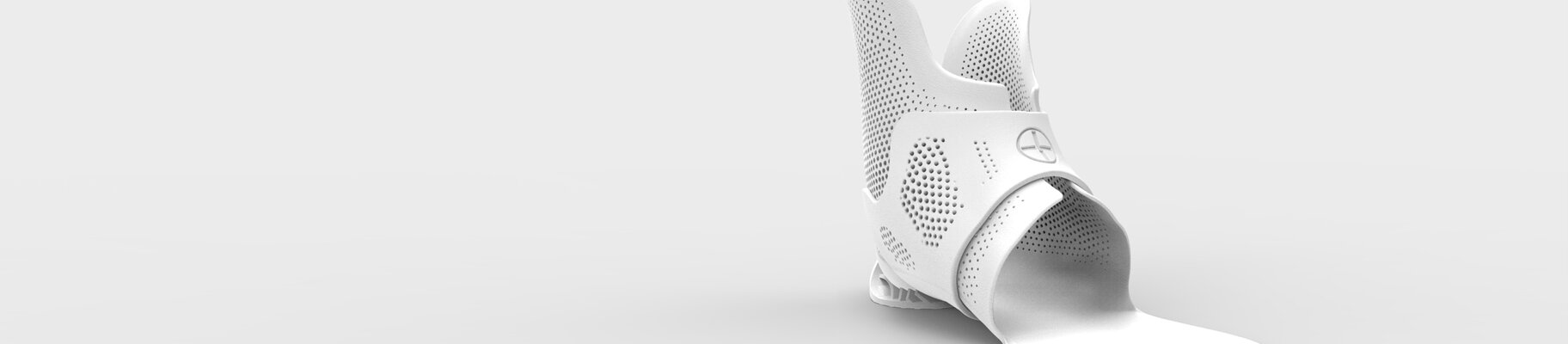
3Dスキャニングと3Dプリンティングによる装具の製造 - 最大限の柔軟性と設計の自由度
オットーボック|サクセスストーリー
複雑な構造とカスタムデザイン
「快適な通気性:リングクロージャーシステムを備えたこの足関節装具の穿孔は、ほぼ全面を覆い、過度の発汗を防ぐ。
支持装具に関しては、整形外科技術者は一般的に、個々の患者のニーズに合わせて形状、機能、材料の厚さを設定しなければならないため、個々の構造に制限されます。複雑な構造が要求される場合、従来の工程では限界があることが多い。さらに、装具は製作に時間がかかるため、すぐに入手できるものでもない。このような問題に対処するため、オットーボック社は工業用3Dプリンティングを採用している。EOSの生産システムとコンサルティング・サービスを利用して、同社はカスタムメイドの装具を生産しています。

「医療機器のトレンドは、カスタマイズされた製品を作ることです。EOSテクノロジーは、患者に特化した製品製造を可能にすると同時に、外科手術の顧客への納品を早めることで、コストをコントロールすることを可能にします。"
ルーカス・エッカーマン|患者ケアおよびiFab(個人製作)部門責任者|オットーボック
チャレンジ
患者のニーズに合わせて最適に調整された、複数の機能を組み合わせた装具の設計、CADエンジニアリング、製造
人はひとりひとり違う。特に整形外科では、その人の可動性を個別にサポートしたり、回復させたりすることが目標となります。治療を完全に成功させるためには、装具は患者の解剖学的構造と治療上のニーズに正確に合うように設計されなければなりません。これまで整形外科技術者は、装具を製作するために、鋳造、成形、モデリング、フライス加工といった従来の製造方法の可能性に導かれてきたからです。
しかし、複雑な構造やさまざまな材料の厚さによって、確立された工程はその能力の限界に達している。1つの製品に複数の機能を組み合わせる必要がある場合、完成した装具を作るために個々の部品を手作業で組み立てなければならず、これは非常に時間のかかるプロセスである。
同時に、脳性麻痺、二分脊椎、麻痺などの神経障害を基礎に持つ患者の移動をサポートするために、装具をできるだけ早く利用できるようにする必要がある。さらに、子どもは成長が早いため、装具を頻繁に交換する必要がある。
オットーボック社は、このような課題を認識し、産業用3Dプリンティングを採用して患者ケアを最適化するという目標を設定しました。「私たちは、手作業による整形外科技術と積層造形の利点を組み合わせています」と、オットーボック社の患者ケアおよびiFab(個別製作)部門の責任者であるルーカス・エッカーマンは言う。
ソリューション
EOS P 396を用いた産業用3Dプリンティングにより、患者用に個別に調整された装具を製作。
オットーボック社は、plus medica OT社の買収により、装具のデジタル生産に参入した。この小さな新興企業は、2015年から3Dプリントによるソリューションを開発している。オットーボック社にとって重要な優先事項は、この技術が提供する可能性を利用して患者ケアを改善し、ネットワーク内のすべての整形外科技術者が利用できるようにすることです。3Dプリンターによる装具の経済的・技術的最適化を何年もかけて行い、特に形態と機能の側面に注目した結果、オットーボック社はマイネクストMAFOを発表しました。このダイナミックな足関節装具は、デジタル製造が可能にした革新的な特性と、熟練した整形外科技術者の経験を組み合わせたものです。患者一人ひとりに最高のサポートを提供するためには、現地の整形外科技術者との緊密な連携が非常に重要です。建設と付加製造の全工程を整形外科技術の要件に合わせて調整することで、初めて最良の結果を実現することが可能になる。
