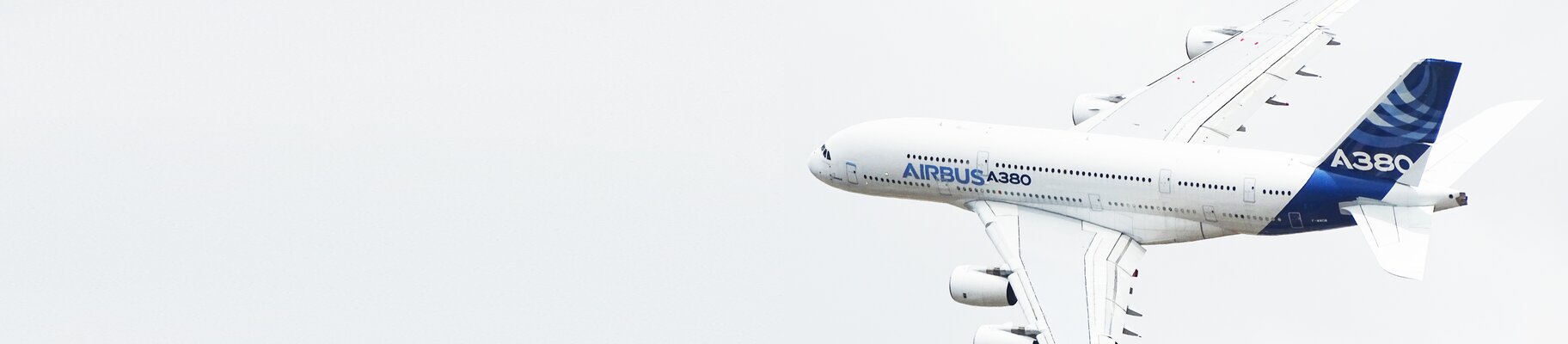
Liebherr | Erstes 3D-gedrucktes Hydraulikbauteil für die primäre Flugsteuerung aus Metall
Fliegt mit einem Airbus A380 | Erfolgsgeschichte
"Wir glauben, dass in einigen Jahren 3D-gedruckte Metallteile wie der Ventilblock bei Lieberr-Aerospace in Serie gefertigt und an unsere Kunden geliefert werden. Der 3D-gedruckte Ventilblock hat bewiesen, dass die additive Fertigung mit der EOS-Technologie für die Herstellung kritischer primärer Flugkomponenten machbar ist."
Alexander Altmann | Lead Engineer Additive Fertigung, Forschung & Technologie | Liebherr-Aerospace Lindenberg GmbH
Herausforderung
Ersatz einer konventionellen primären Flugsteuerungs-Hydraulikkomponente durch ein additiv gefertigtes Teil, das alle Zulassungsanforderungen für den Flug erfüllt
Vor dem Hintergrund eines wachsenden Umweltbewusstseins, steigender Treibstoffpreise und eines Mangels an alternativen Energiequellen muss die Luft- und Raumfahrtindustrie neue Technologien finden, um wettbewerbsfähig zu bleiben. Der pulverbettbasierte industrielle 3D-Druck hat das Potenzial, einen grundlegenden Wandel herbeizuführen und innovative Komponenten zu ermöglichen. Liebherr hat sein Programm zur additiven Fertigung bereits vor sechs Jahren gestartet. Jetzt haben sie bewiesen, dass die EOS-Metall-3D-Drucktechnologie für hydraulische Flugzeugverteiler geeignet ist. Gemeinsam mit Airbus und einem Forschungsteam der Technischen Universität Chemnitz initiierte Liebherr ein vom Bundesministerium für Wirtschaft und Energie (BMWi) gefördertes Projekt.
Ziel war es, ein konventionelles primäres Flugbauteil, einen hydraulischen Hochdruckventilblock, durch ein additiv gefertigtes Bauteil zu ersetzen.
An Bord eines Flugzeugs arbeiten viele Komponenten zusammen, um einen sicheren Flug zu gewährleisten. Ein Spoileraktuator bewegt den Spoiler in die gewünschte Position, um den Auftrieb des Flugzeugs zu verringern. Diese Art von primären Flugsteuerungskomponenten erfordert höchste Qualitäts- und Präzisionsstandards bei der Produktion. Üblicherweise beginnt die Herstellung von Ventilblöcken mit geschmiedetem Rohmaterial, das dann bearbeitet, getrimmt, gebohrt und schließlich zusammengebaut wird. Diese Prozesskette ist zeitaufwändig und komplex und lässt wenig Raum für Optimierungen. Die schiere Anzahl der Prozessschritte verdeutlicht jedoch den Spielraum für mögliche Verbesserungen, die durch den 3D-Druck von Metall erreicht werden können. Das neue Teil muss leichter, ressourceneffizienter und umweltfreundlicher sein, um die Machbarkeit der additiven Fertigung als vielversprechende Zukunftstechnologie zu beweisen.
