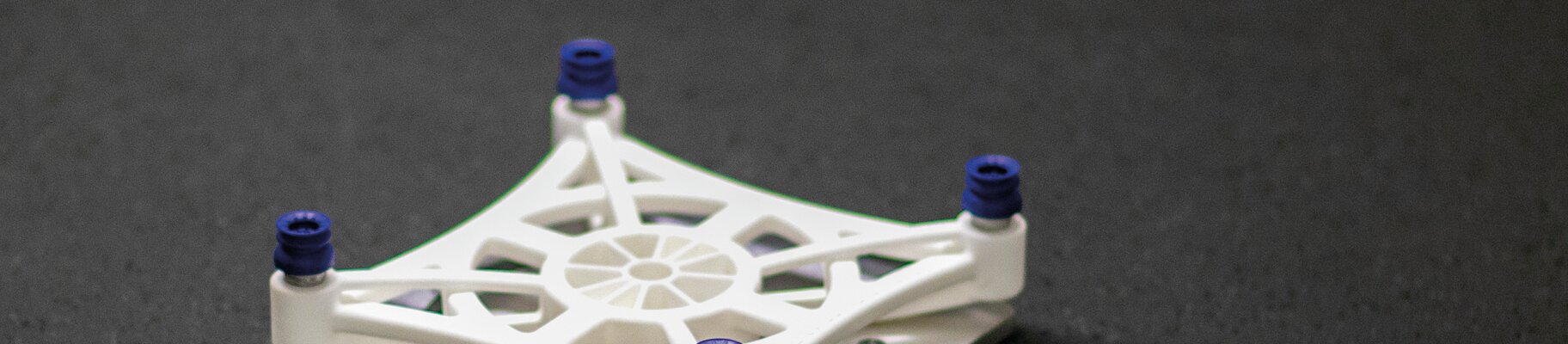
SSI Schäfer mehr Sicherheit durch passgenaue Lösungen
SSI Schäfer | Erfolgsgeschichte
Additive Fertigung für Absauggreifer bei SSI Schäfer
Lagern, Fördern und Transportieren, Kommissionieren, etc. - SSI Schäfer ist ein Spezialist, wenn es um modulare Lager- und Logistiksysteme und die dazugehörige Software geht. Für den Produktionsprozess von Lager-, Transport- und Kommissionierbehältern suchte das Unternehmen nach einer kostengünstigeren und vor allem zuverlässigeren und reibungsloseren Entnahme von Behältern aus seinen Spritzgussmaschinen. Die Lösung war das additive Fertigungsverfahren.
"Unsere Anforderungen waren sehr klar: Zuverlässigkeit und
Zuverlässigkeit und Geschwindigkeit mussten mit dem Umbau der
der Greifer erhöhen. Mit der additiven Fertigung
unserer Greifersysteme konnten wir dieses Problem lösen
dieses Problem lösen und die Kosten senken. Ich bin sehr zufrieden
mit dem Ergebnis und mit der Unterstützung durch das
EOS Additive Minds Team."
Kasim Mohamed | Produkt- und Innovationsmanager | SSI Schäfer

