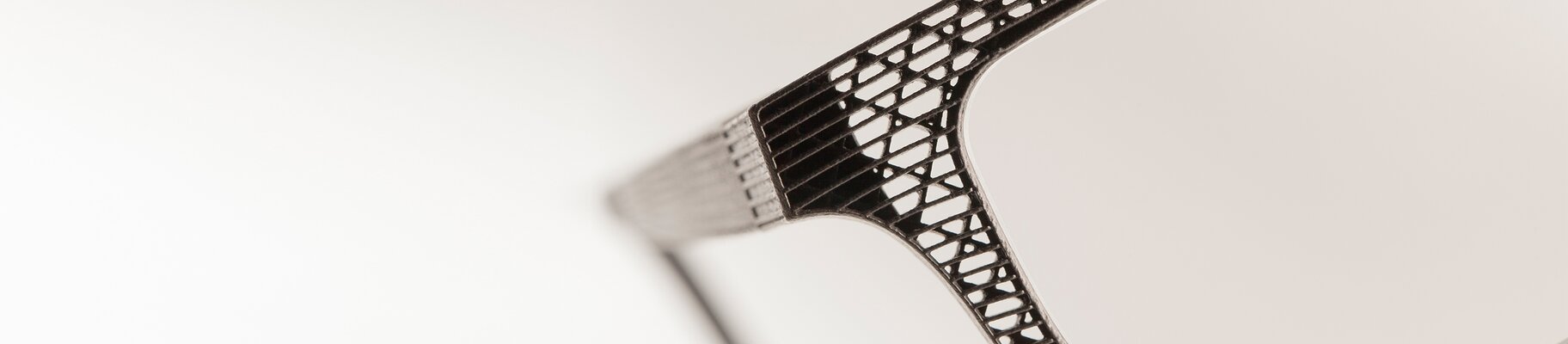
Metall-3D-Druck für Brillengestelle
Mit additiver Fertigung hergestellte Brillen von EOS
Raytech | Hoet | Innovationsgeschichte
Neue Perspektiven durch den Brillenspezialisten Hoet - ermöglicht durch die Unterstützung von Raytech und EOS
"Das Auge ist der Punkt, an dem Seele und Körper verschmelzen". Ob sich die Designer von Hoet an diesem Zitat des Dramatikers und Lyrikers Christian Friedrich Hebbel orientiert haben, ist nicht klar. Aber wenn man sich das klassische und unnachahmliche Design der neuen Kollektion ansieht, könnte man das durchaus annehmen. Möglich wurde diese auffällige Serie durch die Additive Manufacturing Technologie. Für die technische Umsetzung des Designs war der EOS Partner Raytech aus Belgien verantwortlich.

"Wir hatten drei Gründe, warum wir uns für Additive Manufacturing für unsere neuen Brillengestelle entschieden haben: Wir konnten Dinge auf eine Weise herstellen, die mit Standardtechnologien nicht möglich gewesen wäre. Wir konnten verschiedene Größen herstellen, ohne dass uns zusätzliche Kosten entstanden sind. Und es ist eine grüne Technologie, die dank ihrer Flexibilität den Energie- und Materialverbrauch deutlich reduziert."
Patrick Hoet | Geschäftsführer | Hoet
Herausforderung
Herstellung einer Brillenserie mit spezifischen Designmerkmalen, die genau den Anforderungen des Kunden entsprechen
Die Hersteller von Konsumgütern sind genauso innovationspflichtig wie Unternehmen in anderen Branchen - der Wettbewerb um den Kunden ist hart, und wehe dem, dem es an Ideen oder der richtigen Formel fehlt. Neben der reinen Funktionalität zählen gerade im Consumer-Umfeld ästhetische Argumente mit Verkaufsargumenten. Der Kunde gibt Geld in die Hand für etwas, das sein Auge erfreut.
Hoet, ein Unternehmen, das sich auf die Entwicklung und Herstellung von Brillen spezialisiert hat, suchte nach einer innovativen Antwort auf diese Herausforderung.
