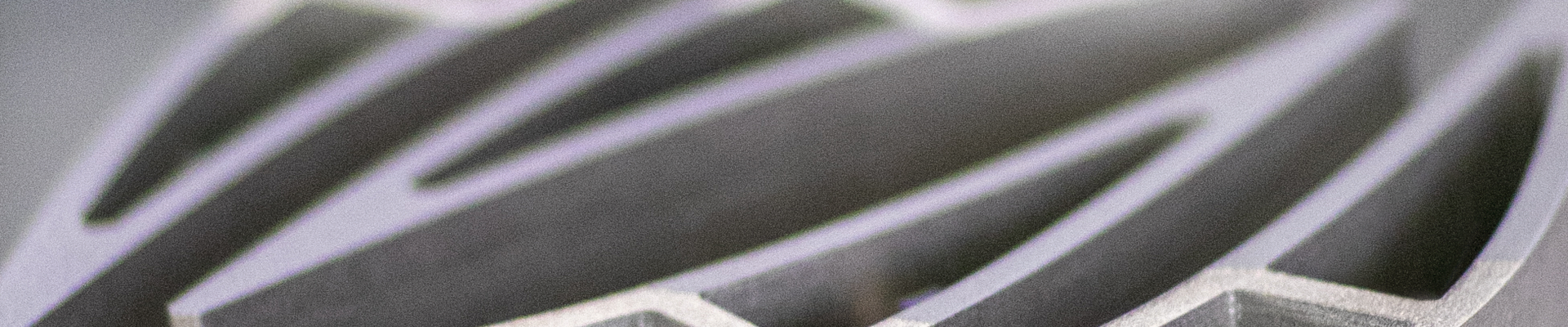
EOS NickelAlloy IN939
Material Data Sheet
EOS NickelAlloy IN939
Excellent High Temperature Performance with Corrosion Resistance
EOS NickelAlloy IN939 is a nickel-chromium alloy which provides an outstanding balance of high temperature strength, corrosion and oxidation resistance, fatigue performance and creep strength at temperatures up to 850 °C (1560 °F). Parts built from EOS NickelAlloy IN939 can be hardened after manufacture by application of precipitation-hardening heat treatments
- Excellent mechanical properties
- Excellent corrosion and oxidation resistance
- High tensile, fatigue, creep and rupture strength at temperatures up to 850 °C (1 560 °F)
- Maintains good ductility in age-hardened condition
- Crack-free in as-built condition and resistant to strain-age cracking
- Industrial gas turbines (vanes, blades, heat-shields)
- Microturbines
- Turbochargers
- Instrumentation parts
- Power industry parts
- Process industry parts
The EOS Quality Triangle
EOS incorporates these TRLs into the following two categories:
- Premium products (TRL 7-9): offer highly validated data, proven capability and reproducible part properties.
- Core products (TRL 3 and 5): enable early customer access to newest technology still under development and are therefore less mature with less data.
All of the data stated in this material data sheet is produced according to EOS Quality Management System and international standards
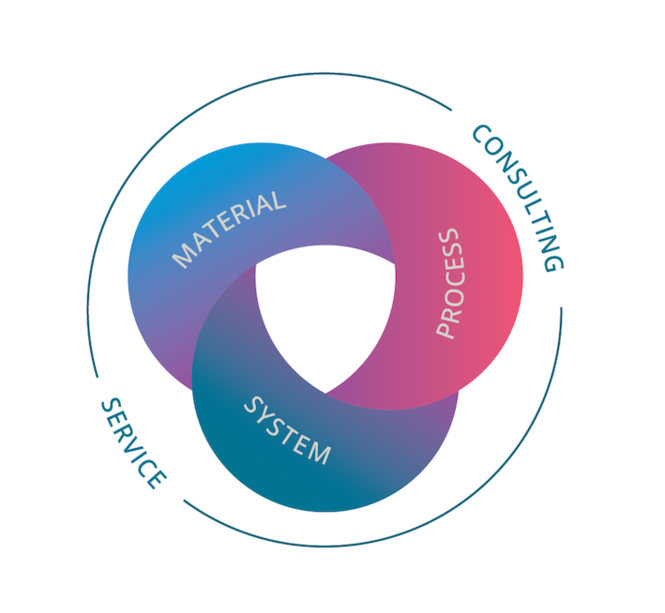
POWDER PROPERTIES
EOS NickelAlloy IN939 has the following chemical composition.
