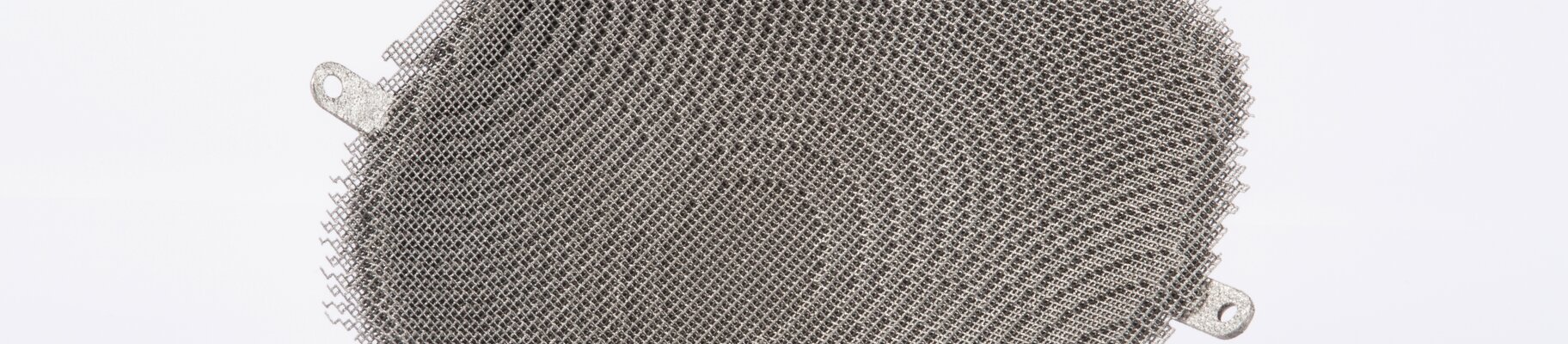
Optimierte Medizinprodukte mit 3D-gedruckten Schädelimplantaten, hergestellt mit EOS Additive Manufacturing
Alphaform | Erfolgsgeschichte
-
Durchlässig für Flüssigkeiten, schützt vor Hitze
-
Großflächiges Implantat trotz poröser Struktur
-
Gitterstrukturen unterstützen das An- und Einwachsen von Knochengewebe
"Additive Fertigung und EOS sind für uns ein und dasselbe. Sowohl wir als auch unsere Kunden sind immer wieder erstaunt über die Anwendungsmöglichkeiten und die hochwertige Produktion, die mit den EOS-Systemen erreicht werden kann. Das war auch hier wieder der Fall. Wir konnten einem Menschen helfen, trotz einer sehr schweren Verletzung ein normales Leben zu führen - und zwar dauerhaft."
Christoph Erhardt | Leiter Additive Fertigung | Alphaform AG
Medizinisches Produkt von Alphaform bietet optimale biomedizinische Eigenschaften für Patienten
Wenn eine Person ein Implantat im Schädelbereich benötigt, sollten äußere Faktoren den Heilungsprozess eher fördern als behindern.
Das schichtweise Produktionsverfahren, bei dem das Material - in diesem Fall Titan - Stück für Stück mit einem Laser gehärtet wird, bietet ein Höchstmaß an Individualisierung in Form und Größe. Für die eigentliche Produktion wurde eine EOSINT M 280 von EOS eingesetzt. Die Bauzeit betrug nur wenige Stunden.
Das perfekt zugeschnittene Implantat erfüllt die individuellen Anforderungen des jeweiligen Krankheitsbildes. Der Porositätsgrad erreichte 95 %, was bedeutet, dass Flüssigkeiten mit dem geringstmöglichen Widerstand hindurchfließen konnten. Darüber hinaus konnte das Knochengewebe die äußeren Ränder des Implantats durchdringen und mit ihm verwachsen. Gleichzeitig ist das Material stabil genug, um dem Patienten das gewünschte Maß an Normalität im täglichen Leben zurückzugeben. Die in Form eines regelmäßigen Gitters aufgebaute Struktur sorgte zudem für die gewünschte Wärmeleitfähigkeit - so kann der Patient auch den Aufenthalt in der Sonne genießen.

"Wir stellen bereits seit 1995 medizinische Implantate her. Additive Manufacturing ist ein neuer Meilenstein für die Patienten. Sie bietet optimale biomedizinische Eigenschaften bei höchster Verträglichkeit und trägt damit nachhaltig zur Verbesserung der Lebensqualität bei. Aus diesen Gründen haben wir die Technologie mit Erfolg auf andere Bereiche des Körpers übertragen. Alphaform hat für uns auch Kieferimplantate, ein Hüftgelenk und ein Wirbelsäulenimplantat hergestellt. Für die Wirbelsäulenimplantate erwägen wir derzeit eine kombinierte Serienfertigung mit Additive Manufacturing."
Daniel Fiz | CEO | Novax DMA
EOS-Erfolgsgeschichten
Erleben Sie drei Jahrzehnte Pionierarbeit im 3D-Druck mit EOS