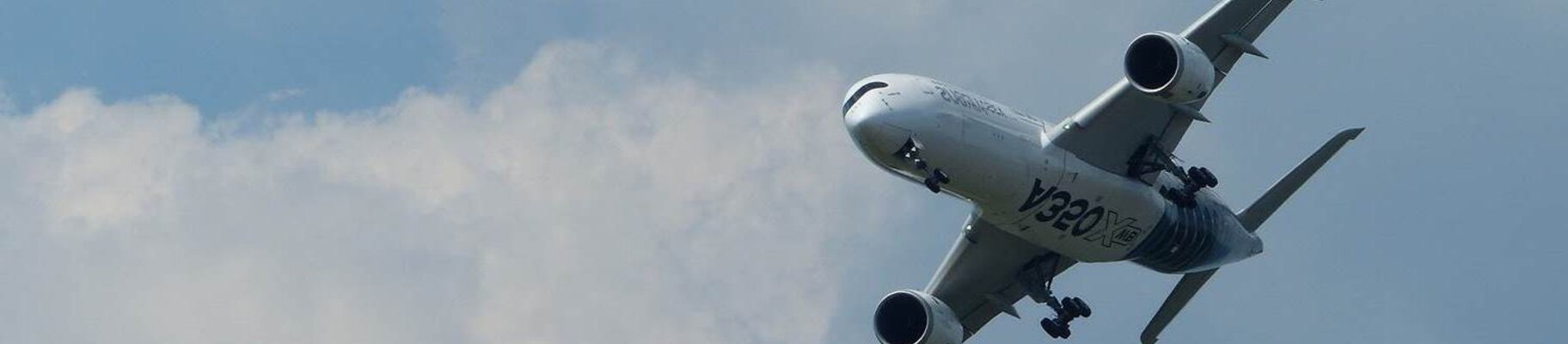
新型エアバスA350 XWB向けSogetiハイテク積層造形技術
A350 XWBのケーブルルーティング - 2週間でデザインからコンポーネントまで|サクセスストーリー
まったく新しい民間航空機が初めて空を飛ぶ瞬間は、常に特別なものであり、エアバスA350 XWBは特にそうであった。新しいミレニアムの子供として、開発作業が革新的な素材と製造プロセスに焦点を当てることは当初から明らかだった。未来の技術として、アディティブ・マニュファクチャリング(積層造形)も開発中に考慮すべき可能性のひとつだった。パイロット・プロジェクトの一環として、Sogeti High Techの専門家は、旅客機の垂直尾翼のフロント・スパーにケーブル・マウントを開発することに成功しました。EOSの技術と専門知識は、この開発プロセスにおいて極めて重要な役割を果たしました。
既存の部品をわずか2週間で "AM-ready "にするということは、最初の試みで成功しなければならないということでした。EOSとの優れた積極的な協力関係が、この野心的なプロジェクトを可能にし、素晴らしい結果をもたらしました。"
カルロス・リベイロ・シモエス|アディティブ・マニュファクチャリング・オファリング・リーダー|ソゲティ・ハイテック
チャレンジ
アディティブ・マニュファクチャリングによる、A350の垂直安定板のカメラ用ケーブル配線マウントの時間的制約のある開発と製造
このプロジェクトでは特に、エアバスの最新モデル用のケーブル配線マウントを製作した。このマウントは最終的に、垂直安定板に設置されたカメラの電源供給とデータ転送のために必要となり、乗客には外の景色を、パイロットには地上の方向を提供する。
製品要求文書では、連続生産に適した機能的に動作するコンポーネントが求められていた。この仕事は、キャップジェミニS.A.の完全子会社で、パリ証券取引所に上場しているソゲティハイテックに任された。
このケースで特に難しかったのは、リードタイムが2週間と短かったことだ。開発全体をこの期間内に完了させる必要があった:部品と現在の設置状況の分析から、トポロジーの最適化とその解釈を目的としたパラメータ研究、そして完成部品の設計と製造まで。また、架台は後処理を避けるため、支持構造をできるだけ少なくする必要があった。
さらに、このコンポーネントの仕様では、スナップオンケーブルホルダーの統合、軽量化、その後の航空業界認証の厳しい要件への適合が求められた。
従来の部品は、成形されたシートメタル部品と多数のリベットで構成されていた。上部のプラグコネクターはプラスチック製で、マウントの他の部品とは材質が異なっていた。目的は、プラグコネクターも含めた単一部品からなる統合ソリューションを開発することであり、それによって建設と設置の時間を大幅に短縮することだった。積層造形の軽量化目標は、トポロジー最適化に基づくパラメータ研究によって決定された。
ソリューション
部品点数を1点に絞り、EOS M 400で製造することで、製造時間を19時間に短縮