Powder Particle Size
GENERIC PARTICLE SIZE DISTRIBUTION | 20 - 55 μm |
---|
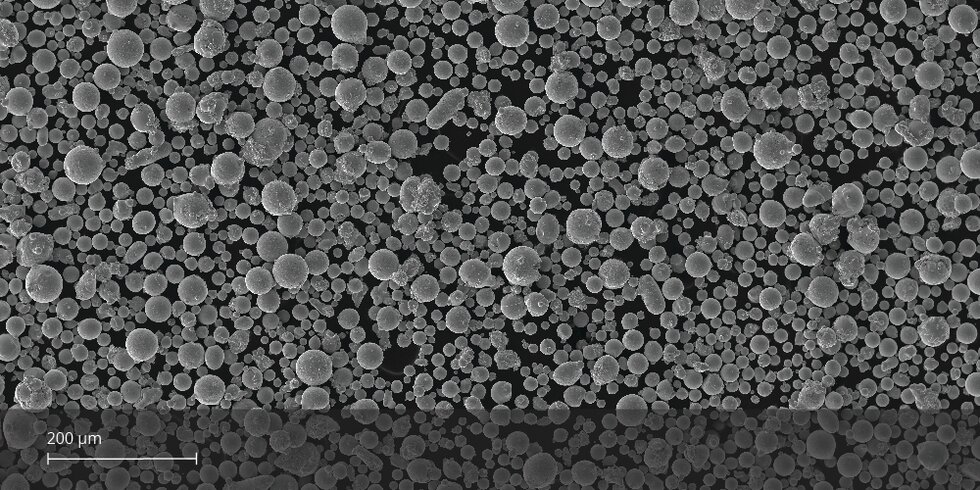
SEM micrograph of EOS NickelAlloy IN939 powder
HEAT TREATMENT
The as-built microstructure of additively-manufactured IN939 consists of gamma phase (γ) and primary carbides. Heat treatment is required for the material to reach the desired microstructure and part properties through precipitation of the gamma prime (γ‘) strengthening phase. EOS has developed a short, AM-optimized 3-step heat treatment (14 hours at temperature), which results in similar or better properties than the commonly used 4-step heat treatment (50 hours at temperature). The gamma prime (γ‘) volume fraction after heat-treatment is in the range of 30 to 40 %.
Solution treatment:
Step 1: The purpose of this treatment is to homogenize the gamma matrix: Hold at 1190 °C for 4 hours followed by fast air / argon cooling.
Aging treatment: The purpose of aging steps is the precipitation and growth of gamma prime (γ‘) and carbides.
Step 2: Hold at 1000 °C for 6 hours, followed by fast air / argon cooling.
Step 3: Hold at 800 °C for 4 hours, followed by cooling in still air / argon.
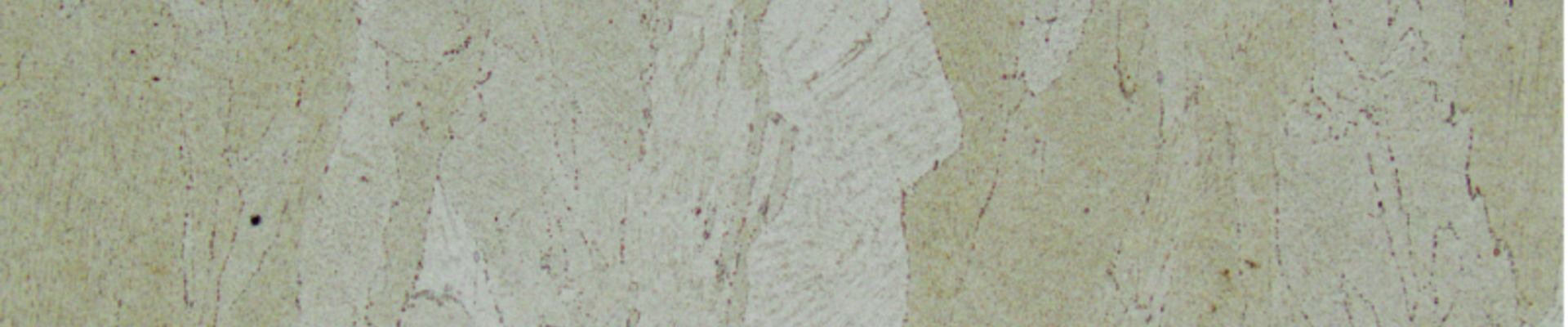
EOS NickelAlloy IN939 for EOS M 400-4 I 40 µm
EOS M 400-4 - 40 µm - TRL 5
Process Information Metal
This process parameter includes two variations of the exposure set: the first one provides better productivity and overhang buildability, while the second one is designed for optimized internal feature and cooling channel accuracy.
System Setup | EOS M 400-4 |
---|---|
EOS Material set | IN939_040_CoreM404 |
Software Requirements |
EOSPRINT 2.8 or newer EOSYSTEM 2.12 or newer |
Recoater Blade | HSS (High Speed Steel) |
Inert gas | Argon |
Sieve | 63 µm |
Additional Information | |
---|---|
Layer Thickness | 40 µm |
Volume Rate | up to 4 x 3.6 mm³/s |
Wall Thickness | Typical 0.3 - 0.4 mm mm |
Chemical and Physical Properties of Parts
Chemical composition of built parts is compliant to EOS NickelAlloy IN939 powder chemical composition.
