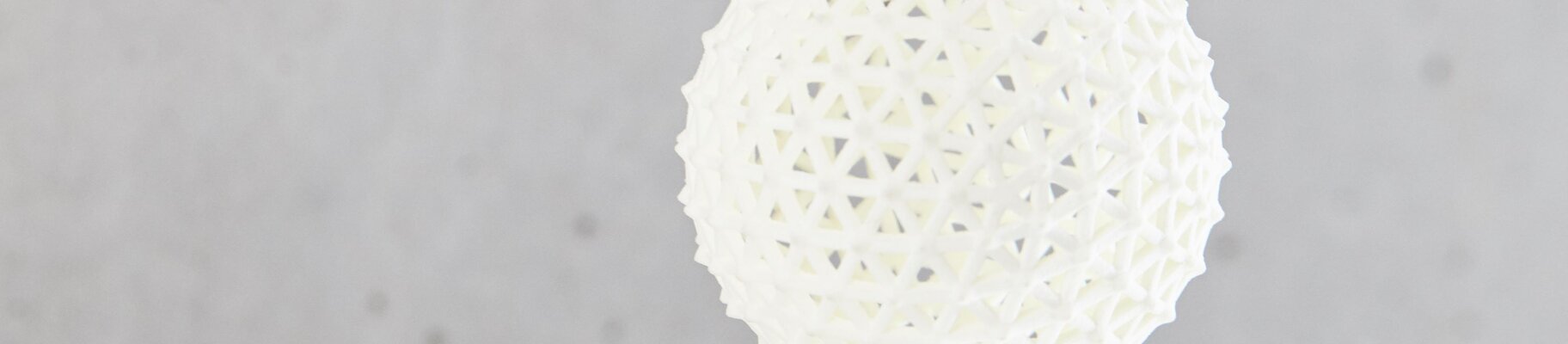
AMの初心者積層造形とその主要技術の入門ガイド
2023年5月8日|閲覧時間:5分
積層造形のエキサイティングな世界と、それを実現する重要な技術について初めて知りましたか?このブログでは、包括的でわかりやすいガイドをまとめました。
積層造形は未来を見据えたものづくり
厳密な意味では新しい技術ではないが、アディティブ・マニュファクチャリング(AM)(3Dプリンティングと呼ばれることもある)は近年、大きな注目を集めている。そして、それには多くのエキサイティングな理由がある:
-
最先端のポリマーブレンドや汎用性の高いアルミニウム合金を成形するためにAMシステムや材料を使用している組織のいずれであっても、かつては不可能であったか、(少なくとも)達成するのが極めて困難であった幾何学的パラメータに従って部品を作成することができるようになったという事実に変わりはない。
-
アディティブ・マニュファクチャリングで製造された部品は、従来製造された部品よりも「シンプル」に見えるかもしれない。しかし、多くの場合、AMで製造された部品は、従来の部品の性能に匹敵するか、それを上回ることができます。
-
アディティブ・マニュファクチャリングは、数多くの用途でその威力を発揮している。その範囲は、カジュアルで楽しいもの(ランニングシューズやホッケー用ヘルメット)から、ワイルドでエキサイティングなもの(ロケットエンジン)から、本当に重要なもの(医療用インプラントや手術器具)まで多岐にわたる。
-
アディティブ・マニュファクチャリングを採用した企業は、市場投入までの期間と全体的な経費の削減とともに、生産品質と効率が長期にわたって目に見えて向上している。
EOSは、3Dプリンティングシステム、ソフトウェアから教育、コンサルティングサービスまで、あらゆるものを開発し、技術の初期から積層造形革命の一翼を担ってきました。しかし、あなたが本当にアディティブ・マニュファクチャリングの初心者であるならば、EOSの善意はまだ伝わらないかもしれません - この驚くべき技術の背景、プロセス、アプリケーション、成功についてもっと知りたいでしょう。
そしてそれこそが、私たちが皆さんをお連れする旅の目的なのだ。
積層造形の歴史
ある情報源では、アメリカのエンジニアで発明家のビル・マスターズが出願した特許(具体的には1984年7月2日付の米国特許第4665492A号)が最初の3Dプリンティング特許と呼ばれている。また、同じ年に米国で出願されたチャールズ・ハルの特許にこの栄誉を授与する人もいる。そして、どちらもこの技術の歴史にとって重要なものである。
しかし、児玉英雄が日本特許庁に提出した特許出願(特願S56-144478)は、マスターズとハルより3年近くも前に出願されていた:マスターズが最終的に米国特許商標庁(USPTO)に送った出願と同様、この出願には、熱(レーザーまたは紫外線(UV))を使って柔らかいプラスチックを硬化させ、3D形状を作成する自動化されたプロセスが記載されている。
児玉は自分のアイデアを有名な業界誌に掲載したにもかかわらず資金を集めることができなかったため、特許申請を断念した。マスターズは特許を経て助成金を受け、約10年間この分野で働いたが、これもほとんど注目されなかった。
知られざる分水嶺の年
1984年には、いくつかの重要なAMプロセスが発明されましたが、これらの初期の技術革新が大規模に実現するまでには時間がかかりました。マスターズの設計は(児玉の設計と同様)、将来のAMシステムに不可欠なコンピューター数値制御(CNC)とコンピューター支援設計(CAD)プログラミングの初期の例を含んでいた。
今年はまた、商業利用が可能な最初の積層造形プロセスのひとつであるステレオリソグラフィ(SLA)に関して、2件の特許出願があった。
フランスの発明家アラン・ル・メホーテ、オリヴィエ・ド・ウィッテ、ジャン・クロード・アンドレの3人による最初の発明は、出願後すぐにスポンサーから放棄された。2つ目はチャールズ・ハルによるもので、SLA-1 3Dプリンターの生産を促した。SLA-1は多くの人にとって法外に高価であり、ハルも他の初期のAM提唱者と同様に、従来のメーカーにその可能性を納得させるのに苦労した。しかし、ハルはSLA-1の設計ファイルのためにSTLを発明し、そのフォーマットは今日でも一般的である。