Das belgische Familienunternehmen, das 1884 gegründet wurde, hat mit seiner Cabrio-Brille die Messlatte besonders hoch gelegt. Dieses innovative Design, das eine Sonnenbrille und ein Cap-Visier kombiniert, um einen doppelten Schutz vor Sonnenstrahlen zu bieten, wurde von Bieke Hoet entworfen. Die Designerin, die das Unternehmen leitet, erfand ein eigenes laminiertes Polypropylenmaterial für die Herstellung der Brillengestelle des Unternehmens. Diese Experimentierfreudigkeit zeigt die Offenheit für neue Perspektiven und ermöglichte es dem Unternehmen, sein Produktionsrepertoire und die Auswahl der Materialien zu erweitern.
Es hatte nicht nur den Mut, neue Wege zu gehen, sondern war auch davon überzeugt, dass die ökologische Nachhaltigkeit ein wesentlicher Bestandteil eines jeden neuen Ansatzes ist. Auch die Kosten hatte das Unternehmen von Anfang an fest im Blick. Mit diesem Dreiklang aus klaren Voraussetzungen - Suche nach neuen Designmöglichkeiten, akzeptablem Kostenniveau und nachhaltiger Produktion - machte sich Hoet auf die Suche nach einem neuen Produktionsverfahren für seine neueste Produktlinie. Schnell wurde der Brillenspezialist auf die additive Fertigung aufmerksam.
Lösung
Der industrielle 3D-Druck bietet eine herausragende und konkurrenzlose Gestaltungsfreiheit. Dieser Vorteil kann nicht nur bei der Herstellung von Prototypen genutzt werden, sondern bietet auch einen immensen Mehrwert in der Serienproduktion - insbesondere bei Produkten, deren Design und Ästhetik eine wichtige Rolle bei der Kaufentscheidung der Kunden spielen. Anything goes" könnte der Slogan für Additive Manufacturing sein. Dass Hoet, ein designorientiertes Unternehmen, von dieser Technologie angezogen wurde, ist keine Überraschung. Mit Blick auf die außergewöhnliche Freiheit, die sie bei der Umsetzung von Ideen bietet, machte sich Bieke Hoet an die Arbeit, um Designs für die Kollektion zu entwerfen.
Nach Abschluss der kreativen Arbeit entschied sich das Unternehmen, das vorhandene Fachwissen zu nutzen, um eine effiziente Produktion zu gewährleisten. Die Suche nach einem erfahrenen Partner führte schließlich zu Raytech, einem Unternehmen mit Sitz in der Nähe von Hoet's Niederlassung in Brügge. Raytech verfügt über langjährige Erfahrung und das erforderliche Fachwissen in der additiven Fertigung. Das Unternehmen ist beispielsweise Zulieferer für die Elektronik- und Automobilindustrie. Die metallbasierte Variante der Technologie DMLS, bei der ein Laser ein Bauteil Schicht für Schicht aus einem Pulver aufbaut, ist für Kunden in diesen Branchen von großer Bedeutung.
Gemeinsam entwickelten Hoet und Raytech ein Produktionskonzept. Dazu gehörte die Verwendung von EOS Titanium Ti64 als Kernmaterial. Titan wird häufig für Brillenfassungen verwendet, weil es extreme Flexibilität mit hoher Festigkeit und geringem Gewicht verbindet. Zudem ist das Metall einer der zahlreichen Rohstoffe, die mit der EOS Technologie verarbeitet werden können. Das Design, das Material und das Verfahren standen also schon fest. Es fehlten nur noch die Mittel zur Herstellung. Raytech entschied sich einmal mehr für das hauseigene EOS-System: "Was uns bei EOS überzeugte, war der exzellente Service und vor allem die schnelle und kompetente Anwendungsberatung des Unternehmens. Die Praxisnähe, die schnelle Reaktion und die führende Technologie in Verbindung mit einem exzellenten Produktionssystem ergaben ein stimmiges Gesamtpaket", sagt Paul Raymaekers, Inhaber und Geschäftsführer von Raytech.