ソゲティハイテックは、この新しい部品のために、添加剤製造部品を設計するための試行錯誤の開発プロセスに従った。このプロジェクトは、既存の従来生産部品の今後の製造プロセスに関する分析から始まり、極めて良好な結果が得られました。この部品の機能性、素材、以前の複雑な構造から、EOSのパウダーベッドベースの3Dプリンティング技術の理想的な候補となりました。この技術が提供する設計の自由度により、複雑な構造を1つのピースで製造することができ、機能的な統合をおろそかにすることなく、軽量化設計を選択することができます。
この解析により、いわゆるデザインスペース(ケーブル配線マウントが占める可能性のあるスペース)を定義することができた。材料には、薄肉で複雑な構造に最適なアルミニウム合金AlSi10Mgが選ばれた。外部領域とのインターフェースはそのままで、非設計空間を形成するため、変更は必要ありませんでした。定義された荷重は、パラメータ研究におけるトポロジー最適化の境界条件とされ、新しい設計の基礎となった。
トポロジーの最適化計算にはCAEソフトウェアが使用されるのが通例だが、今回の再設計には、自由曲面を持つ構造物の設計に特化したソリューションが使用された。Sogeti High Techは、設計そのものを行いました。2週間というリードタイムに間に合わせるため、EOSはソフトウェアEOSPRINTを使用して、トポロジー最適化の結果から製作時間と最適化されたパラメータを計算した。これにより、製造プロセスの可能性と限界、およびサポート構造を避ける必要性を考慮しながら、製造部品のCAE実装が作成されました。
「傑出したハードウェアに加えて、EOSは付加製造部品を実現するための包括的な専門知識も提供しており、これは私たちが非常に高く評価している点です。
カルロス・リベイロ・シモエス|アディティブ・マニュファクチャリング・オファリング・リーダー|ソゲティ・ハイテック
結果
Sogeti社とEOS社の協力により、DMLS技術による設計の自由度を十分に活用しながら、同時にその制約も考慮した、積層造形に最適化されたコンポーネントを開発することができました。これにより、ケーブル配線用のプラグコネクタを設計に組み込むことができ、構造を最適化するために特定の重要な部分に局所的な補強を組み込むことができました。部品内の開口部と支柱を自立させることで、労力、ひいては後処理コストを最小限に抑えることができます。
さらに、マウントは必要なときにいつでも極めて迅速に製造できる。層厚90μmのEOS M 400で製造する場合、従来は70日を要していたが、わずか19時間で済む。
これは、90%をはるかに超える生産時間の短縮に相当する。この主な理由は、多くの個別工程と、以前は30個あった部品が、今では1回の生産で製造できる中心的な部品にまとめられたからである。さらに、個々の部品は、高価になりがちな組み立てや在庫を持つ必要がなくなった。部品アセンブリ全体の保管も、より簡単になった。
ソゲティは製造だけでなく、開発においても膨大な時間を節約することができた。最初のスケッチから完成部品までの全工程に要した時間はわずか2週間。これは驚異的なリードタイムである。同時に、この設計は重量効率の向上も意味する。
航空業界では、燃料消費を最小限に抑えるため、1グラム1グラムが重要であることはよく知られている。顧客であるエアバスは、この結果に十二分に満足している。
一目でわかる結果
- -29 単一部品 機能統合
- -生産時間を90%短縮
- -135グラムの軽量化
もっと見る
EOSの30年にわたる3Dプリンティングのパイオニアとしての卓越性をご覧ください。