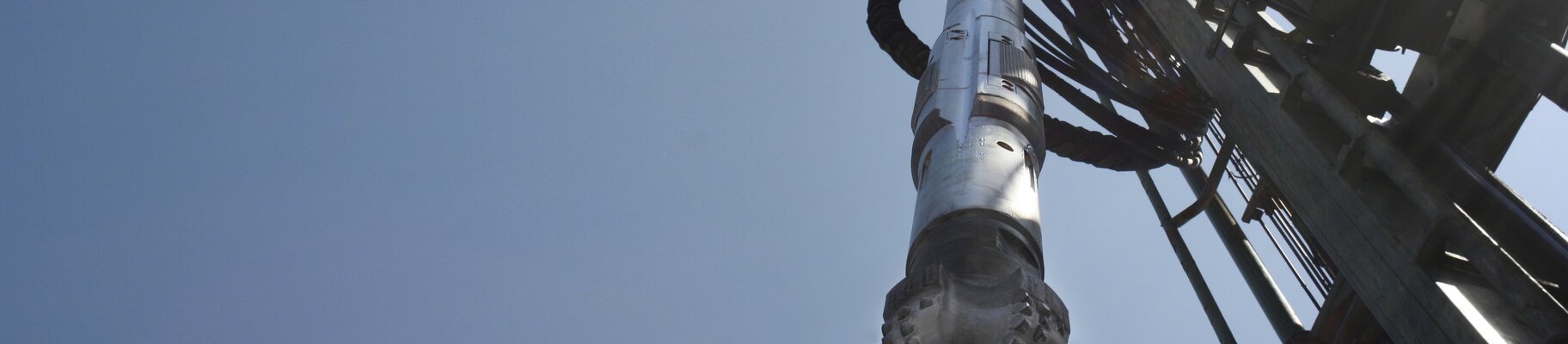
Oilfield Drilling Equipment Manufacturer
APS Technology | Success Story
Advantages of the 3D Printed Oilfield Drilling Equipment
- Shorter lead times and times to market
- Optimized design increases drilling accuracy, reduces post-processing and production costs
- Drilling assembly with part count reduced from four separate components to just one
- Reduction of components by 75 %
"Traditional manufacturing methods have got us this far, but the improved efficiencies of parts created with DMLS are game changers. It creates a domino effect, where longer product life spans lead to less disruption for equipment maintenance, greater drilling time, and lower costs. Ultimately, this makes for a happier customer and additional sales orders."
Paul Seaton | Vice President of Marketing | APS Technology Inc.
"We might give the shop a DMLS part that once took 18 hours to produce by traditional means from bar stock. That part would have taken 22-26 hours to print, but it might have features that could not have been manufactured in a traditional way such as organic holes. Now, finishing that part would only require 3-4 hours to machine sealing surfaces and tighten tolerance features."
Chris Funke | Senior Mechnical Engineer | APS Technology

Additive Manufacturing by EOS – for a New Drilling Experience
APS offers a variety of intelligent tools, including steerable drill motors, vibration dampers, modelling and analysis tools, and logging sensors, in addition to its MWD systems. Aside from the obvious difficulties involved in when cutting rock hundreds of feet under the earth, the pressurized fluid used to cool the drill head and flush away cuttings is highly abrasive and rushes past very fast.
EOS had the perfect solution in store for APS: additive manufacturing based on durable metal. Using this technology, the company was able to build long-lasting parts in a short space of time. The solution is known by the name of: EOSINT M 280. DMLS enables designers to create complex geometries that could not previously be manufactured, and challenges such as these have now become far more manageable.
By using EOS technology, APS has reduced the part count in a drilling assembly from four separate components to just one. Aside from the advantages APS has seen in part-count reduction and novel component shapes, designers are finding that product development cycles are substantially shorter. DMLS is also creating cost savings in the company’s extensive machine shop, where jigs and fixtures that once took days or even weeks to machine can now be printed, unattended, overnight.
EOS Success Stories
Explore three decades of pioneering 3D printing excellence with EOS