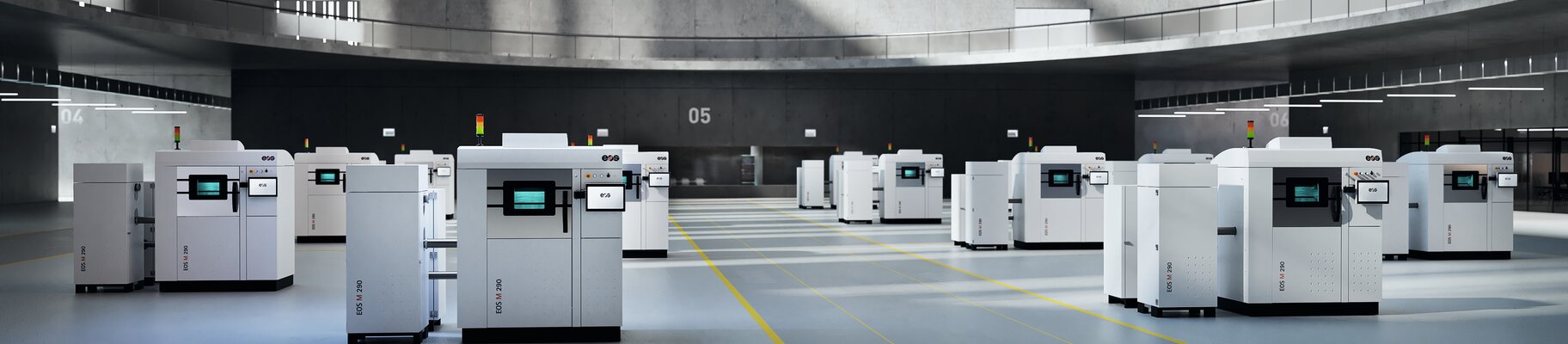
Wie bringt man ein Teil in die Serienproduktion?
22. Juli 2021 | Lesedauer: 6 min
Die additive Fertigung (AM) hat im Vergleich zur traditionellen Fertigung klare Vorteile, nicht nur in Bezug auf Design und Gewicht, sondern auch im Hinblick auf den ökologischen Fußabdruck der Fertigung und die Dynamik der Lieferketten. Um das volle Potenzial von AM auszuschöpfen, müssen die Hersteller es erfolgreich in ihr Produktionssystem integrieren.
Qualifikationen im Bereich der additiven Fertigung in regulierten Branchen
Auf diesem Weg unterstützt Additive Minds seine Kunden kontinuierlich bei der Identifizierung der richtigen Anwendung mit einem geeigneten Geschäftsszenario, dem Entwurf und der Entwicklung optimaler Fertigungsparameter und der Qualifizierung der Anwendung gemäß branchenspezifischer Standards. Branchen wie die Luft- und Raumfahrt sowie die Gesundheits- und Medizintechnik werden zu Anpassungsführern von AM. Der Einsatz von AM in sicherheitskritischen Anwendungen ermöglicht hohe Standards, die den Präzedenzfall für hervorragende Qualität, Sicherheit und Zuverlässigkeit bilden.
Qualifizierung ist der Prozess des Nachweises, dass [...] ein Verfahren in der Lage ist, [...] die festgelegten Anforderungen zu erfüllen
JEDEC, JEP 148, "Reliability Qualification of Semiconductor Devices Based on Physics of Failure Risk and Opportunity Assessment", April 2004.
Wie funktioniert die Qualifizierung?
"Qualifizierung ist der Prozess des Nachweises, dass [...] ein Prozess in der Lage ist, [...] die festgelegten Anforderungen zu erfüllen" [1]. Jede Branche hat einen ähnlichen Ansatz zur Erfüllung dieser Anforderung. Im Allgemeinen müssen die Hersteller potenzielle Produktionsrisiken in den Griff bekommen und Daten generieren, die belegen, dass der AM-Prozess unter bestimmten Bedingungen wiederholbare Ergebnisse liefern kann.
Nehmen wir als Beispiel eine Turbinenschaufel: Ein Hersteller muss sicherstellen, dass der Prozess konsistent ist und dass die produzierten Schaufeln über einen bestimmten Zeitraum hinweg bestimmten Kräften standhalten (niemand von uns möchte in einem Flugzeug sitzen, während eine Turbinenschaufel bricht).
Die Qualifizierung erfolgt in der Regel in drei Stufen. Bei EOS verwenden wir üblicherweise die Begriffe Installationsqualifizierung (IQ), Betriebsqualifizierung (OQ) und Leistungsqualifizierung (PQ). Diese aus der Medizintechnik stammenden Begriffe sind inzwischen auch in der AM-Branche allgemein akzeptiert.
Installationsqualifizierung (IQ)
Der IQ ist Teil eines von EOS angebotenen Standardverfahrens. Field Service Engineers validieren, dass die Anforderungen an die Maschine und Ausrüstung vor Ort erfüllt werden und dass die Kernkomponenten des Systems gemäß den EOS-Spezifikationen funktionieren. Darüber hinaus wird ein Testauftrag zur Qualitätssicherung erstellt und mit dem Kunden ausgewertet. Alle Ergebnisse sowie die kalibrierten Werkzeuge, die zur Durchführung der IQ verwendet wurden, werden in einem Abschlussbericht dokumentiert.