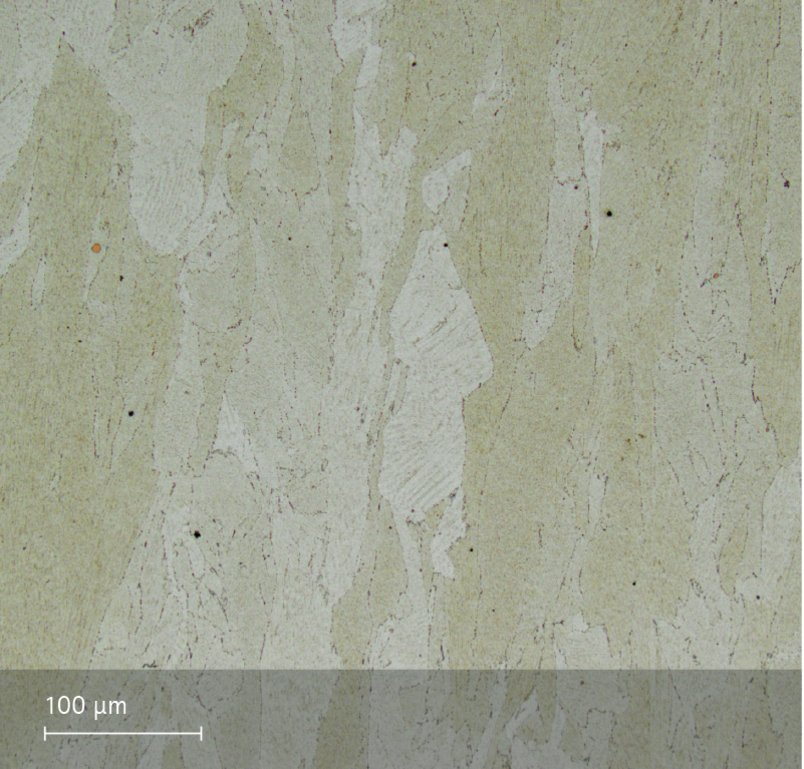
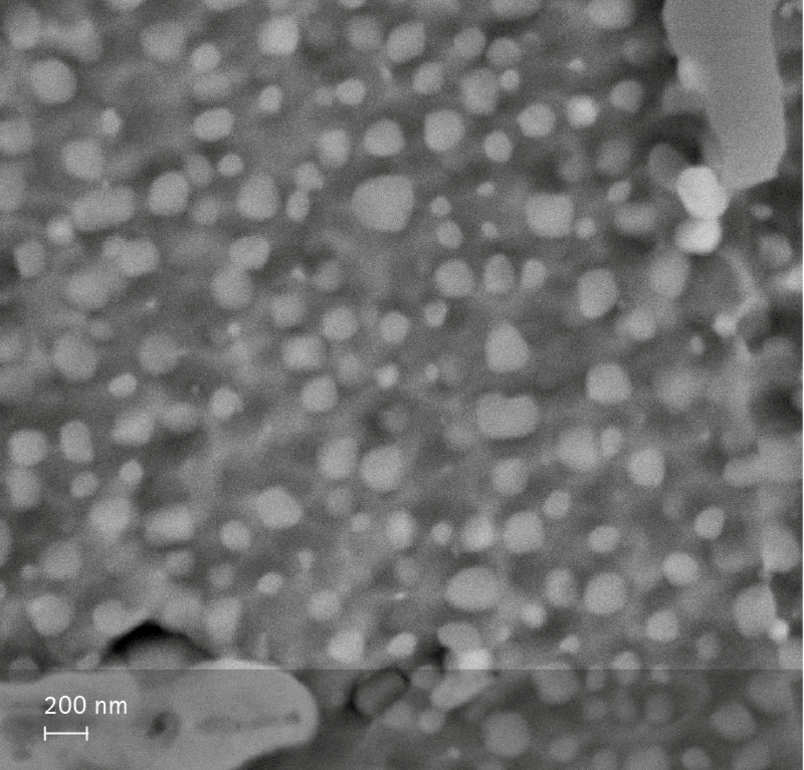
Microstructure of the Produced Parts
Defects | Thickness | Result | Number of Samples |
---|---|---|---|
Average Defect Percentage | - | 0.01 % | - |
Density EN ISO 3369 | Thickness | Result | Number of Samples |
---|---|---|---|
Average Density | - | > 8.15 g/cm³ | - |
Mechanical Properties Heat Treated
EN ISO 6892-1 Room Temperature | Yield Strength [MPa] | Tensile Strength [MPa] | Elongation at Break [%] | Reduction of Area Z [%] | Number of Samples |
---|---|---|---|---|---|
Vertical | 1080 | 1460 | 11 | - | - |
Horizontal | 1160 | 1560 | 9.5 | - | - |
