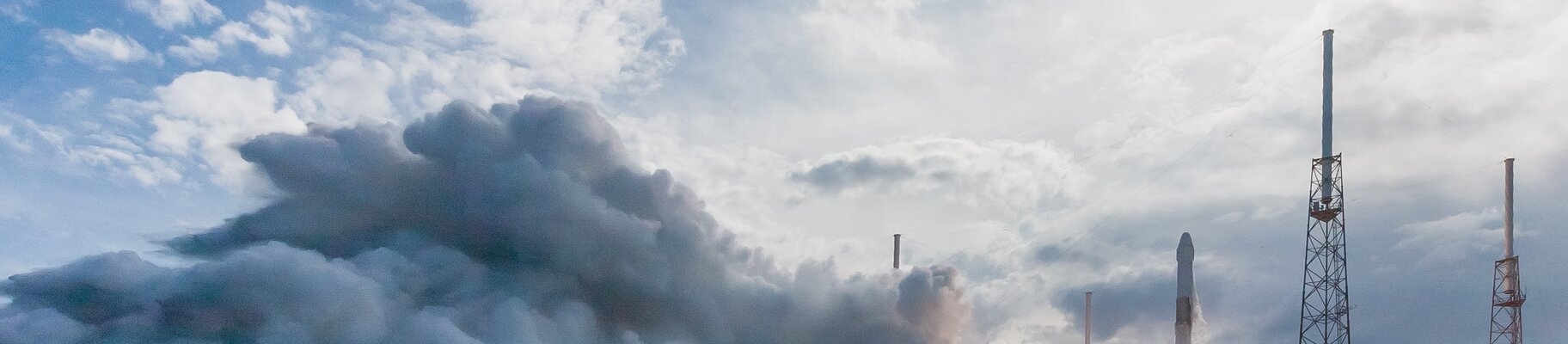
将来のアリアン推進モジュールの簡素化
アリアングループ|イノベーション・ストーリー
オール・イン・ワン設計 - 122個の射出ノズルとその他の部品を一体化。
「ミッション・クリティカル」は、航空宇宙産業で使用されるクラス1コンポーネントを完璧に表現しています。億単位の費用がかかるミッションは、これらの部品に依存しています。したがって、エンジニアは、製造チェーンを簡素化し、個々の要素の数を減らしながら、最高の品質、機能性、堅牢性を備えたコンポーネントを開発することを常に追求しています。EOS積層造形技術のおかげで、ArianeGroupはこれをまったく新しいレベルに引き上げることに成功しました:将来の上段推進モジュールのロケットエンジンのインジェクターヘッドは、248個の部品からわずか1個の部品になりました。インジェクターヘッドは簡素化され、文字通りオールインワン(AiO)設計になりました。

「アリアン・プログラムでは、当社の革新的な強みとEOSの専門知識を組み合わせています。私たちは、ロケットエンジンのインジェクターヘッドの積層造形に取り組んでいます。結果は素晴らしいものです:製造時間の大幅な短縮と50%のコスト削減です。"
ステフェン・バイヤー博士|生産技術・材料・プロセス部門責任者|アリアングループ
カレンジ
可能な限り部品点数を減らし、単価を抑えたロケットエンジン用噴射ヘッドの製造
欧州宇宙機関(ESA)は、効率的なロケット技術を用いて宇宙輸送において強力かつ独立した地位を築きたいと考えている。そのために、欧州の航空宇宙企業エアバス・グループとフランスのサフラン・グループによるジョイント・ベンチャーであるアリアン・グループが、次世代ロケットの製造を委託された。アリアンは、通信衛星のような重いペイロードを地球の周回軌道に投入できるように設計された欧州のロケットシリーズである。
推進モジュールでは、過酷な条件下で莫大な力が発生する。そのため、小さなスペースで最大レベルの信頼性と精度が要求されます。インジェクションヘッドは推進モジュールの中核をなす要素のひとつで、混合燃料を燃焼室に送り込みます。
その伝統的な設計は、さまざまな製造工程で製造・組み立てられる248個の部品で構成されている。鋳造、ろう付け、溶接、穴あけなど、さまざまな加工工程があるため、極端な負荷がかかると危険な弱点が生じる可能性がある。さらに、時間がかかり、複雑な工程となる。インジェクター・エレメントの分野では、従来の製造では、122個のインジェクター・エレメントに正確にネジ止めされた銅スリーブに、8,000個以上の十字穴を開け、そこから流れる水素を酸素と混合する必要があった。
これらの数字を見れば、すべての要素を組み合わせた機能的に統合された1つの部品が、明白だが野心的な目標に違いないことが明らかだ。これにより、特にクラス1コンポーネントの場合、大きな経済的可能性が生まれ、加工工程数と生産時間が削減される可能性がある。
ソリューション
機能統合により、248個の部品から構成されるのではなく、単一の要素から構成される付加製造製品