リファインとアップスケール
EOSを含むエンジニアたちは1990年代、初期の積層造形プロセスであるSLAや溶融積層造形(FDM)を着実に改良し、新しいプロセスを開発してきた。そのほとんどは(すべてではないが)、ポリマーを3D部品に成形することに重点を置いており、材料やバインダーの噴射、シート積層、レーザー粉末床溶融(LPBF)、選択的レーザー焼結(SLS)などがあった。SLSやLPBFのように、高度な金属加工を可能にするものもあったが、それは従来の(減法的)製造のためのものだった。しかし、マイクロキャスティングや溶射を含む材料堆積法の開発は、金属の付加的使用への道を開いた。
CADソフトウェアの進歩や粉末ポリマーや金属の台頭と相まって、産業用3Dプリンティングシステムの改良が進み、2000年代を通じてラピッドプロトタイピングでよく知られるようになった。2010年代には、積層造形は、はるかに高いレベルでの部品組み立てを促進するのに十分なほどスケールアップし、場合によっては、正確に「大量生産」と見なされるほどにまでなりました。材料の互換性(主に金属側)、導入に必要な初期コストと労力、(縮小しつつあるとはいえ)スキル・ギャップ、伝統的な製造業者からの懐疑的な見方など、AMに影響を及ぼすいくつかの制約がまだあるにせよ、この技術の存在と重要性は拡大し続けている。
主なAM技術
生産設備に積層造形技術を導入する本格的な計画に向けた次のステップは、主要な積層造形技術の基礎について学ぶことである。
これは、すべての積層造形法のリストではありませんし、以下に詳述する技術のすべてがEOSシステムで使用されているわけではありません。しかし、AMについて可能な限り情報に基づいた決断を下すには、当社の製品カタログにとどまらず、このトピックを理解する必要があります。
光重合
現在も使用されているSLAプロセスではないが、バット光重合(または単に重合)は間違いなく最も一般的である。この方法の名前は、製造の原動力となる材料の供給源、すなわち液体光重合樹脂の桶に由来する。ビルド・プラットフォーム」が繰り返し桶の中に降ろされ(そして桶から引き上げられ)、出てくるたびに、UV光源またはレーザー光源がプラットフォーム上の樹脂を硬化させ、システムに接続されたCADソフトウェアの設計パラメータに従って、コンポーネントを形成する層を形成する。組み立てが完了すると、システムは余分な樹脂を排出した製品を槽から取り出す。
槽内重合法で付加製造された部品は、他のAM法で製造された部品よりも後処理が必要になる場合がある:コンポーネントを効果的に硬化させるには、さらにUV照射やレーザー照射が必要になることがある。また、造形中、硬化樹脂が設計者の意図した形状を形成するように、プラットフォーム上に支持構造物を設置しなければならないことがある。全体として、バット重合は迅速で正確なプロセスであるが、完成した部品は必ずしも劣化や腐食に強くないため、市場に出せる部品を製造するよりもプロトタイピングに適しているかもしれない。
素材とバインダーの噴射
マテリアル・ジェッティングは、3DプリンティングがAMの全体的な同義語として使われることがあるにせよ、おそらく他のほとんどの積層造形法よりも「印刷」に近い性質を持つ。造形プラットフォームの上にあるノズルから、液化した材料(通常はポリマーまたはワックス、場合によっては金属)が造形プラットフォーム上に繰り返し滴下される。UV光が液滴を硬化させ、設計パラメータに沿った層が形成され、計画されたオブジェクトの形状になる。マテリアル・ジェットは一部の材料にしか適合しないため、その有用性は限られている。この方法の最大の利点は廃棄物が少ないことで、ラピッド・プロトタイピングにも役立つ。
バインダージェッティングは、粉末と液体を組み合わせて交互に堆積させ、液体(通常はポリカーボネートまたはポリアミド)は接着剤として機能する。この方法の主な利点は、粉末状の金属合金とポリマーやセラミックを一緒に使って部品を作ることができることですが、液体層が冷えて適切な結合を形成するのに必要な後処理に時間がかかるため、この利点は多少相殺されます。
材料押出
これは一般的に溶融積層造形法(FDM)を指し、工業的に成功を収めた最初の積層造形法のひとつである。また、デスクサイズの3Dプリンターの消費者ユーザーには最もよく知られている手法でもある。ポリマーまたはプラスチックをプリンターに引き込み、加熱し、最終的にノズルから層状に堆積させる。