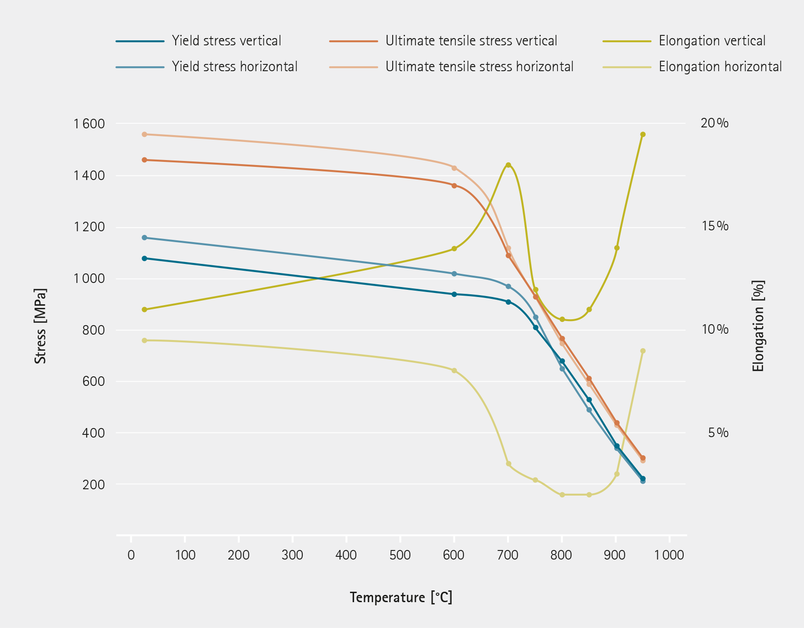
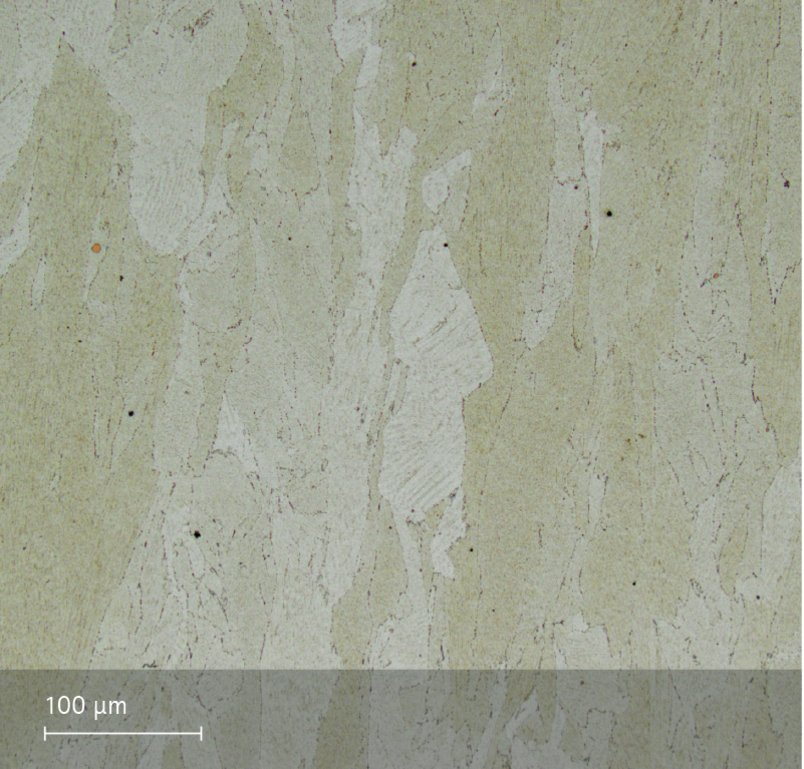
Mechanical Properties As Manufactured
EN ISO 6892-1 Room Temperature | Yield Strength [MPa] | Tensile Strength [MPa] | Elongation at Break [%] | Reduction of Area Z [%] | Number of Samples |
---|---|---|---|---|---|
Vertical | 740 | 1090 | 28 | - | - |
Horizontal | 880 | 1160 | 24 | - | - |
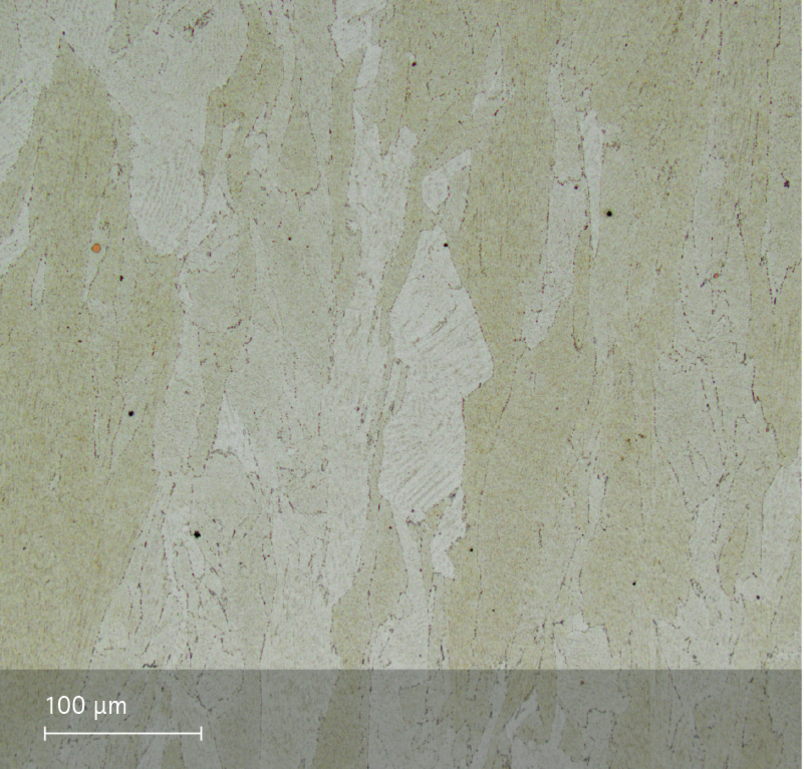
Mechanical Properties
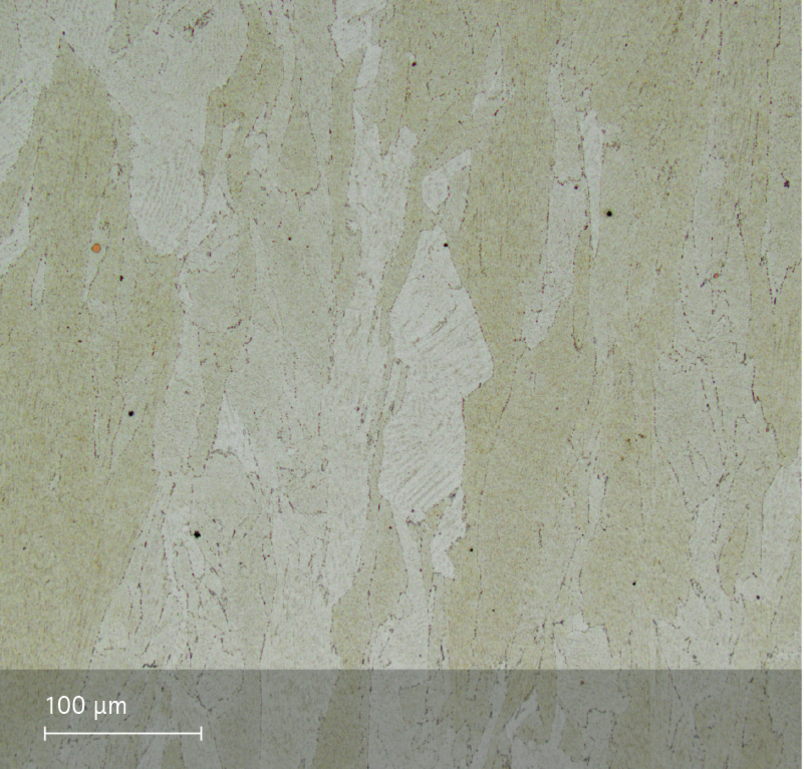
Impact Toughness
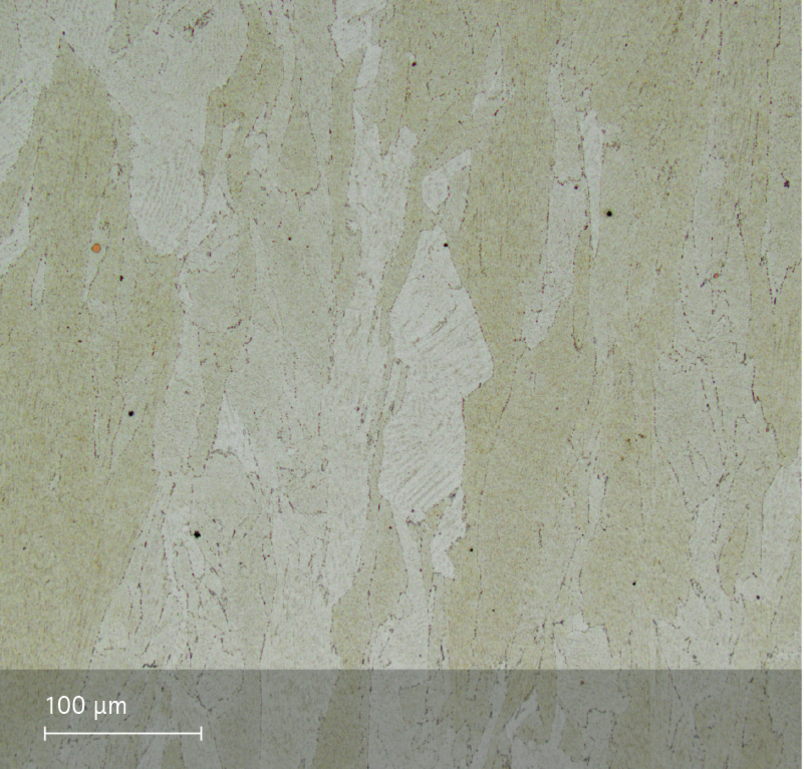
Fatigue
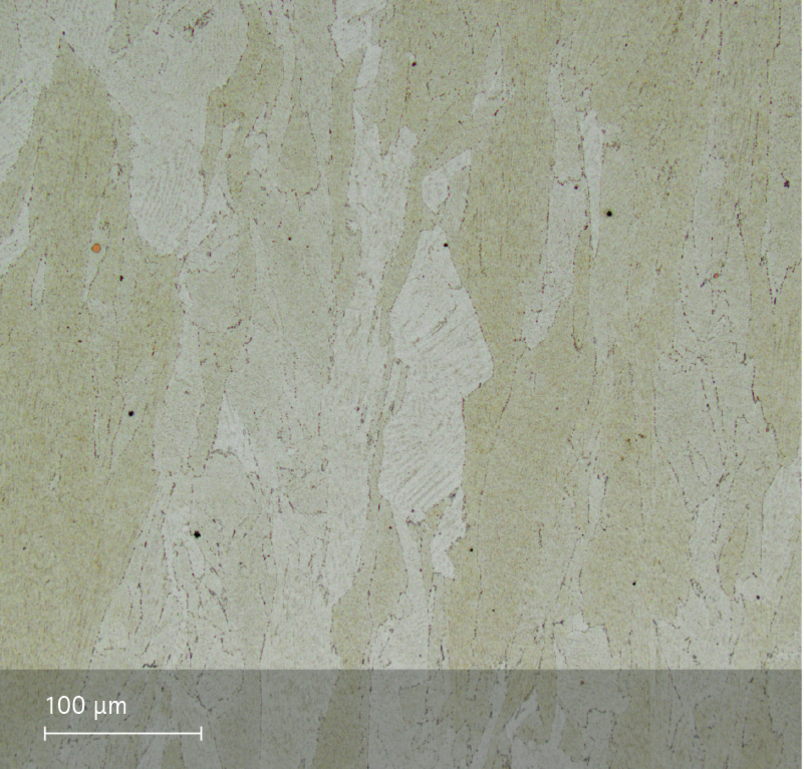
Surface Roughness
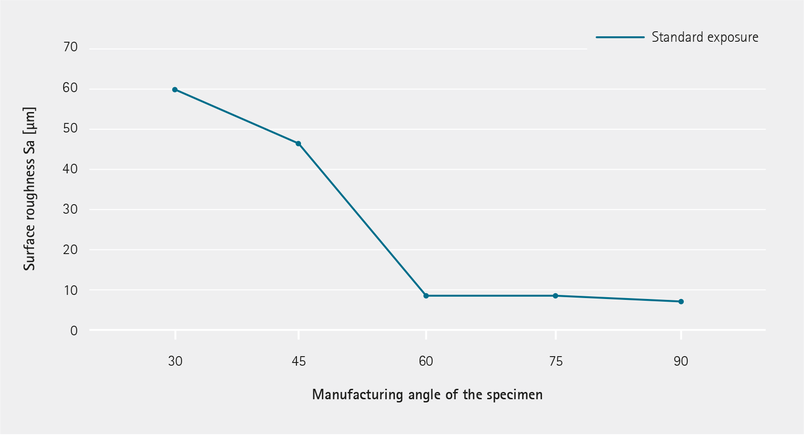