Operative Qualifizierung (OQ)
Das Ziel der OQ ist es, zu überprüfen, ob der Produktionsprozess kontrolliert wird und die gleichen Ergebnisse liefert. Darüber hinaus muss der Hersteller sicherstellen, dass alle relevanten Parameter innerhalb eines festgelegten Toleranzfensters liegen.
Eine OQ ist ein sehr individueller Prozess, der von den branchenspezifischen Anforderungen abhängt. Für den erfolgreichen Abschluss einer OQ sind zwei Schritte erforderlich:
Einrichtung des Risikomanagementsystems und Durchführung einer Fähigkeitsbewertung. Im Rahmen des Risikomanagements sollte der Hersteller alle mit dem Prozess verbundenen Risiken, die die Leistung des Teils beeinträchtigen könnten, ermitteln und bewerten. Dies setzt voraus, dass der Prozess gründlich definiert ist (vom Wareneingang bis zur Nachbearbeitung) und dass potenzielle Risiken erkannt, bewertet und gemindert werden. EOS-Kunden werden von Additive Minds durch Schulungen und Workshops unterstützt, in denen sie mit den relevanten Schlüsselparametern des Prozesses und den Auswirkungen auf die endgültigen Bauteileigenschaften vertraut gemacht werden (z. B. qualitätskritische Schulungen, Bereitstellung eines AM-Flussdiagramms und einer Prozessdokumentation).
Darüber hinaus bitten die Kunden Additive Minds häufig um zusätzliche technische Informationen über Systeme, Materialien und Prozesse, aber auch darüber, wie EOS interne Verfahren zur Qualitätssicherung durchführt (z. B. wie eine konsistente Software-Validierung vor der Freigabe sichergestellt wird).
Die wichtigste Methode zur Dokumentation und Nachverfolgung der Wirksamkeit einer angemessenen Risikominderung ist eine Prozess-Fehlermöglichkeits- und -Einfluss-Analyse (pFMEA), die Additive Minds als Teil eines OQ-Projekts teilt und anpasst. Kunden aus regulierten Industrien müssen gegenüber den Regulierungsbehörden den Nachweis erbringen, dass sie diese Qualitätsmethodik durchgeführt haben, um sicherzustellen, dass alle Entwicklungsaktivitäten nach modernsten Verfahren durchgeführt wurden.
Der Zweck der betrieblichen Qualifizierung besteht darin, durch strenge Tests die Wirksamkeit und Reproduzierbarkeit des Prozesses nachzuweisen. Voraussetzung dafür ist eine Prozesscharakterisierung zur Bestimmung des Prozessfensters für jede der wichtigsten Prozessvariablen.
ASTM F3434-20, Leitfaden für die additive Fertigung - Installation/Betrieb und Leistungsqualifizierung (IQ/OQ/PQ) von Laserstrahl-Pulverbettschmelzanlagen für die Serienfertigung
Die wichtigste Methode zur Dokumentation und Nachverfolgung der Wirksamkeit einer angemessenen Risikominderung ist eine Prozess-Fehlermöglichkeits- und -Einfluss-Analyse (pFMEA), die Additive Minds als Teil eines OQ-Projekts teilt und anpasst. Kunden aus regulierten Industrien müssen gegenüber den Regulierungsbehörden den Nachweis erbringen, dass sie diese Qualitätsmethodik durchgeführt haben, um sicherzustellen, dass alle Entwicklungsaktivitäten nach modernsten Verfahren durchgeführt wurden.
Zurück zu unserer Turbinenschaufel: Was sollte eine pFMEA abdecken?
Eine fehlende Verschmelzung ist ein Fehler, der die mechanischen Eigenschaften stark beeinträchtigt und bei sicherheitskritischen Anwendungen vermieden werden sollte. Ein möglicher Grund dafür ist der Abfall der Laserleistung aufgrund eines nicht ordnungsgemäß gereinigten Laserfensters.
Um dieses Risiko zu minimieren, können auf Kundenseite verschiedene Abhilfemaßnahmen getroffen werden. Dies könnte eine vorbeugende Arbeitsanweisung zur ordnungsgemäßen Reinigung des Laserfensters beim Einrichten der Maschine oder sogar ein CT-Scan des endgültigen Blatts sein, um etwaige Abweichungen zu erkennen und zu vermeiden.
Der letzte Schritt einer OQ ist die Fähigkeitsstudie. Die Fähigkeitsstudie folgt einem streng vordefinierten Testplan (der von Additive Minds bereitgestellt und angepasst wird). Hier werden alle relevanten Testparameter für alle Prozessschritte definiert. Dazu gehören ein Prozessfenster für jeden Parameter und Akzeptanzkriterien, anhand derer die ursprünglichen Designanforderungen getestet werden. Um die Fähigkeitsstudie erfolgreich zu bestehen, müssen alle Akzeptanzkriterien erfüllt werden, z. B. die Materialeigenschaften, die in den Datenblättern angegeben oder als Teil der Materialnormen anerkannt sind (die Kunden verwenden diese als Referenzpunkt).
