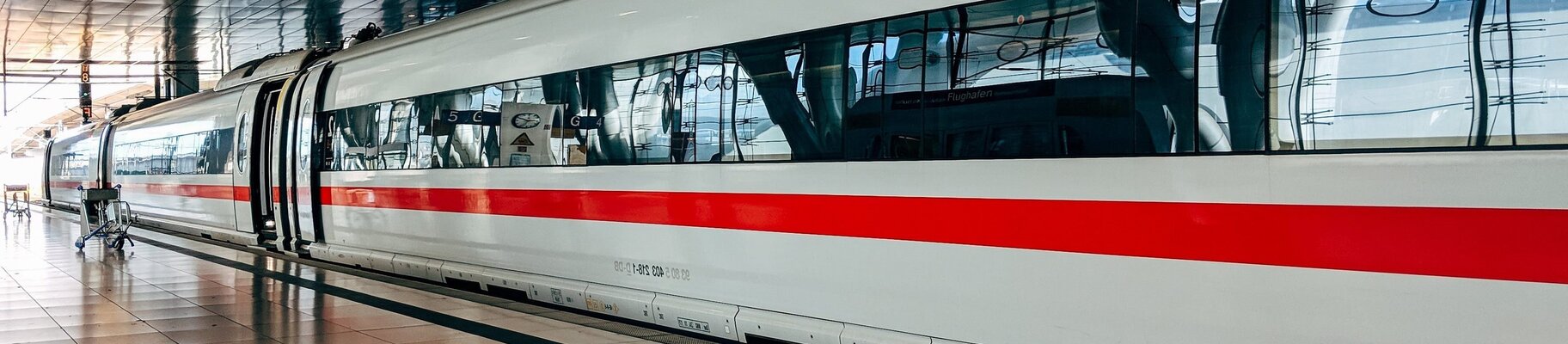
EOSのアディティブ・マニュファクチャリングによる3Dプリントのカスタム列車部品への早道
ハセナウアー&ヘッサー|サクセスストーリー
ドイツ鉄道、車両保守にアディティブ・マニュファクチャリングを採用
ドイツ鉄道が運行する第3世代のICE車両は、さまざまな製造シリーズから160台弱が製造されている。そのスタイリッシュなデザインと定期的に改装される内装のおかげで、どの車両もいまだに現代的な外観を保っている。にもかかわらず、運輸業界では1996年以前に製造されたものはすべてヤングタイマーとみなされている。この時代の自動車と同様、これらの列車のスペアパーツを見つけるのは難しい。しかし、ドイツ鉄道は、EOSの産業用3Dプリンティング技術を駆使して平然としている。

「アディティブ・マニュファクチャリングの大きな利点は、常に新品同様の交換部品を製造できることです。品質や性能で妥協する必要はありません。コストもカスタム金型より低く抑えられます」。
フローレンス・リヒテ|3Dプリンティング部門責任者|DB Fahrzeuginstandhaltung GmbH
チャレンジ
第三世代のICE列車は、少々気の遠くなるような存在だ。非積載重量は270トンから400トンをはるかに超え、走行速度は時速140マイルから190マイルで、各列車に搭載される部品の種類の多さは見過ごされがちである。最も小さな部品が最も難しい場合が多い。標準的な市販のネジは簡単に交換できるが、その他の多くの小さな特注品は、摩耗したり故障したりしても、メーカーから簡単に再注文することはできない。部品によっては生産が中止されていたり、メーカーが倒産していたりするものもある。各部品は通常、数部しか必要とされない。高い工具コストと最低購入数の制限により、従来の方法では不経済である。
160台のバッチは、工業規模の注文に比べれば微々たるものだ。それに比べれば、中型車は年間何十万台も生産されている。航空機でも、短・中距離路線の成功モデルなら年間生産台数は数千台に達する。
これは確かに輸送手段としての列車の持続可能性を示しているが、生産規模が小さいため、スペア部品の生産と倉庫物流が複雑になっている。同様の問題は、他の多くの特殊な部品でも発生する。ここで取り上げた具体例では、ICE-3およびICE-T列車の電子車載情報システム内の表示灯に使用される、非常にデリケートな蛍光管器具の交換部品が必要だった。このモニターは、速度、時刻、次の駅に関する情報を乗客に表示する。
時間の経過とともに、標準的な磨耗や脆性によって9.4 x 0.4 x 0.3インチの射出成形部品は徐々に弱くなり、10年から15年ごとに交換する必要がある。鉄道車両は25年以上の耐用年数を持つように設計されているが、40年から50年、例外的なケースではそれ以上使用されることも珍しくない。にもかかわらず、サプライヤーはこれらの部品の製造中止を決定した。年間約40個が必要とされる。この責任を負った保守会社、ドイツ・ミュンヘンのElectronikzentralwerk (EZW)は、代替品や答えのありそうなパートナーの探索に乗り出した。その結果、鉄道技術の専門家は、積層造形とその可能性にたどり着いた。