Creep Performance
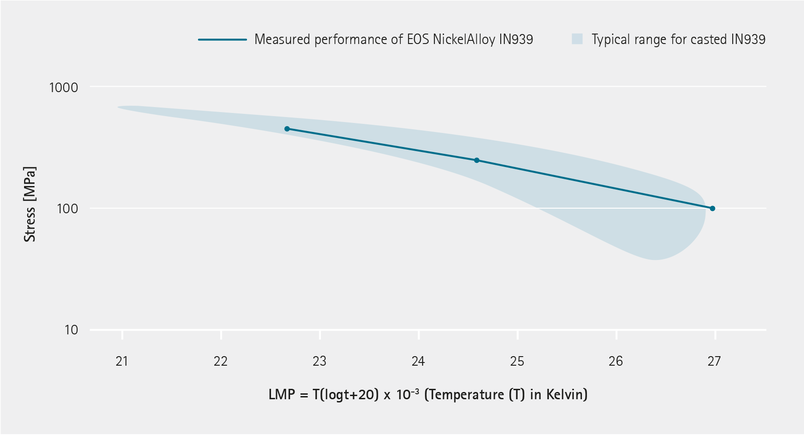
The stress-rupture performance of EOS NickelAlloy IN939 was tested on vertically oriented samples, in heat-treated condition. No HIP was applied. The data presents the Larson-Miller Parameter values achieved at stress levels of 100 MPa, 250 MPa and 450 MPa. Standard: ASTM E139
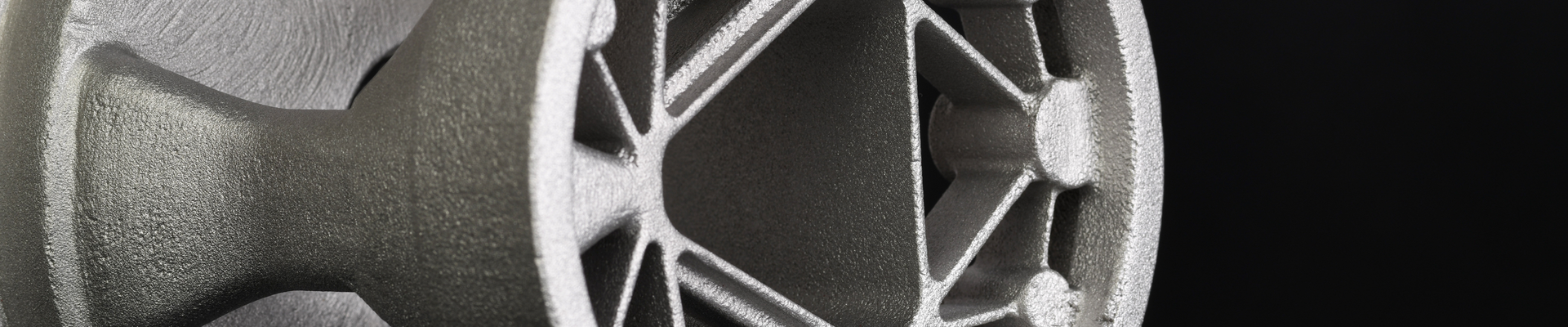
EOS NickelAlloy IN939 for EOS M 290 I 40 µm
EOS M 290 - 40 µm - TRL 7
Process Information Metal
This is the process description
System Setup | EOS M 290 |
---|---|
EOS Material set | IN939_040_HiPerM291 |
Required Software Plan | EOS BUILD |