Viele Aufsichtsbehörden (FAA/EASA oder FDA/EMA) verlangen von ihren Kunden auch die Durchführung von Versuchsplänen (Design of Experiments, DoE) zur Validierung der Prozessleistung unter ungünstigsten oder extremen Prozessbedingungen.
Schauen wir uns unser praktisches Beispiel an!
Die ASTM F3434 verlangt, dass ein Hersteller alle Bedingungen, die während der tatsächlichen Produktion auftreten, einschließlich der "Worst-Case"-Bedingungen, überprüft. Aufgrund dieser Anforderung können auf Kundenseite verschiedene Fragen auftauchen. Da der Hersteller bei der Markteinführung kritischer Sicherheitsbauteile die volle Verantwortung trägt, ist es notwendig, diese Fragen zu beantworten.
- Wie schnell degeneriert die Laserleistung einer AM-Maschine?
- Was sind die wichtigsten Faktoren, die zu einem Leistungsverlust des Lasers führen können?
- Wie viel Verlust an Laserleistung ist akzeptabel, bis die Anwendung die Konstruktionsanforderungen nicht mehr erfüllt?
- Wie gleichmäßig ist die Laserleistung über die gebaute Platte verteilt und hat z.B. die F-Theta-Linse einen Einfluss auf diese Verteilung?
Nach Abschluss der OQ muss der Herstellungsprozess für eine bestimmte Anwendung qualifiziert werden, d.h. Leistungsqualifizierung.
Die Leistungsqualifizierung (PQ)
Die Leistungsqualifizierung ist der letzte Schritt im Qualifizierungsprozess. "Mit dieser Analyse wird festgestellt, ob die Ausrüstung und die Prozesskontrollen angemessen sind, um sicherzustellen, dass die Produktspezifikation erfüllt wird" [2]. Es wird überprüft, ob alle Prozessschritte zusammengenommen die geforderten Spezifikationen für das Endprodukt erfüllen.
Die PQ kann eine recht kurze Phase innerhalb einer Qualifizierung sein, da ein Großteil der umfangreichen Arbeiten bereits im Rahmen der OQ abgeschlossen wurde. Die PQ schließlich übernimmt und ergänzt den generischen Prozess für eine spezifische Anwendung, z. B. die Turbinenschaufel für einen bestimmten Flugzeugtyp.
Wie die OQ folgt auch die PQ einem strengen Prüfplan, der sich diesmal auf das Teil selbst konzentriert. In der PQ werden Betriebsparameter, Ausrüstungsgrenzen und Komponenteneinsatz definiert. In der Serienproduktion bedeutet dies, dass z. B. das Verfahren für die Handhabung, Aufarbeitung und Wiederverwendung von Pulver klar definiert und umgesetzt werden muss.
Bei der Herstellung von Turbinenschaufeln hat dies mehrere Auswirkungen: Der Hersteller muss Spezifikationen für das recycelte Pulver sowie Anweisungen für die Durchführung der Aufarbeitung festlegen. Es sollten Grenzwerte für die Verschrottung des Pulvers festgelegt werden, da sichergestellt werden muss, dass das Pulver in einem stabilen Zustand verbleibt und sein Status und seine Geschichte ordnungsgemäß dokumentiert werden.
Wie kann man den Prozess qualifiziert halten?
Nach Abschluss der Qualifizierung sollte der Hersteller jede Prozessänderung im Hinblick auf den Schweregrad und die möglichen Auswirkungen auf das fertige Teil bewerten. Auf der Grundlage dieser Bewertung können verschiedene Ansätze für eine erneute Qualifizierung anwendbar sein, um das Verfahren qualifiziert zu halten.
Als Maschinen-OEM kann EOS diese Bewertung nicht durchführen. Dies liegt in der Verantwortung des Herstellers. Durch die Bereitstellung relevanter Informationen für diese Bewertung kann EOS jedoch dazu beitragen, den Aufwand für den Kunden zu verringern und das Vertrauen in die Industrietauglichkeit von Produkten, Prozessen und Organisation zu fördern. Wenn Kunden potenzielle Risiken im Zusammenhang mit neuen Funktionen leichter einschätzen können, ermöglicht dies EOS, den Kunden schnell fortschrittliche, aktualisierte Funktionen und Lösungen anzubieten.
Zusammenfassung
Die Qualifizierung ist eine gängige Praxis in der Serienproduktion. Die Verfahren und Anforderungen an AM sind die gleichen wie bei jeder anderen Produktionstechnologie. Qualifizierte Produkte machen die Luft- und Raumfahrt zu einem der sichersten Transportmittel. Dies ermöglicht es den Kunden, AM für die Serienproduktion zu qualifizieren und mit EOS zu wachsen, um den Einsatz der AM-Technologie in der Zukunft voranzutreiben.