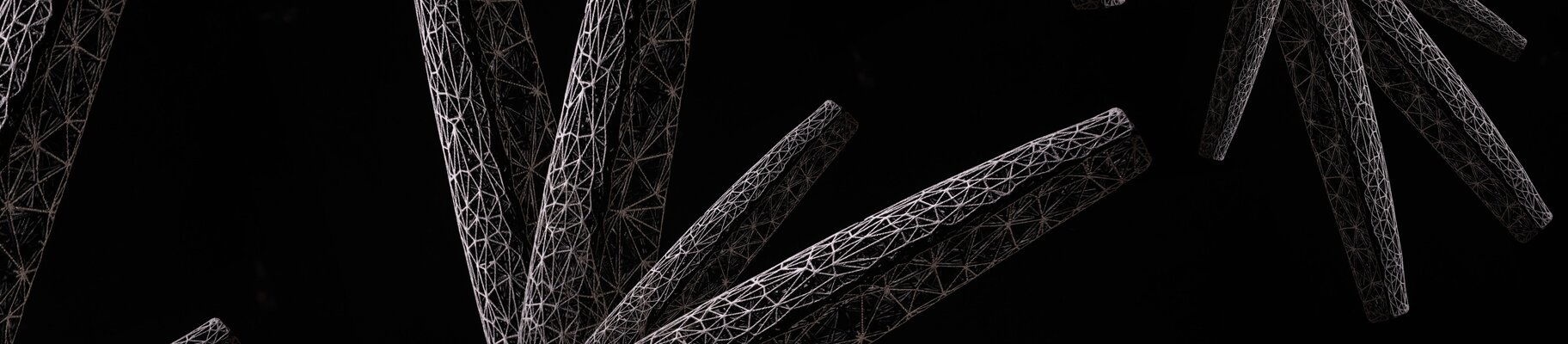
NextGen AM - Automatisierter 3D-Druck erweist sich als voller Erfolg
Gemeinsames Projekt von Premium AEROTEC, EOS und Daimler zeigt großes Potenzial für die Produktion von Ersatz- und Serienteilen.
____ Augsburg/Varel, Krailling, Stuttgart, 30. April 2019
Was im Mai 2017 als vielversprechende Vision begann, hat nun einen erfolgreichen Abschluss gefunden: das Projekt"NextGenAM" zur Entwicklung einer Pilotproduktionslinie für ein automatisiertes "Additive Manufacturing" Verfahren der nächsten Generation durch die Partner Premium AEROTEC, EOS und Daimler.
Das 3D-Druckverfahren, das auch als "Additive Manufacturing" (AM) bezeichnet wird, wird als ergänzendes oder alternatives Verfahren zu herkömmlichen Fertigungstechniken immer interessanter. Die Technologie wird als "additiv" bezeichnet, weil bei diesem Verfahren Schicht für Schicht ein dünnes Material aufgetragen wird, das dann durch eine Energiequelle gehärtet wird. Neben Kunststoffen und Keramiken ist es auch möglich, Metallteile im 3D-Druckverfahren herzustellen.
Ziel des Pilotprojekts war es, eine digitalisierte Fertigungslinie der nächsten Generation zu entwickeln, mit der sich Aluminiumbauteile für die Automobil- und Luftfahrtindustrie deutlich kostengünstiger herstellen lassen als bisher. Das erfolgreiche Ergebnis von NextGenAM: Bezogen auf den gesamten Produktionsprozess bei Premium AEROTEC konnten die Herstellungskosten im Vergleich zu bestehenden 3D-Drucksystemen um bis zu 50 Prozent gesenkt werden.
"Die Automatisierung ist eine der wichtigsten Triebfedern unserer Strategie, die es ermöglicht, unsere Systeme in automatisierte Produktionslinien wie POLYLINE zu integrieren. Und das ist wichtig, um die Kosten pro Teil zu senken und die richtige Qualität in der gesamten Produktionskette zu gewährleisten.
Die Ermöglichung der Serienfertigung ist einer der Hauptgründe für die Gründung von DyeMansion, und genau dafür sind unsere Systeme gebaut, um die Nachbearbeitung auf dieses Niveau zu bringen. Die Powershot DUAL Performance wurde für die Skalierung gebaut, so dass sie zehn oder sogar mehr Drucker in der Produktion bedienen kann und somit eine End-to-End-Fabrik möglich macht. Die wichtigste Erkenntnis dabei ist, dass eine durchgängig automatisierte Fabrik mit 3D-Druck möglich ist. Das erfolgreiche POLYLINE-Projekt zeigt, was möglich ist, und das ist erst der Anfang."