Software Requirements |
EOSPRINT 2.6 or newer EOSYSTEM 2.10 or newer |
Recoater Blade | HSS (High Speed Steel), Ceramic, Carbon Fiber Brush, Nitrile Butadiene Rubber (NBR) |
Build Platform Temperature | 80 °C |
Nozzle | EOS Grid Nozzle |
Inert gas | Argon, Nitrogen |
Sieve | 63 µm |
Additional Information | |
---|---|
Layer Thickness | 40 µm |
Volume Rate | 3.6 mm³/s |
Exposure Strategy | Swimlanes |
Wall Thickness | Typical 0.3 - 0.4 mm mm |
Typical Dimensional Change after HT [%] | +0.2% % |
Chemical and Physical Properties of Parts
Chemical composition of built parts is compliant to EOS NickelAlloy IN939 powder chemical composition.
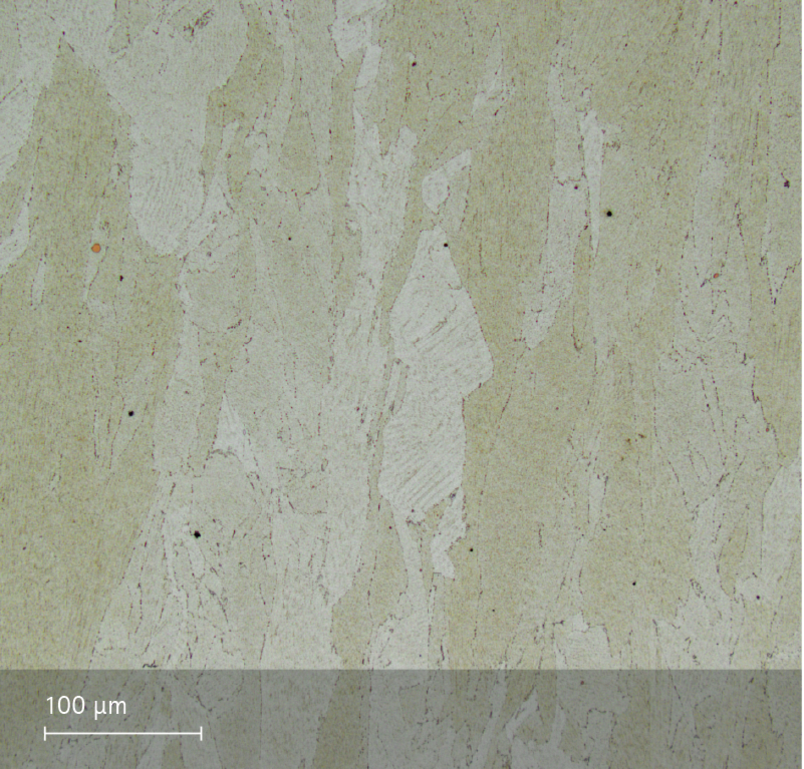
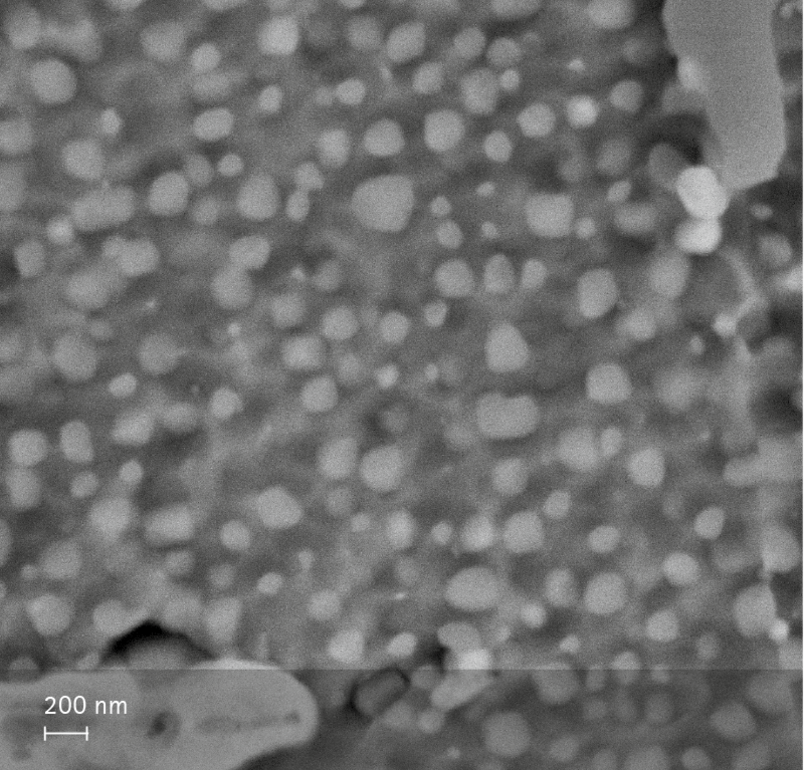
Footnotes Part properties
Microstructure of the Produced Parts
Defects | Thickness | Result | Number of Samples |
---|---|---|---|
Average Defect Percentage | - | 0.01 % | 10 |
Average Defect Percentage | 20 µm | 0.3 % | 10 |
Density EN ISO 3369 | Thickness | Result | Number of Samples |
---|---|---|---|
Average Density | 40 µm | > 8.15 g/cm³ | - |
Density AMS 2774 | Thickness | Result | Number of Samples |
---|---|---|---|
Average Density | 30 µm | 8.10 g/cm³ | 15 |
Mechanical Properties Heat Treated
