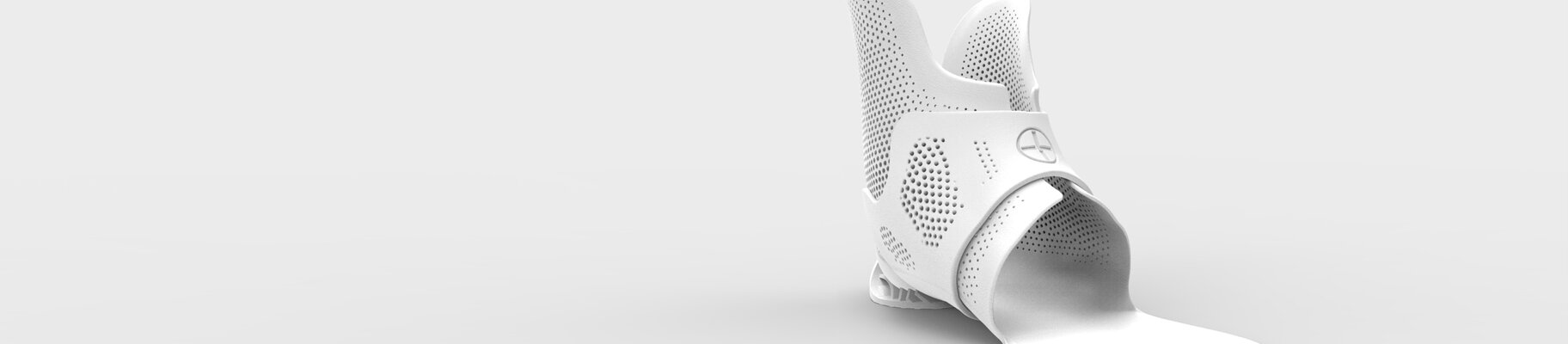
Produktion von Orthesen mit 3D-Scanning und 3D-Druck - maximale Flexibilität und Gestaltungsfreiheit
Ottobock | Erfolgsgeschichte
Komplexe Strukturen und individuelle Gestaltung
"Angenehme Atmungsaktivität: Die Perforationen dieser Knöchel-Fuß-Orthese mit Ringverschluss-System bedecken nahezu die gesamte Oberfläche und verhindern übermäßiges Schwitzen."
Bei Stützorthesen sind Orthopädietechniker in der Regel auf individuelle Konstruktionen beschränkt, da Formen, Funktionen und Materialstärken auf die Bedürfnisse des jeweiligen Patienten abgestimmt werden müssen. Bei komplexen Strukturen stoßen herkömmliche Verfahren oft an ihre Grenzen. Zudem sind Orthesen zeitaufwändig in der Herstellung und nicht ohne Weiteres verfügbar. Ottobock setzt deshalb auf den industriellen 3D-Druck. Mit Hilfe von Produktionssystemen und Beratungsleistungen von EOS stellt das Unternehmen maßgeschneiderte Orthesen her.

"Der Trend in der Medizintechnik geht hin zu maßgeschneiderten Produkten. Mit der EOS-Technologie können wir patientenindividuelle Produkte herstellen und gleichzeitig die Kosten kontrollieren, da wir unsere chirurgischen Kunden schneller beliefern können."
Lukas Eckermann | Leiter Patientenversorgung und iFab (individuelle Fertigung) | Ottobock
Herausforderung
Entwurf, CAD-Konstruktion und Herstellung von Orthesen, die mehrere Funktionen kombinieren und optimal auf die Bedürfnisse des Patienten zugeschnitten sind
Jeder Mensch ist einzigartig. Das gilt besonders in der Orthopädie, wo es darum geht, die Mobilität des Menschen individuell zu unterstützen oder wiederherzustellen. Damit die Behandlung ein voller Erfolg wird, müssen Orthesen genau auf die Anatomie und die therapeutischen Bedürfnisse des Patienten abgestimmt sein. Deshalb werden sie als Sonderanfertigungen oder in individuellen Kleinserien hergestellt, denn bisher orientierten sich die Orthopädietechniker bei der Konstruktion von Orthesen an den Möglichkeiten der traditionellen Fertigungsverfahren wie Gießen, Formen, Modellieren und Fräsen.
Doch komplexe Strukturen und unterschiedliche Materialstärken bringen etablierte Verfahren an die Grenzen ihrer Leistungsfähigkeit. Ist es notwendig, mehrere Funktionen in einem Produkt zu vereinen, müssen einzelne Teile manuell zur fertigen Orthese zusammengefügt werden, was sehr zeitaufwändig ist.
Gleichzeitig müssen Orthesen so schnell wie möglich verfügbar sein, um die Mobilität von Patienten mit neurologischen Grunderkrankungen wie Zerebralparese, Spina bifida oder Lähmungen zu unterstützen. Ein weiterer Faktor bei der Behandlung von Kindern ist, dass sie schnell wachsen und Hilfsmittel daher häufig ausgetauscht werden müssen.
Ottobock hat diese Herausforderungen erkannt und sich zum Ziel gesetzt, die Patientenversorgung durch den Einsatz des industriellen 3D-Drucks zu optimieren. "Wir verbinden manuelles orthopädisches Handwerk mit den Vorteilen der additiven Fertigung", sagt Lukas Eckermann, Leiter Patientenversorgung und iFab (individuelle Fertigung) bei Ottobock.