FDMによる材料の押し出しは、ポリマーまたはプラスチックでしか印刷できない。FDM産業用プリンターは、頑丈な部品の基礎となるABSプラスチックに対応しているが、他の積層造形プロセスと比較すると、時間がかかり、精度もそこそこでしかない。これが、FDMプリンターを製造する企業が、完全ではないにせよ、消費者市場に大きく舵を切った主な理由である。
シートラミネート
シート・ラミネーションは、シート・メタルや紙専用の付加製造方法であり、用途は限られているが、高速で低コストのプロトタイプ製造には有用である。
このプロセスの金属バージョンは超音波積層造形(UAM)と呼ばれ、金属シート(通常はアルミニウム、銅、ステンレス鋼、チタン)を超音波溶接する。対照的に、積層造形(LOM)は紙シートを接着剤で重ね合わせる。どちらも部品モデルの作成にしか適していない。とはいえ、複数の金属を使うことができるUAMの能力は、設計者やエンジニアが、たとえば銅でできた付加製造金属部品が、特定の産業用途で他の金属とどのように互換性があるのかをシミュレートするのに役立つかもしれません。
直接エネルギー蒸着
その名が示すように、指向性エネルギー蒸着(DED)は通常、非常に柔軟な自動アームの上に取り付けられたノズルを使用して、熱源が物質に集中するとまったく同時に、ビルドプラットフォームの上に材料を層状に蒸着させる。DEDには多くのバリエーションがあり、ポリマー、セラミック、金属材料を使用することができますが、最も一般的なサブカテゴリーである電子ビーム溶解(EBM)は金属専用です。
部品生産には非現実的だが、この方法はノズルの柔軟性により、部品補修のためのアディティブ技術として有用である。しかし、DEDが可能な高速修復は精度を低下させるため、精度を優先するのであれば、エンジニアは速度を犠牲にしなければならない。
パウダーベッド融合
最も一般的な積層造形技術は、SLS、選択的熱焼結(SHS)、選択的レーザー溶融(SLS)、EBMなど、粉末床溶融法の傘下にある。これらの手法に共通する要素は、粉末状のポリマーや金属に依存することである:粉末は、造形プラットフォーム(ベッド)の下または隣にある容器から、ローラーまたはブレードで層状に取り出され、その後加熱されて固化する。
粉末床溶融法の主な違いは以下の通り:
-
SLSは、ポリマーやプラスチックを融合(焼結)させて完成部品にする。
-
直接金属レーザー凝固法(DMLS)は、粉末金属に使用されるSLSのバリエーションです。
-
SHSはサーマルプリントヘッドを使用して、パウダーベッド内の層を一緒に焼結する。
-
EBMは真空条件下でのみ金属粉末を使用し、電子ビームが粉末層の層を融合させる。
粉末床溶融法は他の積層造形法よりもやや遅く、かなりの電力を必要とする。しかし、ほとんどが産業用途に限られているため、これらの問題は必ずしも問題ではない。また、この技術のレーザーベースのバリエーションは、モデルやプロトタイプとは対照的に、機能的で市場に出せるパーツを確実に製造する能力も間違いなく高い。
EOSのAM技術への貢献
EOSの産業用3Dプリンティングシステムは、ポリマーパウダーと金属パウダーにそれぞれSLSとDMLSのバリエーションを使用しています。実際、EOSはSLSを産業用途に普及させただけでなく、金属3Dプリンティング用のDMLSを約30年前に発明しました。金属を使った積層造形が可能だと考える人がほとんどいなかった頃、当社のエンジニアと専門家は、それを実現するためのツールと方法を改良していました。
全面的な革新
積層造形業界におけるEOSの評判は、当社が改良した粉末床溶融法、当社が開発した3Dプリンティングシステム、社内で作成したポリマーおよび金属積層造形材料だけではありません。当社は、積層造形に総合的なアプローチを取り、受賞歴のあるAdditive Mindsチームによるプロジェクト・コンサルティングや、積層造形初心者がデザイナーになり、エンジニアのスキルを専門技術に磨きをかけるための3Dプリンティング・コースなど、当社のハードウェアやソフトウェアとともに、積層造形をサポートする信頼できるサービスを提供しています。
Additive Mindsの専門家までお問い合わせください。