"Unserer Meinung nach ist EOS der beste Partner, mit dem wir im Bereich der additiven Fertigung zusammenarbeiten konnten. Besonders beeindruckt hat uns, dass wir sofort Zugang zu Ansprechpartnern mit hoher Kompetenz im optischen Bereich und in Bezug auf den von uns verwendeten Werkstoff Titan hatten. Dieses Basiswissen, gepaart mit den schnell hergestellten, hochwertigen Testmustern, hat uns überzeugt, dass wir die richtige Wahl des Partners getroffen haben."
Paul Raymaekers | Eigentümer und Geschäftsführer | Raytech
Ergebnisse
Das Ergebnis des Dreigestirns Hoet, Raytech und EOS wird nicht nur gut aussehen, sondern auch für alle sichtbar sein. Die verschiedenen komplexen und filigranen Gitterstrukturen der Rahmen wären mit herkömmlicher Technik nicht möglich gewesen. Die Umsetzung des unnachahmlichen klassischen Designs wurde erst durch die EOS M 290 möglich. Doch trotz der angestrebten Optik hatte Hoet noch weitere Anforderungen - und auch diese wurden durch die additive Fertigung erfüllt. Da keine weiteren Werkzeugkosten anfallen, können mit ein und derselben Maschine verschiedene Größen schnell und einfach hergestellt werden, ohne dass zusätzliche Kosten entstehen. In Verbindung mit der entsprechenden Software und dem Scanning-Equipment kann sie sogar maßgeschneiderte Fassungen für das jeweilige Modell herstellen.
Das erhöht den Komfort der Brillengläser. Bieke Hoet weist noch auf einen weiteren Punkt hin: Normalerweise bleiben zwischen 30 und 40 % der produzierten Brillen unverkauft in den Schubladen des Groß- oder Einzelhändlers liegen.
Unter diesen Bedingungen ist eine genaue Produktionsplanung sehr schwierig. Mit der additiven Fertigung ist es jedoch möglich, nach Bedarf zu produzieren, so dass keine Lagerbestände angelegt werden müssen.
Dies verringert nicht nur die Lagerkosten, sondern senkt auch die durchschnittlichen Produktionskosten der verkauften Produkte.
Ein weiterer Vorteil der Technologie ist die kurze Markteinführungszeit, d. h. die Zeit zwischen dem Entwurf des Produkts und seiner Verfügbarkeit in den Einzelhandelsgeschäften. Nur zwei Monate nach der Installation des Systems waren die Rahmen verkaufsfertig. Und wenn nötig, dauert die Herstellung zusätzlicher Bestände nur wenige Tage.
"Die additive Fertigung hat sich in vielen Anwendungsbereichen bewährt. In der Regel stehen die funktionalen Aspekte im Vordergrund. Für uns waren jedoch die gestalterischen Möglichkeiten, die die Technologie bietet, ausschlaggebend für unsere Entscheidung", fasst Hoet zusammen.
"Wir wollten dem Markt etwas wirklich Neues bieten. Mit dem Einsatz der additiven Fertigung sind wir einmal mehr dem Credo der Cabrio-Reihe gefolgt: Der Einsatz neuer Materialien und Technologien bringt weitere Vorteile und eine fortschrittliche Ästhetik in den Bereich des Brillendesigns." Um mit einem Zitat von Mark Twain, einem der Großen der Weltliteratur, zu schließen: "Du kannst dich nicht auf deine Augen verlassen, wenn deine Vorstellungskraft unscharf ist. In ihrem Unternehmen sorgt Bieke Hoet für eine klare Sicht, die den Kunden hilft, neue ästhetische Perspektiven und eine Sicht von 20/20 zu erreichen.
Die Ergebnisse auf einen Blick
-
Attraktiv: Neue Gestaltungsmöglichkeiten
-
Maßgeschneidert: Einfache und kostengünstige Herstellung maßgeschneiderter Produkte
-
-40 % Überschuss: Produktion auf Anfrage
EOS-Erfolgsgeschichten
Erleben Sie drei Jahrzehnte Pionierarbeit im 3D-Druck mit EOS