Lösung
Herstellung eines leichten 3D-gedruckten Bauteils mit weniger Teilen und einer effizienten Prozesskette
Die Lösung war die Entwicklung einer Design- und Prozesskette für die Umsetzung in der Luftfahrtindustrie unter Verwendung der zuverlässigen und hochwertigen industriellen 3D-Drucktechnologie von EOS. Zunächst wurde das konventionelle Teil analysiert. Hydraulische Strukturen wurden identifiziert und Hilfsteile entfernt. Die Positionierung der Hauptkomponenten wurde hinsichtlich ihrer Bauraum- und Schnittstellenanforderungen neu überdacht mit dem Ziel, intelligente, kurze Verbindungsleitungen zu optimieren. Damit war der Grundstein für das Design des neuen Teils gelegt. "Mit dem industriellen 3D-Druck ist Komplexität plötzlich kein Thema mehr. Auf der EOS M 290 Anlage werden Bauteile aus einer Vielzahl von dünnen Schichten mit einer Dicke von jeweils 30 bis 60 μm aufgebaut, was uns den Aufbau komplexer Geometrien ermöglicht", erklärt Alexander Altmann, Lead Engineer Additive Manufacturing, Research & Technology bei der Liebherr-Aerospace Lindenberg GmbH. "Die Funktionselemente wurden über gebogene Rohre direkt miteinander verbunden. Das erspart ein komplexes System von Rohren mit vielen Querbohrungen und spart Zeit in der Produktion."
Das Material der Wahl, eine Titanlegierung, ist für die Luftfahrt besonders geeignet, da es eine Reihe von Vorteilen bietet. Es ermöglicht Gewichtseinsparungen und Kosteneffizienz im Betrieb, da es sehr leicht und mechanisch stabil ist und eine sehr gute Korrosionsbeständigkeit aufweist. Zu den Nachbearbeitungsschritten gehören z. B. eine Wärmebehandlung zum Spannungsabbau sowie eine spezielle Behandlung der Hydraulikkanäle.
Schließlich "darf es nicht den geringsten Zweifel an der Zuverlässigkeit und Sicherheit der Bauteile und des Materials, aus dem sie gefertigt sind, geben. Mit der EOS-Technologie sind wir in der Lage, Titanbauteile in höchster Qualität zuverlässig herzustellen, was eine Voraussetzung für den nächsten Schritt der Serienproduktion ist", erklärt Alexander Altmann.
Additiv gefertigter Ventilblock Made by Liebherr | aufgebaut auf einer EOS M 290: Gleiche Leistung, 35 % weniger Gewicht
Ergebnisse
Der neue additiv gefertigte Ventilblock bietet die gleiche Leistung wie der herkömmliche, ist aber 35 % leichter und besteht aus weniger Teilen. Es war möglich, 10 Funktionselemente in den neuen Ventilblock zu integrieren, wodurch das komplexe Verrohrungssystem mit vielen Querbohrungen entfällt.
"Das könnte auch der Slogan für die additive Fertigung sein - dieselben Dinge mit weniger Masse und weniger Teilen herstellen - aber für uns bei Liebherr-Aerospace ist dies ein bedeutender Schritt", sagt Altmann. Das neue 3D-gedruckte Bauteil wurde nun bei einem Testflug des A380-Flugzeugs erfolgreich erprobt.
Der industrielle 3D-Druck ist im Vergleich zum traditionellen Fräsverfahren weniger komplex und äußerst materialsparend und hilft, den Titanabfall auf ein Minimum zu reduzieren. "Heute dauert die Herstellung eines Ventilblocks etwa einen Tag. Mit der EOS M 400-4 sehen wir das Potenzial, die Bauzeit um mehr als 75 % zu verkürzen", sagt Alexander Altmann.
Doch damit nicht genug: Der leichte 3D-gedruckte Ventilblock und zukünftige 3D-gedruckte Teile werden auch zu einem geringeren Treibstoffverbrauch und reduzierten CO2- und NOX-Emissionen beitragen. Die Anforderungen an Flugzeugkomponenten sind extrem hoch. Deshalb legt Liebherr großen Wert darauf, additive Fertigungsverfahren bis ins Detail zu verstehen, um absolut zuverlässige Produktionsprozesse zu etablieren. Mit EOS hat Liebherr einen Technologieanbieter und Partner, der die Qualitätssicherung im additiven Fertigungsprozess ermöglicht. Durch die Teilnahme an einer Pilotphase konnte Liebherr an der Entwicklung von EOSTATE Exposure OT mitwirken, einem neuen Modul der EOS Monitoring Suite, das eine lückenlose Bauteilprüfung in Echtzeit ermöglicht.
"Dies wird in Zukunft die Erkennung von Materialfehlern im industriellen 3D-Druckprozess beschleunigen und dazu beitragen, nachgelagerte Qualitätssicherungsverfahren wie die Computertomographie zu reduzieren", sagt Alexander Altmann.
Die Ergebnisse auf einen Blick
- -75% Produktionszeit
- -35% Gewichtsreduzierung
- -10 Einzelteile Funktionsintegration
EOS-Innovationsgeschichten
Erleben Sie drei Jahrzehnte Pionierarbeit im 3D-Druck mit EOS