これらの課題を解決するのが、積層造形です。「インジェクターヘッドの一体生産は、EOS技術で可能です」と、産業用3Dプリンティングが選ばれた理由を説明するのは、アリアングループの生産技術-材料・プロセス部門責任者であるSteffen Beyer博士です。「アディティブ・マニュファクチャリングだけが、統合された機能性、軽量構造、よりシンプルな設計、リードタイムの短縮を1つの部品で実現できるのです。プロジェクトチームは、今回も耐熱・耐腐食性のニッケル基合金(IN718)を材料として選択した。この材料は、高温で優れた引張強度、耐久強度、クリープ強度、破壊強度を発揮し、新しい製造技術でも使用される。
「コンポーネントの開発に成功した後、私たちはコスト効率に目を向けました。アリアングループからの主な要求は、リードタイムと単価を削減することでした。製造は当初、EOS M 290によるインクリメンタル・プロセスで行われました。パイロットテストが成功した後、製造はより大型のEOS M 400-4システムにスケールアップされた。4レーザー技術により、推進モジュール・コンポーネントを最大4倍の速度で製造できるようになった。「生産性の高いEOSM 400-4システムに製造工程をスケールアップすることは、アリアン・プロジェクトの産業化と競争力を高めるための重要なステップでした。EOSスタッフの経験と業界専門知識のおかげで、コラボレーションは非常に効率的に展開されました。結果は、それ自体が物語っており、素晴らしいチーム・パフォーマンスの証明です」とシュテフェン・バイヤー博士は付け加えた。
結果
アディティブ・マニュファクチャリングを用いて製造された新しいインジェクター・ヘッドの結果は非常に印象的である。
EOSのパウダーベッドベースの産業用3Dプリンティング技術により、例えば122個の噴射ノズル、ベースプレートとフロントプレート、水素と酸素燃料用の対応する供給パイプを備えた分配ドームを、1つの統合コンポーネントとしてプリントすることが可能になりました。シングルレーザーシステムと比較して、EOS M 400-4マルチレーザーシステムの生産性は著しく高く、AiOインジェクターヘッドの例では、工期を3分の1に、コストを50%削減することができた。
プロジェクトチームは、一連の成功をさらに積み重ねることができた。設計を簡素化し、鋳造部品の品質と比較して材料特性を向上させたことで、積層造形技術により、強度を損なうことなく肉厚を大幅に減らすことができました。
重量を大幅に削減することは、工期のさらなる短縮を意味し、もちろんコスト削減にもつながる。
最後になるが、積層造形プロセスにより、技術革新のサイクルを大幅に早めることができる。開発段階での構造改善、設計変更、テスト部品の製造は、鋳造部品の場合のようにエンジニアが工具の準備に時間を費やすことなく、CADデータに基づいて直接生産に移すことができる。このように、産業用3Dプリンティングは、リードタイムの点で飛躍的な進歩を遂げています。以前は1回の反復に半年ほどかかっていたのが、今では数日で済むようになった。その上、製造チェーン全体がアリアングループの社内で展開される。一言で言えばミッション達成
メリット
- -131日反復
- -247 単一部品の機能統合
- -50%のコスト削減
EOSイノベーションストーリー
EOSの30年にわたる3Dプリンティングのパイオニアとしての卓越性をご覧ください。