Herausforderung
Herstellung von individuellen Spezialgreifern mit integrierten Luftkanälen für die Produktentnahme aus Spritzgießmaschinen im Produktionskreislauf.
Ausfall von IT-Systemen, menschliches Versagen... die Liste der möglichen Gründe für einen Produktionsausfall ist lang. Weit weniger spannend, aber im Betriebsalltag noch relevanter als Katastrophenszenarien, sind die Tücken der produktionsimmanenten Prozesse selbst. So auch bei SSI Schäfer: Das Unternehmen fertigt seine Lager-, Kommissionier- und Transportkästen seit vielen Jahren mit einem universell einsetzbaren Aluminium-Greifsystem.
Diese "Metallhände" bestanden aus Aluminiumprofilen mit Aufnahmen für Saugnäpfe. Dieser Mechanismus wurde mit Hilfe von Sechskantschrauben eingestellt - je nach Art des hergestellten Behälters immer wieder neu.
Entscheidend ist dabei die Präzision: Die Sauger müssen genau in der richtigen Position stehen, damit die Behälter während des Produktionszyklus leicht und schnell aus der Spritzgießmaschine entnommen werden können. Geschieht dies nicht, besteht die Gefahr, dass der Behälter kippt, was zu einem Produktionsstillstand führen kann. Auch ohne diesen "Worst Case" ist klar, dass die wiederkehrenden Kosten für das Umrüsten erheblich sind:
"Aufgrund unseres großen Produktportfolios müssen wir etwa dreimal am Tag eine unserer vielen Spritzgießmaschinen umrüsten".
Michael Zander, Leiter der Kunststoffproduktion in Neunkirchen / Siegerland (Deutschland)
Angesichts dieser Tatsache ist es leicht zu verstehen, warum das Unternehmen das Verfahren verbessern wollte. Dafür gab es noch einen weiteren Grund: Mit einer besseren Lösung konnten die Kosten nicht nur indirekt, sondern auch direkt gesenkt werden. Und zwar, indem die Rüst- und Stillstandszeiten der Spritzgießmaschinen grundlegend reduziert wurden.
Lösung
Additive Fertigung von mehreren Greiferserien aus PA 2200 auf einer EOS P 396
Mit Unterstützung der technischen Berater von EOS Additive Minds konnte das Team von SSI Schäfer in kurzer Zeit Wissen aufbauen und fand gezielt dieses Verbesserungspotenzial: Der fehleranfällige Aluminiumgreifer sollte durch mehrere dedizierte Greifer ersetzt werden, die jeweils individuell an die jeweiligen Schachtelgrößen und -formen angepasst sind. Diese sollten langlebig, schnell austauschbar und optimal an die jeweiligen Anforderungen angepasst sein. Der Grundgedanke ist also ähnlich wie im Sport: Ein Zehnkämpfer ist zwar ein beeindruckender Athlet, aber die Experten in ihren Einzeldisziplinen sind ihm meist deutlich überlegen. Diesem Gedanken folgend, machten sich EOS und SSI Schäfer an die Arbeit.
Die Konstruktion der passenden Greifer war relativ einfach, da alle Daten der Behälter im Haus vorhanden waren. Wichtig war auch, alte Konstruktionswege zu verlassen und die besonderen Fähigkeiten des 3D-Drucks optimal zu nutzen: Die Integration der Luftkanäle in den Greifer, die wiederum die Basis für den pneumatischen Greifmechanismus zur Entnahme der Behälter bilden, ist eine der Besonderheiten der additiven Fertigung. Aufgrund der kompakten Größe und des geringen Gewichts des Greifers war es zudem notwendig, die Bauteile so zu gestalten, dass Stabilität und Funktion miteinander harmonieren. "Letztlich ist eine solche Konstruktion immer ein Kompromiss", erklärt Werkzeugbauleiter Torsten Kosiahn. Der dafür gewählte Werkstoff PA 2200 hat sich dank seines ausgewogenen Eigenschaftsprofils in tausenden von Anwendungen bewährt: fest, steif, chemikalienbeständig, langlebig. Darüber hinaus ermöglicht es einen hohen Detaillierungsgrad und umfangreiche Nachbearbeitungsmöglichkeiten - kurzum: ideal für Funktionsteile und bewegliche Verbindungen. Die Greifer wurden auf einer EOS P 396 hergestellt.

Ergebnisse
Auf diese Weise konnte SSI Schäfer eine Vielzahl von Greifern in nur wenigen Tagen konstruieren und bauen. Und sie haben die Umrüstzeiten drastisch reduziert: Ein paar Klicks genügen jetzt, um einen Greifer zu bekommen, der perfekt auf den jeweiligen Euro-Behälter abgestimmt ist. Das macht sich auch in Zahlen bemerkbar. Durch den Ansatz wurden die Rüstzeiten um 80 % reduziert und ca. 120 Stunden Produktionszeit pro Jahr gewonnen. Kaum in Zahlen auszudrücken sind die möglichen Folgekosten, wenn ein gravierender Fehler in der Greifereinstellung zu einem längeren Ausfall geführt hätte, denn bei der manuellen Feinabstimmung der alten Greifer war die Gefahr von Fehlbedienungen immer im Hintergrund vorhanden. Durch eine entsprechende Umgestaltung der Greifer ist dies nahezu ausgeschlossen - die Sauger sind nun immer zuverlässig in der richtigen Position.
Die neuen Greifer sind außerdem aufgrund ihres Materials um mehr als die Hälfte leichter als die alten Greifer. Diese Gewichtseinsparung von mehr als 70 % und die erhöhte Bedienerfreundlichkeit kommen natürlich auch dem Personal zugute, das die Umrüstungen vornimmt. SSI Schäfer hat alle seine Ziele erreicht: höhere Zuverlässigkeit, geringere Kosten und Gewichtseinsparungen sowie eine Steigerung der Produktivität.

Die Ergebnisse
auf einen Blick
-
Leicht: Gewichtsreduzierung der Greifer um mehr als 70 %
-
Effizient: Reduktion der Rüstzeiten um 80 % Erhöhung der Produktionszeit um ca. 120 Stunden pro Jahr
-
Schneller: Beschaffungszeit für Greifer von mehreren Wochen auf wenige Tage verkürzt
-
Vereinfacht: Funktionsintegration reduziert Montageaufwand und Anzahl der Einzelteile von 18 auf 6