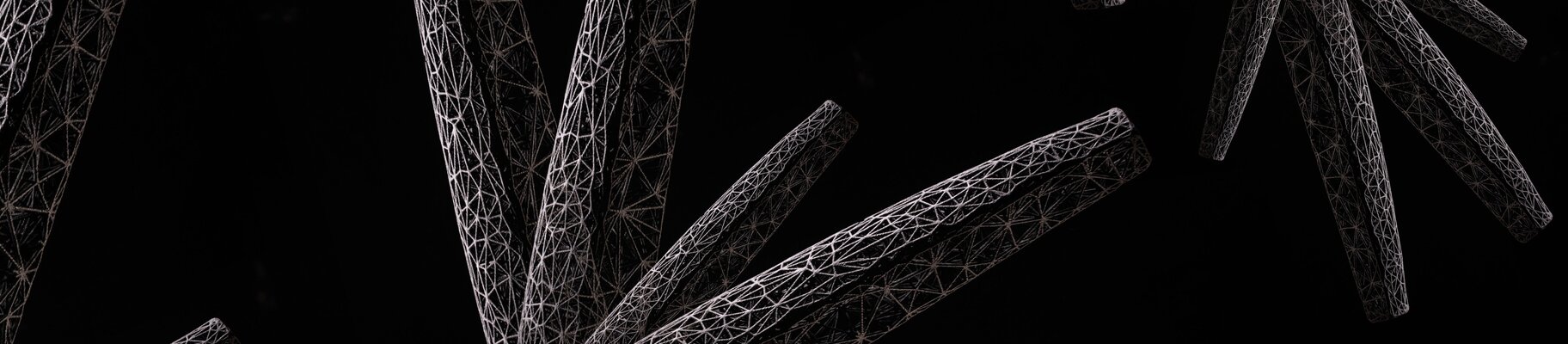
NextGen AM - 自動3Dプリンティングが完全な成功を収める
Premium AEROTEC、EOS、ダイムラーの共同プロジェクトは、交換部品や量産部品の生産に大きな可能性を示している。
アウクスブルク/ヴァレル、クライリング、シュトゥットガルト、30日。2019年4月
プレミアム・エアロテック、EOS、ダイムラーによる次世代自動化「積層造形」プロセスのパイロット生産ライン開発プロジェクト「NextGenAM」である。
アディティブ・マニュファクチャリング」(AM)としても知られる3Dプリンティング・プロセスは、従来の製造技術を補完または代替するプロセスとして、ますます関心を集めている。この技術は、薄い材料を何層にも重ね、それをエネルギー源で硬化させることから「積層造形」と呼ばれている。プラスチックやセラミックとともに、3Dプリンティング・プロセスで金属部品を製造することも可能だ。
このパイロット・プロジェクトの目的は、デジタル化された次世代製造ラインを開発することであり、これにより、自動車および航空宇宙分野向けのアルミニウム部品を、現在よりも大幅にコスト効率よく製造できるようになる。NextGenAMの成功の成果:Premium AEROTECの生産工程全体において、既存の3Dプリンティングシステムと比較して、製造コストを最大50%削減することができた。
「オートメーションは、ポリラインのような自動化された生産ラインに私たちのシステムを統合することを可能にし、私たちの戦略における重要な原動力のひとつです。これは、部品あたりのコストを削減し、生産チェーン全体を通して適切な品質を確保するために重要です。
連続生産を可能にすることは、DyeMansionが設立された主な理由のひとつであり、後処理をこのレベルまで高めるために私たちのシステムが構築されたのです。Powershot DUAL Performanceは、10台、あるいはそれ以上のプリンターの生産に対応し、エンド・ツー・エンドの工場を可能にするために開発されました。ここで重要なのは、3Dプリンターでエンド・ツー・エンドの自動化工場が可能だということです。成功したPOLYLINEプロジェクトは、何が可能かを示しており、これは始まりに過ぎません」。
トーマス・エームPremium AEROTEC会長
完全自動化生産
その秘密は、プリントされた部品が造形プラットフォームから機械的に切り離される時点まで完全に自動化された、独創的でスケーラブルな付加製造チェーンにある。つまり、データ準備から中央粉体供給、AM造形プロセスそのもの、さらに熱処理、品質保証、造形プラットフォームからの部品の分離に至るまで、プロセスのどの段階でも手作業が不要になったのです。このシステムの技術的中核は、金属材料を使用する産業用3Dプリンティング用の4レーザーシステムEOS M 400-4です。ドライバーレスの搬送システムとロボットが、生産ラインの各段階における部品のスムーズな移動を保証します。
生産プロセス全体が、中央の自律的なコントロールセンターから、操作担当者を介さずに自走する。このシステムの基本は、使用されるすべての機械がネットワーク化されていることだ。製造ジョブデータはコントロールセンターに送信され、コントロールセンターはさまざまな製造リクエストに優先順位をつけ、AMシステムに割り当てる。製造プロセス中、製造ステータスは、場所に関係なくモバイル・デバイスで取得することもできる。すべての製造チェーンが完了すると、品質レポートがコントロールセンターに一元的に送信される。デジタル "ツイン "の製造に必要なすべてのデータは、ここでアクセスできるため、とりわけ完全なトレーサビリティが可能になる。
容量の拡張が可能
統合された品質管理を伴う継続的な3Dデータストリングにより、この生産システムは、将来のベンチマークであるインダストリー4.0の最初の例のひとつとなっている。製造工程は完全に拡張可能で、生産ラインを複製するだけで工場の生産能力を拡張できる。これにより、将来的に生産数が増えるにつれて、さらに大幅なコスト削減が期待できる。今日、パイロット施設は、すでに量産品質基準での部品の自動製造が可能になっている。
ダイムラー向けの部品は、すでにPremium AEROTECの新技術ラインで生産されている。例えば、トラック部門では、Premium AEROTECで生産された最初の交換部品がすでに使用されている。これは、トラックのディーゼルエンジン用のブラケットです。

トラック・バス用交換部品
3Dプリンティングプロセスは、交換部品の分野で特に有用です。工具に問題が発生した場合、必要頻度の低い部品は、従来の砂型鋳造や圧力鋳造プロセスよりもコスト効率よく再現できることが多いからです。ダイムラーバスの3Dプリンティング・コンピテンスセンターでは現在、アルミニウム製の3Dプリンティングによるバス交換部品の最初の依頼が検討されている。乗用車分野の分析チームも現在、適切な潜在的用途を検討している。