Lösung
Konstruktion von individuell angepassten Orthesen für Patienten durch industriellen 3D-Druck mit der EOS P 396
Mit der Übernahme von plus medica OT steigt Ottobock in die digitale Produktion von Orthesen ein. Das kleine Start-up entwickelt seit 2015 3D-gedruckte Lösungen. Oberste Priorität für Ottobock ist es, das Potenzial der Technologie zur Verbesserung der Patientenversorgung zu nutzen und für alle Orthopädietechniker in ihrem Netzwerk verfügbar zu machen. Nach jahrelanger wirtschaftlicher und technischer Optimierung von 3D-gedruckten Orthesen mit besonderem Augenmerk auf die Aspekte Form und Funktion hat Ottobock die MyNext MAFO eingeführt. Diese dynamische Knöchel-Fuß-Orthese kombiniert innovative Eigenschaften, die durch die digitale Fertigung ermöglicht werden, mit der Erfahrung von ausgebildeten Orthopädietechnikern. Um jedem Patienten die bestmögliche Unterstützung zukommen zu lassen, ist eine enge Zusammenarbeit mit den Orthopädietechnikern vor Ort sehr wichtig. Nur durch die Abstimmung aller Prozesse in der Konstruktion und der additiven Fertigung auf die Anforderungen der Orthopädietechnik ist es möglich, die bestmöglichen Ergebnisse zu erzielen.
Zu diesem Zweck kooperiert das Unternehmen mit EOS, dem Technologieführer auf dem Gebiet des 3D-Drucks. Das Unternehmen liefert nicht nur die notwendigen Systeme und Materialien, sondern unterstützt die Anwender auch im Entwicklungs- und Produktionsprozess. "Wir haben von der kompetenten und partnerschaftlichen Beratung durch EOS profitiert, zum Beispiel bei der Auswahl des geeigneten Materials", erklärt Lukas Eckermann. Anwendungsspezialisten mit Erfahrung in der Medizintechnik halfen Ottobock beim Aufbau von eigenem Know-how und zeigten, wie man die Möglichkeiten der Technologie voll ausschöpfen kann. Und auch jetzt stehen sie jederzeit für Fragen der Designoptimierung und Funktionsintegration zur Verfügung.
Grundlage jeder 3D-gedruckten MyNext-Orthese ist ein Scan des Fußes des Patienten mit einem Bodyscanner, der von einem Orthopäden angefertigt wird. Anschließend modifiziert er das Scanmodell in einer CAD-Software und sendet es zusammen mit den gewünschten Produktspezifikationen über das iFab Kundencenter, eine digitale Bestellplattform für individuelle Produkte, an Ottobock. Anschließend werden die Konstruktionsdaten an das Produktionssystem, eine EOS P 396, übertragen. Dort wird das Bauteil Schicht für Schicht aus einem feinen Pulvermaterial mit einem Laserstrahl aufgebaut. Auf diese Weise lassen sich Teile in jeder erdenklichen Form herstellen, ohne dass spezielle Werkzeuge benötigt werden. Als Werkstoff wird das Polymer PA 1101 auf Nylonbasis verwendet, das sich durch eine hohe Steifigkeit und Schlagzähigkeit auszeichnet und auch bei starker Belastung weder splittert noch bricht. Dies senkt das Verletzungsrisiko für den Patienten.
Ergebnisse
Die additive Fertigung ermöglicht es Ottobock, mit einem neuen Ansatz Hilfsmittel in höchster Qualität zu produzieren. Komplexe Strukturen können problemlos berücksichtigt werden. Es ist auch möglich, unterschiedliche Materialstärken in eine Orthese einzubauen und damit beliebig dicke oder dünne Wandstärken zu erzeugen. Darüber hinaus ermöglicht die additive Fertigung die Integration unterschiedlicher Strukturen, die bestimmte Bereiche entweder flexibel oder steif machen. Dies gilt auch für Perforationen, die der Verbesserung der Atmungsaktivität dienen. "Es gibt verschiedene Geometrien, geringe Wandstärken und integrierte Funktionen, die wir mit traditionellen Fertigungsmethoden nicht so einfach hätten realisieren können", erklärt Lukas Eckermann. Die Orthesen können besser als bisher auf die Bedürfnisse des Patienten zugeschnitten werden. Auch optisch lässt sich das Gerät relativ einfach und kostengünstig individualisieren.
Zukünftig können durch nachträgliches Färben oder Lackieren Farbvariationen erzeugt werden. Für Lukas Eckermann sind Optimierungen bei Gewicht und integrierten Funktionen, hohe Atmungsaktivität und ansprechendes Design entscheidende Faktoren für den Erfolg einer Versorgung: "Niemand trägt gerne eine Orthese. Aber wenn man sie im Alltag kaum bemerkt und sie auch noch gut aussieht, kann das die Tragedauer und damit den Therapieerfolg der Orthese deutlich erhöhen." Ein weiterer Vorteil der EOS-Technologie ist die leichte Reproduzierbarkeit der Teile: Einmal entwickelt, kann die Orthese jederzeit in gleicher Qualität nachproduziert werden. Dies ist besonders bei Kinderorthesen relevant, die in einer anderen Größe, aber mit gleicher Funktionalität und Struktur ersetzt werden müssen. Der industrielle 3D-Druck ermöglicht Ottobock eine einfache Skalierung seiner Lösung in Bezug auf die produzierten Einheiten sowie die Einführung weiterer Orthesentypen.
Die Ergebnisse auf einen Blick
- Funktional: völlige Gestaltungsfreiheit bei Strukturen, Funktionen und Wandstärken
- Reproduzierbar: Jede einzelne Orthese kann jederzeit mit dem gleichen Aufbau und den gleichen Eigenschaften wieder hergestellt werden
- Bequem: Geringes Gewicht und Atmungsaktivität erhöhen den Tragekomfort
- Standardisiert: gleichbleibende und wiederholbare Produktionsqualität ohne Abhängigkeit von manuellen Qualitätsfaktoren in der Produktion