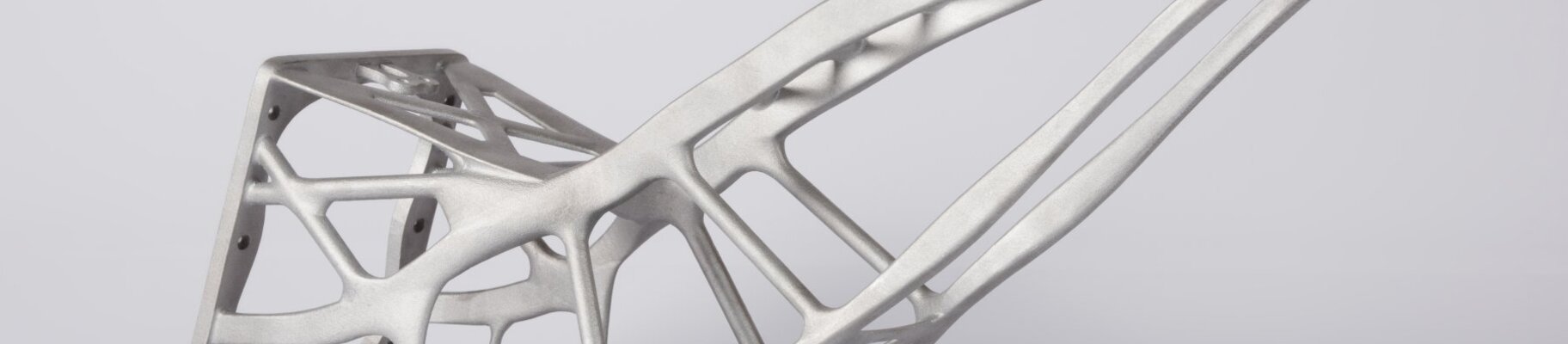
RUAG 3Dプリント衛星部品
RUAGのセンチネル衛星用アンテナ・ブラケット - 宇宙空間での展開が認証|イノベーション・ストーリー
多くの人にとって、無限に広がる宇宙といえば、ハリウッドの映画スタジオが語るSFの物語を思い浮かべるだろう。しかし、現実の世界では、他のどの分野よりも、宇宙旅行においてこそ、強い意志と明確なビジョンが、必要な技術を生み出し、宇宙での展開に備えるために不可欠であることは間違いない。スイスの技術集団RUAGが、地球を高所から観測するために設計したセンチネル衛星の建設で直面した課題がこれだった。地球の大気圏外でも、アディティブ・マニュファクチャリングは重要な役割を果たしている。
部品を大幅に軽量化し、同時に堅牢性を高めることができたのだ。部品の特性は、航空宇宙分野に必要な厳密さで実施された試験で、その価値が証明されました。私たちは今後数年間、積層造形についてもっと多くのことを耳にすることになるだろう!
フランク・ムリオー|構造部門ゼネラル・マネージャー|RUAG
チャレンジ
センチネル衛星用超軽量・堅牢なアンテナブラケットの製造
2016年のドイツ航空宇宙センター(DLR)の報告によると、輸送ペイロード1kgあたりの宇宙探査のミッションコストは20,000ユーロ以上である。1グラムでも節約できれば、上昇に必要な燃料が少なくて済むため、打ち上げ総費用が削減される。その結果、航空宇宙エンジニアは、余分な重量が急速に蓄積されるため、あらゆる部品から可能な限りグラム単位で削る必要がある。この場合、スイスのRUAGグループは、最適に設計されたアンテナブラケットを必要としていました。
しかし、重量の最適化だけでは十分ではない。ロケットの打ち上げ時には、ペイロードが大きく揺さぶられ、振動のレベルも相当なものになる。
また、時速数千キロという圧倒的な速度は、高いGフォースはもちろんのこと、旅客機で期待されるようなスムーズな飛行ができないことを意味する。安定性と剛性は、仕様書に記載される第二の必須項目である。残念ながら、この要件は軽量設計の必要性とは正反対である。
エンジニアは、形と重量の間で実行可能なレベルの妥協点を特定するために複雑な構造を採用する。
RUAGチームは、従来の製造方法では限界があったため、アンテナブラケットの構造に強度と重量の最適な組み合わせを求めた。
ありがたいことに、アディティブ・マニュファクチャリングは、必要な自由設計を実現する完璧な可能性を提供してくれた。部品テストは、前述の振動のためだけでなく、特に難しい課題だった。宇宙空間では、一般的に修理が不可能なため、信頼性が重視される。そのため、このようなコンポーネントの認証には長期にわたる複雑なプロセスが必要となる。すべての認証は、それを達成したエンジニアにとって称賛に値する。
複雑な構造により、重量と安定性のすべての要件を満たす積層造形による部品の製造。
このような場合、特に航空宇宙分野では、完全な生産チェーンが重要な役割を果たします。「RUAGの構造部門ジェネラルマネージャーであるFranck Mouriaux氏は、次のように説明しています。「例えば、設計の自由度や複雑なコンポーネントは軽量化に役立ちます。例えば、設計の自由度や複雑なコンポーネントは軽量化に役立ちます。しかし、最終的には、これらの潜在的な利点を特定し、理想的な方法で実装し、必要な認可を取得する必要があります。最もシンプルなコンポーネントでも、それが使用できなければ意味がない。"