そのため、同社は3Dプリンティング分野の技術リーダーであるEOS社と協力している。同社は必要なシステムや材料を供給するだけでなく、開発・製造プロセスにおいてもユーザーをサポートしている。「例えば、最適な材料を選択する際など、EOSが提供する非常に有能でパートナーベースのコンサルティングから恩恵を受けています」とLukas Eckermann氏は説明する。医療工学の経験を持つアプリケーション・スペシャリストが、オットーボック社のノウハウの蓄積を支援し、技術の可能性を十分に引き出す方法を教えてくれました。そして現在も、設計の最適化や機能的な統合に関して、いつでも支援を受けることができる。
3Dプリントされたマイネクスト装具のベースとなるのは、整形外科の臨床医が作成したボディスキャナーによる患者の足のスキャンです。その後、CADソフトウェアでスキャンモデルを修正し、カスタム製品のデジタル注文プラットフォームであるiFabカスタマーセンターを通じて、希望の製品仕様とともにオットーボック社に送信します。次に、製造システムであるEOS P 396に製造データが送信される。その後、レーザービームを使用して、微細な粉末材料から1層ずつパーツを作り上げていく。これにより、特別な工具を必要とせず、想像しうるあらゆる形状のパーツを作ることが可能になる。使用される素材は、高い剛性と衝撃強度を持つナイロン系ポリマーPA 1101で、大きな負荷がかかっても割れたり裂けたりしない。これにより、患者が怪我をする危険性が低くなります。
結果
積層造形は、オットーボック社が新しいアプローチで最高品質の補助具を製造することを可能にしました。複雑な構造にも問題なく対応できます。また、装具内にさまざまな材料の厚みを組み込むことも可能で、それによって必要な厚みや薄さの壁を作ることができます。さらに、積層造形は異なる構造の統合を可能にし、特定の部分を柔軟にも硬くもします。これは通気性を向上させるパンチングにも適用される。「ルーカス・エッカーマンは、次のように説明する。「従来の製造方法では、そう簡単に実現できなかったような形状、低い肉厚、統合された機能がいくつかあります。装具は、以前よりも患者のニーズに合わせることができるようになりました。この装具は、見た目のカスタマイズも比較的簡単で安価です」。
将来的には、その後の染色や漆塗りによってカラーバリエーションを作ることもできる。ルーカス・エッカーマンにとって、重量と統合機能の最適化、高い通気性、魅力的なデザインは、すべて治療の成功の決定的な要因である:「装具を好んで装着する人はいません。しかし、日常生活でほとんど気づかれず、見た目もよければ、装具の装着時間が大幅に延び、ひいては装具の治療効果も高まります。"一度開発した装具は、いつでも同じ品質で再製作することができます。これは特に小児用装具に関係します。小児用装具は、同じ機能と構造で、異なるサイズに交換する必要があります。産業用3Dプリンターにより、オットーボック社は、生産台数や装具の種類を増やすことで、ソリューションの規模を容易に拡大することができます。
結果一覧
- 機能性:構造、機能、肉厚の設計が自由自在
- 再現性: 特定の装具は、いつでも同じ構造と特性で再製作できる。
- 快適性:軽量性と通気性が着用者の快適性を高める
- 標準化: 手作業による生産品質要因に依存しない、一貫した再現可能な生産品質