ソリューション
積層造形技術は、バッチサイズが小さいことから、完璧なソリューションである。製造ツールのセットアップなど、大がかりな準備作業も必要ない。「私たちの経験に基づけば、同等のアルミ金型と手作業によるアンローディングに基づくソリューションでは、注文ごとのハンドリングとセットアップ費用、金型の年間保管・メンテナンス費用を差し引いても、数千ユーロのコストがかかると予想されます。さらに、金型の製作には3カ月ほどかかり、最初のサンプルの製作にはさらに1カ月かかります」と、DB Fahrzeuginstandhaltung GmbHの3Dプリンティング部門責任者であるフローレンス・リヒテ氏は説明する。
企業が部品の積層造形を希望する場合、自社で産業用3Dプリンターを導入したり、専門知識を身につけたりする必要はありません。これは、ドイツ鉄道が選んだ道だ。ドイツ鉄道のロジスティクス会社は現在、何度もHasenauer & Hesser GmbHとのコラボレーションを成功させている。しかし、問題は細部にあった、とHasenauer & Hesser GmbHのマネージング・ディレクター、ハンス・ヨルグ・ヘッサー氏は語る。そのためには、部品の仕様を再設計し、積層造形プロセスに適合させる必要がありました。通常、3Dプリントは簡単ですが、このプロジェクトでは膨大な経験が要求されました。ICEの列車に使われている部品は、細長く、肉厚が薄い。そのため、驚くほど簡単に反ってしまう。特に、この注文では200個以上のフィクスチャーを同時に作りたかったので、造形室内でのパーツの位置決めは不可欠でした"

"私たちは10年以上の積層造形の経験があり、覚えている限りEOSシステムを使用してきました。部品の品質とシステムの信頼性に満足しています。このシステムのおかげで、一流のスペアパーツをお客様に迅速にお届けすることができます。"
ハンス・イェルク・ヘッサー|マネージング・ディレクター|Hasenauer & Hesser GmbH
結果
フィクスチャーは FORMIGA P 110 で製作された。3D CADデータも設計図面も入手できなかったため、リエンジニアリング工程では4桁台前半の費用がかかった。その結果、製造コストは射出成形よりも80%以上低くなった。このプロジェクトでは、開始から最初の納品まで合計1カ月を要したが、これは3Dプリントされた部品が4倍早く入手できたことを意味する。後続の注文は24時間以内に完了する可能性がある。EZWミュンヘンの従業員自身が、プリントされたパーツの形状、フィット感、機能を現場でテストした。その結果は、非常に納得のいくものでした。付加製造された治具は、クライアントの要求のひとつひとつを満たしていたのです。「部品は完璧にフィットし、ゆがむこともありませんでした。私たちはすでに少なくとも20ユニットを取り付けています」とフローレンス・リヒテは付け加えた。
しかし、ドイツのリヒテ氏と彼の同僚たちは、単に機能試験に合格するだけでなく、もっと心配しなければならないことがあった。鉄道産業で使用されるプラスチックは、EN 45545-2 / DIN 5510-2(既存車両用)に規定された防火要件を満たさなければならない。各コンポーネントのサイズ、重量、車両内の位置、他のコンポーネントとの距離によって、異なる要件が存在し、場合によっては追加の例外もあります。このプロジェクトのために選択されたEOS素材PA 2210 FRは、その用途の特定の要件を満たしていることを確認するために、広範な火災試験を受ける必要がありました。これらの新しい部品は、乗客に最新情報を提供するだけでなく、猛スピードで線路を疾走する乗客の安全を守る。
結果一覧
- 75% 生産時間の短縮
- 80 % 製造コストの削減
EOSサクセスストーリー
EOSの30年にわたる3Dプリンティングのパイオニアとしての卓越性をご覧ください。