基本的な適合性と剛性のテストが、アンテナブラケットの設計の出発点となりました。次のステップは、材料の選択、工程の定義、材料特性に関する初期基本試験でした。その後、部品のトポロジー最適化の出発点となる初期試験構造が構築されました。RUAGは最終的に、AltairのCADおよびFEMシステムによる集中的な作業と、積層造形による設計および製造に関するEOSの指導を組み合わせることで、アンテナブラケットの理論的に完璧な形状を実現することができました。

長さ約40cmのアンテナブラケットは、ドイツ・バーレーベンのcitim GmbHがEOS M 400を使用して製作した。400 x 400 x 400 mmの製作容積で、1回の発注で2つのアンテナ、30個の引張試験片、各種試験品を製作することができた。工期は約80時間。使用されたパラメーターセットは、表面品質と生産性を最適化した層厚60 µmのものであった。
使用されたアルミ合金、EOSアルミAlSi10Mgは、高強度と動的応力に対する強い耐性を特徴としており、高応力部品に最適な材料です。要求される特性を実証するため、包括的な試験が実施されました。航空宇宙分野では、これらの試験はプロジェクトの総範囲の最大80%を占めます。試験には、特別に製造された構造が用いられた。特にエンジニアは、コンピューター断層撮影装置でブラケットを検査した。また、さまざまな機械的、物理的手順も実施された。時には、部品にかかる応力が意図的に荷重制限を超えることもあり、最終的にはテストピースの破壊につながった。
EOSは、アディティブ・マニュファクチャリングにおける革新と優れた経験を兼ね備えています。このシステムは、あらゆる分野のあらゆる市場に、実に興味深い可能性を提供します。
アンドレアス・ベルカウ|CEO|シティムGmbH
結果
このような努力の結果、センチネル衛星用の新しいアンテナブラケットは、すべての期待を上回るものとなった。この部品は認証を取得し、宇宙空間での使用が承認された。宇宙での積層造形の利用がまだ始まったばかりであることを考えれば、この成果はさらに注目に値する。
例えば、部品の最小剛性要件は30%以上上回っており、乱気流飛行の後でも理想的なアンテナ位置を確保するのに十分なマージンを確保し、地球との無線通信を保証した。要求されたレベルの安定性が達成されたのは、応力分布が非常に均一だったからでもある。
さらに、アディティブ・マニュファクチャリングを使用することで、最終部品の重量が大幅に削減された。
この例では、革新的な技術を使用することで、部品特性の向上とシステム・コストの削減という、ありそうでなかった組み合わせを実現することに成功した。「このプロジェクトの結果には非常に満足しています。プロセス面では未知の領域に足を踏み入れましたが、安定した軽量コンポーネントを手に入れることができました。
「アディティブ・マニュファクチャリングは、宇宙旅行における基本的な手続き上の要求を満たすことができることを示している。複数の設計上の利点と部品自体の特性は、確かにこれを証明しています。私はこの技術に今後大きな可能性を感じています"
結果一覧
- 30%の厳格さ - 最低要求事項を30%超過達成
- 40%の軽量化
さらなるメリット
- インテリジェント:設計の自由度により均一な力の分散が可能
- 認定:包括的なテストによって検証された航空宇宙セクターの要件
もっと見る
EOSの30年にわたる3Dプリンティングのパイオニアとしての卓越性をご覧ください。