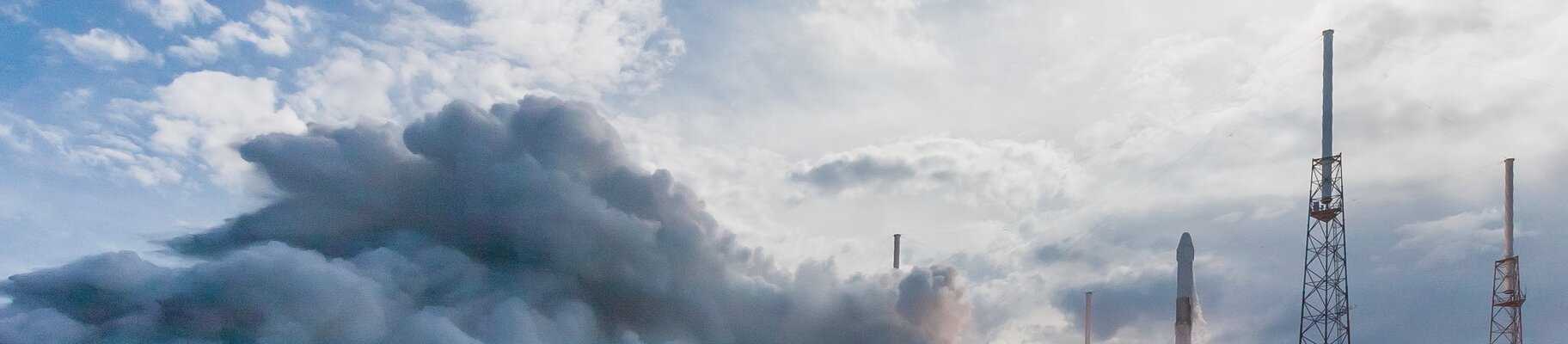
Künftiges Ariane-Antriebsmodul vereinfacht
ArianeGroup | Innovationsgeschichte
All-in-one Design - 122 Einspritzdüsen und weitere Teile als eine integrierte Komponente
"Mission Critical" beschreibt perfekt die in der Luft- und Raumfahrtindustrie verwendeten Komponenten der Klasse 1. Von diesen Bauteilen hängen Missionen ab, die Hunderte von Millionen kosten. Dementsprechend sind die Ingenieure ständig bestrebt, Komponenten von höchster Qualität, Funktionalität und Robustheit zu entwickeln und gleichzeitig die Fertigungskette zu vereinfachen und die Anzahl der einzelnen Elemente zu reduzieren. Dank der additiven Fertigungstechnologie von EOS ist es der ArianeGroup gelungen, dies auf ein völlig neues Niveau zu heben: Statt 248 Elementen besteht der Injektorkopf eines Raketentriebwerks eines zukünftigen Oberstufenantriebsmoduls nur noch aus einem Bauteil. Der Injektorkopf wurde vereinfacht und auf eine buchstäbliche All-in-One-Konstruktion (AiO) reduziert.

"Beim Ariane-Programm kombinieren wir unsere Innovationskraft mit dem Know-how von EOS. Gemeinsam arbeiten wir an der additiven Fertigung eines Einspritzkopfes für ein Raketentriebwerk. Die Ergebnisse sind beeindruckend: Signifikante Verkürzung der Produktionszeit und 50 % geringere Kosten."
Dr.-Ing. Steffen Beyer | Leiter Produktionstechnik, Materialien & Prozesse | ArianeGroup
Herausforderung
Herstellung eines Einspritzkopfes für Raketentriebwerke mit möglichst wenigen Komponenten und geringeren Stückkosten
Die Europäische Weltraumorganisation (ESA) will mit einer effizienten Trägertechnologie eine starke und unabhängige Position im Raumtransport einnehmen. Um dies zu erreichen, wurde die ArianeGroup, ein Joint Venture des europäischen Luft- und Raumfahrtunternehmens Airbus Group und des französischen Konzerns Safran, mit dem Bau der nächsten Generation beauftragt. Ariane ist eine Reihe europäischer Trägerraketen, mit denen schwere Nutzlasten, wie z.B. Kommunikationssatelliten, in die Erdumlaufbahn gebracht werden können.
In einem Antriebsmodul entstehen unter extremen Bedingungen enorme Kräfte. Das erfordert ein Höchstmaß an Zuverlässigkeit und Präzision auf kleinstem Raum. Der Einspritzkopf ist eines der Kernelemente des Antriebsmoduls und führt das Kraftstoffgemisch in den Brennraum ein.
Die traditionelle Konstruktion besteht aus 248 Komponenten, die in verschiedenen Fertigungsschritten hergestellt und zusammengefügt werden. Die verschiedenen Bearbeitungsschritte wie Gießen, Löten, Schweißen und Bohren können zu Schwachstellen führen, die bei extremen Belastungen ein Risiko darstellen. Zudem ist der Prozess zeitaufwändig und komplex. Im Bereich der Injektorelemente müssen in der konventionellen Fertigung über 8.000 Querbohrungen in Kupferhülsen gebohrt werden, die dann präzise mit den 122 Injektorelementen verschraubt werden, um den durchströmenden Wasserstoff mit Sauerstoff zu vermischen.