Dr. Thomas Ehm, Vorsitzender der Geschäftsführung von Premium AEROTEC
Vollständig automatisierte Produktion
Das Geheimnis liegt in einer ausgeklügelten und skalierbaren additiven Produktionskette, die bis zu dem Punkt, an dem die gedruckten Teile mechanisch von der Bauplattform abgetrennt werden, vollständig automatisiert ist. Das bedeutet, dass in keiner Phase des Prozesses mehr manuelle Arbeit erforderlich ist, von der Datenaufbereitung und der zentralen Pulverversorgung bis hin zum AM-Build-Prozess selbst, einschließlich Wärmebehandlung, Qualitätssicherung und Trennung der Bauteile von der Bauplattform. Das technische Herzstück der Anlage ist das Vier-Laser-System EOS M 400-4 für den industriellen 3D-Druck mit metallischen Werkstoffen. Ein fahrerloses Transportsystem und Roboter sorgen für die reibungslose Bewegung der Teile durch jede Stufe der Produktionslinie.
Der gesamte Produktionsprozess läuft ohne Bedienpersonal von einer zentralen, autonomen Leitstelle aus. Grundlegend für das System ist die Art und Weise, wie alle eingesetzten Maschinen vernetzt sind. Die Daten der Bauaufträge werden an den Leitstand übermittelt, der dann die verschiedenen Bauaufträge priorisiert und einem AM-System zuweist. Während des Bauprozesses kann der Fertigungsstatus auch ortsunabhängig auf einem mobilen Gerät abgerufen werden. Nach Abschluss der gesamten Produktionskette werden die Qualitätsberichte zentral an den Leitstand zurückgesendet. Hier sind alle für die Erstellung eines digitalen "Zwillings" notwendigen Daten abrufbar, was unter anderem eine lückenlose Rückverfolgbarkeit ermöglicht.
Kapazität kann erweitert werden
Ein durchgängiger 3D-Datenstrang mit integriertem Qualitätsmanagement macht dieses Produktionssystem zu einem der ersten Beispiele für den Maßstab der Zukunft, Industrie 4.0. Der Fertigungsprozess ist vollständig skalierbar: Die Produktionslinien können einfach dupliziert werden, um die Kapazität der Anlage zu erweitern. Das verspricht für die Zukunft weitere erhebliche Einsparungen, wenn die Stückzahlen steigen. Die Pilotanlage ist bereits heute in der Lage, Bauteile in Serienqualität automatisiert zu fertigen.
Auf der neuen Technologielinie bei Premium AEROTEC werden bereits Teile für Daimler produziert: Der Lkw-Bereich zum Beispiel nutzt bereits das erste bei Premium AEROTEC gefertigte Ersatzteil. Dabei handelt es sich um eine Halterung für einen Lkw-Dieselmotor.

Ersatzteile für Lkw und Busse
Gerade im Ersatzteilbereich bietet sich das 3D-Druckverfahren an, da im Falle eines Werkzeugproblems selten benötigte Teile oft kostengünstiger reproduziert werden können als mit herkömmlichen Sand- oder Druckgussverfahren. Erste Anfragen für 3D-gedruckte Busersatzteile aus Aluminium werden derzeit im Kompetenzzentrum für 3D-Druck bei Daimler Buses geprüft. Auch das Analyseteam im Pkw-Bereich prüft derzeit geeignete Einsatzmöglichkeiten.
Möglichkeiten für Kleinstserien und Vorentwicklung
"Additive Manufacturing eignet sich auch für die Kleinserienfertigung von neuen Fahrzeugen (Limited Editions). Durch die systematische Entwicklung der Teile speziell für den 3D-Druck können die Produktionskosten weiter gesenkt und die Qualität optimiert werden. Besonders sinnvoll ist der 3D-Druck auch bei der Vorentwicklung von Fahrzeugen. Die geringen Stückzahlen, die benötigt werden, lassen sich mit Additive Manufacturing oft kostengünstiger und schneller herstellen als mit konventionellen Produktionsverfahren."
Jasmin Eichler, Leiterin Zukunftstechnologien bei der Daimler AG
Und das gilt für Fahrzeuge mit Verbrennungsmotor genauso wie für Elektroautos. Der 3D-Druck eignet sich zum Beispiel auch hervorragend für die Herstellung der integrierten Bodenplatten, die die Kühlleitungen für die Batterien in Elektrofahrzeugen tragen.
Hohe Produktqualität als Standard
Hohe Produktqualität ist in der Pilotanlage Standard: Auch die Verwendung einer hochfesten Aluminium/Magnesium/Scandium-Legierung (auch bekannt als Scalmalloy®) für Teile, die in der Luft- und Raumfahrt verwendet werden, ist vorgesehen.