最小シリーズと先行開発の機会
「アディティブ・マニュファクチャリングは、新車(限定車)の最小シリーズ生産にも適している。3Dプリンティング専用のパーツを体系的に開発することで、生産コストをさらに削減し、品質を最適化することができます。3Dプリンティングはまた、自動車の先行開発においても特に理にかなっている。アディティブ・マニュファクチャリングでは、従来の製造プロセスよりもコスト効率よく、しかも短時間で、必要な数を生産できることが多いのです」。
ダイムラーAGの未来技術責任者、ヤスミン・アイヒラー氏
そしてこれは、電気自動車と同様に、内燃エンジンを搭載した自動車にも当てはまる。3Dプリンティングは、例えば電気自動車のバッテリーの冷却ラインを運ぶ一体型ベースプレートの製造にも非常に適している。
高い製品品質を標準装備
パイロット施設では、高い製品品質が標準となっている。また、航空・宇宙分野で使用される部品用の高強度アルミニウム/マグネシウム/スカンジウム合金(Scalmalloy®としても知られる)の使用も用意されている。
自動車分野では、古典的なアルミニウム合金(AlSi10Mg)が使用されており、その材料特性はパイロット・プロジェクトの過程で継続的に改善されてきた。特に材料強度と仕上げ品質は、協力が始まった2年前と比べて大幅に改善されている。
展望将来性のある生産方法としての3Dプリンティング
これまでのすべての品質検査が有望な結果で合格した今、厳しい業界標準VDA 6.3の要件に従った監査の準備が進められている。これはダイムラーにとって、受託印刷サプライヤーが量産部品を供給するための前提条件のひとつである。AM生産チェーン全体が自動化されることで、将来的には、従来製造の部品と同等の信頼性、機能性、耐久性、経済効率で、大量ロットの連続生産が可能になる。新車のコンポーネントは、設計段階で3Dプリンティングに最適化できるため、コスト面でさらなるメリットが期待できる。また、3Dプリンティングは重量面でもメリットがあり、電気自動車では特に注目されている。交換部品に関して言えば、3Dは倉庫保管コストを削減するという利点をもたらす。つまり、3Dプリンティングを使用した交換部品の分散生産を可能にするために、デジタル製造データを一元的に利用できるようにすることである。
このように、3Dプリンティングは、非常に汎用性が高く、比較的歴史の浅い新たな製造方法として、自動車や航空宇宙分野でさらに確立されつつある。

プロジェクト・パートナー
プレミアム・エアロテック
Premium AEROTECは、エアバス航空機の量産用にチタン合金製の3Dプリント部品を供給する世界初の部品メーカーである。同社は航空分野における世界的な企業である。その中核事業は、金属と炭素繊維複合材料からなる航空機構造の開発と製造である。同社はドイツ国内のアウグスブルク、ブレーメン、ハンブルク、ノルデンハム、ヴァレルに拠点を構えている。Premium AEROTECは、この共同プロジェクトに関わるすべての製造工程を担当した。
______________
EOS
EOSは、金属とポリマーの産業用3Dプリンティング分野で世界をリードする技術サプライヤーです。1989年に設立されたこの独立系企業は、積層造形における包括的ソリューションのパイオニアであり、イノベーターです。EOSシステム、材料、プロセス・パラメーターの製品ポートフォリオにより、顧客は製品の品質と製造プロセスの長期的な経済的持続可能性の面で決定的な競争優位性を得ることができる。この共同プロジェクトの一環として、EOSは3Dプリンティング技術一式と関連ソフトウェア・ソリューション、および生産チェーンを連結・管理するためのコントロール・センターを提供しました。
______________
ダイムラー
ダイムラーはこのプロジェクトに大規模生産の経験を提供した。研究部門と先行開発部門は非常に緊密に連携した。ここでカバーされたのは、サンプル・コンポーネント、計算上の堅牢性、完全な生産工程におけるコンポーネント・データのデジタル化などである。サンプルコンポーネントのテストも自動車メーカーが担当し、3Dプリンティングのための標準化された製造仕様書の作成もダイムラーが担当した。ダイムラーはさらに、連続生産に関するVDA 6.3規格に従った検証と認証の監視も担当した。
ダウンロード
-
NextGenAMプロジェクトの一環として製造されたトラック用ディーゼルエンジンのブラケット。
JPG 2,74 MB -
パイロット生産チェーンの中心は、金属材料による産業用3Dプリント用の4レーザーシステムEOS M 400-4である。
JPG 881,07 kB