Ein Blick auf diese Zahlen zeigt deutlich, dass ein funktional integriertes Bauteil, das alle Elemente vereint, das naheliegende, aber ehrgeizige Ziel sein muss. Dies könnte auch ein erhebliches wirtschaftliches Potenzial freisetzen und die Anzahl der Verarbeitungsschritte sowie die Produktionszeit verringern, insbesondere für ein Bauteil der Klasse 1.
Lösung
Ein additiv gefertigtes Produkt, das dank der Funktionsintegration aus einem einzigen Element anstelle von 248 Einzelteilen besteht
Die Lösung für diese Herausforderungen bietet die additive Fertigung. "Die Herstellung des Injektorkopfes in einem Stück ist mit der EOS-Technologie möglich", erklärt Dr.-Ing. Steffen Beyer, Leiter Produktionstechnik - Werkstoffe & Prozesse bei der ArianeGroup, die Entscheidung für den industriellen 3D-Druck. "Nur die additive Fertigung kann integrierte Funktionalität, Leichtbau, ein einfacheres Design und kürzere Lieferzeiten in einem einzigen Bauteil vereinen." Als Werkstoff wählte das Projektteam erneut eine hitze- und korrosionsbeständige Nickelbasislegierung (IN718). Dieser Werkstoff bietet eine hervorragende Zug-, Dauer-, Kriech- und Bruchfestigkeit bei hohen Temperaturen und wird auch bei der neuen Fertigungstechnologie zum Einsatz kommen.
"Nach der erfolgreichen Entwicklung des Bauteils haben wir unser Augenmerk auf die Kosteneffizienz gerichtet", berichtet Dr. Fabian Riss, Produktionstechnik - Materialien & Prozesse. Die zentrale Vorgabe der ArianeGroup war es, die Durchlaufzeiten und Stückkosten zu reduzieren. Die Fertigung erfolgte zunächst in einem inkrementellen Verfahren mit der EOS M 290. Nach erfolgreichen Pilotversuchen wurde die Produktion auf das größere System EOS M 400-4 ausgeweitet. Dank der 4-Laser-Technologie konnte das Bauteil des Antriebsmoduls bis zu viermal so schnell gefertigt werden. "Die Ausweitung des Bauprozesses auf das hochproduktive System EOS M 400-4 war für uns ein wichtiger Schritt, um die Industrialisierung und Wettbewerbsfähigkeit des Ariane-Projekts voranzutreiben. Die Zusammenarbeit verlief dank der Erfahrung und Branchenkenntnis der EOS-Mitarbeiter sehr effizient. Die Ergebnisse sprechen für sich und sind ein Beweis für eine großartige Teamleistung", ergänzt Dr. Steffen Beyer.
Ergebnisse
Das Ergebnis des neuen, additiv gefertigten Injektorkopfes kann sich sehen lassen: Statt aus 248 Teilen besteht er nur noch aus einem - bei gleicher Funktionalität und minimaler Zeitersparnis.
Mit der pulverbettbasierten, industriellen 3D-Drucktechnologie von EOS konnten zum Beispiel die 122 Einspritzdüsen, die Grund- und Frontplatte sowie der Verteilerdom mit den entsprechenden Zuleitungen für die Brennstoffe Wasserstoff und Sauerstoff als ein integriertes Bauteil gedruckt werden. Die deutlich höhere Produktivität des Multilasersystems EOS M 400-4 konnte im Vergleich zu Einlasersystemen die Bauzeit um den Faktor 3 und die Kosten am Beispiel des AiO-Injektorkopfes um 50 % senken.
Das Projektteam konnte eine ganze Reihe von zusätzlichen Erfolgen verbuchen. Die vereinfachte Konstruktion und die verbesserten Materialeigenschaften im Vergleich zur Qualität von Gussteilen erlaubten es der additiven Technologie, die Wandstärke deutlich zu reduzieren - ohne dabei an Festigkeit zu verlieren.
Eine deutliche Gewichtsreduzierung bedeutet auch eine weitere Reduzierung der Bauzeit und natürlich der Kosten.
Nicht zuletzt ermöglichen additive Fertigungsverfahren eine erhebliche Beschleunigung der Innovationszyklen. Strukturelle Verbesserungen, Konstruktionsänderungen und die Herstellung von Testbauteilen in der Entwicklungsphase können auf der Grundlage von CAD-Daten direkt in die Produktion überführt werden, ohne dass die Ingenieure Zeit für die Vorbereitung von Werkzeugen aufwenden müssen, wie es beim Gießen von Teilen der Fall ist. Der industrielle 3D-Druck erreicht damit einen Quantensprung in der Vorlaufzeit. Während früher jede Iteration in der Regel etwa ein halbes Jahr in Anspruch nahm, dauert eine Iteration heute nur noch wenige Tage. Hinzu kommt, dass die gesamte Fertigungskette nun im Hause der ArianeGroup abläuft. Kurz und gut: Mission erfüllt!
Vorteile
- -131 Tage Iteration
- -247 Einzelteile Funktionsintegration
- -50% Kostenreduzierung
EOS-Innovationsgeschichten
Erleben Sie drei Jahrzehnte Pionierarbeit im 3D-Druck mit EOS