Für den Automobilbereich wird eine klassische Aluminiumlegierung (AlSi10Mg) verwendet, deren Materialeigenschaften im Laufe des Pilotprojekts kontinuierlich verbessert wurden. Unter anderem konnten die Materialfestigkeit und die Oberflächenqualität im Vergleich zum Beginn der Zusammenarbeit vor zwei Jahren deutlich verbessert werden.
Ausblick: 3D-Druck als Produktionsverfahren mit guten Aussichten
Nachdem alle bisherigen Qualitätsprüfungen mit so vielversprechenden Ergebnissen bestanden wurden, laufen die Vorbereitungen für ein Audit nach den Anforderungen des strengen Industriestandards VDA 6.3. Dies ist eine der Voraussetzungen bei Daimler für die Lieferung von Serienbauteilen durch Lohndruckanbieter. Die Automatisierung der gesamten AM-Produktionskette wird es künftig ermöglichen, größere Stückzahlen in Serie zu fertigen - mit der gleichen Zuverlässigkeit, Funktionalität, Langlebigkeit und Wirtschaftlichkeit wie bei konventionell gefertigten Bauteilen. Bauteile für neue Fahrzeuge können bereits in der Designphase für den 3D-Druck optimiert werden, was weitere Kostenvorteile verspricht. Der 3D-Druck bietet auch Gewichtsvorteile, die besonders für Elektrofahrzeuge interessant sind. Bei den Ersatzteilen bietet der 3D-Druck den Vorteil, dass künftig Lagerkosten eingespart werden können, da die Teile stattdessen "on demand" produziert werden können. Diese Zukunftsvision wird bei Daimler auch als "Digital Stock" bezeichnet, also die zentrale Verfügbarkeit digitaler Fertigungsdaten, die eine dezentrale Produktion von Ersatzteilen mittels 3D-Druck ermöglichen.
Wie Sie sehen, ist der 3D-Druck auf dem besten Weg, sich in der Automobil- und Luftfahrtbranche als zusätzliches, sehr vielseitiges und vergleichsweise junges Produktionsverfahren weiter zu etablieren.

Projektpartner
Premium AEROTEC
Premium AEROTEC ist der erste Komponentenhersteller der Welt, der 3D-gedruckte Bauteile aus Titanlegierungen für die Serienproduktion von Airbus-Flugzeugen liefert. Das Unternehmen ist ein Global Player in der Luftfahrtbranche. Sein Kerngeschäft ist die Entwicklung und Herstellung von Flugzeugstrukturen aus Metall und Kohlefaserverbundwerkstoffen. In Deutschland unterhält das Unternehmen Standorte in Augsburg, Bremen, Hamburg, Nordenham und Varel. Premium AEROTEC hat hier die Verantwortung für den gesamten Produktionsprozess des Gemeinschaftsprojekts übernommen.
______________
EOS
EOS ist der weltweit führende Technologieanbieter im Bereich des industriellen 3D-Drucks von Metallen und Polymeren. Das 1989 gegründete, unabhängige Unternehmen ist Pionier und Innovator für umfassende Lösungen in der additiven Fertigung. Das Produktportfolio aus EOS-Systemen, Werkstoffen und Prozessparametern verschafft den Kunden entscheidende Wettbewerbsvorteile in Bezug auf die Produktqualität und die langfristige wirtschaftliche Nachhaltigkeit ihrer Fertigungsprozesse. Im Rahmen des Gemeinschaftsprojekts lieferte EOS die komplette 3D-Drucktechnologie und die dazugehörigen Softwarelösungen sowie das Kontrollzentrum zur Verknüpfung und Steuerung der Produktionskette.
______________
Daimler
Daimler brachte seine Erfahrung in der Großserienfertigung in das Projekt ein. Forschung und Vorentwicklung arbeiteten sehr eng zusammen. Dabei ging es unter anderem um die Musterbauteile, die rechnerische Robustheit und die Digitalisierung der Bauteildaten für den gesamten Produktionsprozess. Die Erprobung der Musterbauteile wurde ebenso vom Automobilhersteller übernommen wie die Erstellung eines standardisierten Lastenheftes für den 3D-Druck. Darüber hinaus war Daimler für die Überwachung der Validierung und Zertifizierung nach VDA 6.3 im Hinblick auf die Serienfertigung verantwortlich.
Herunterladen
-
Eine Halterung für einen LKW-Dieselmotor, hergestellt im Rahmen des NextGenAM-Projekts.
JPG 2,74 MB -
Im Zentrum der Pilotproduktionskette steht das Vierlasersystem EOS M 400-4 für den industriellen 3D-Druck mit metallischen Werkstoffen.
JPG 881,07 kB