EN ISO 6892-1 Room Temperature | Yield Strength [MPa] | Tensile Strength [MPa] | Elongation at Break [%] | Reduction of Area Z [%] | Number of Samples |
---|---|---|---|---|---|
Vertical | 1100 | 1500 | 13 | - | - |
Horizontal | 1130 | 1520 | 11 | - | - |
HT description mech properties 1
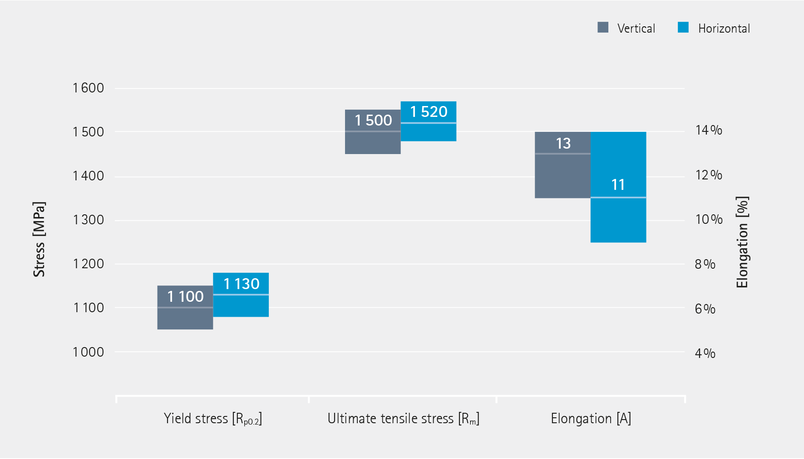
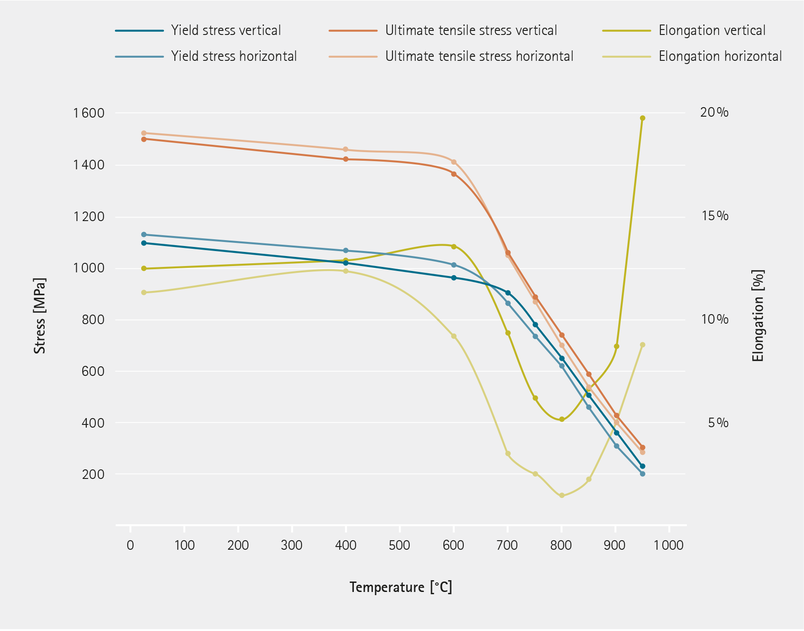
Footnotes Mech properties
Mechanical Properties As Manufactured
EN ISO 6892-1 Room Temperature | Yield Strength [MPa] | Tensile Strength [MPa] | Elongation at Break [%] | Reduction of Area Z [%] | Number of Samples |
---|---|---|---|---|---|
Vertical | 740 | 1090 | 28 | - | - |
Horizontal | 880 | 1160 | 24 | - | - |
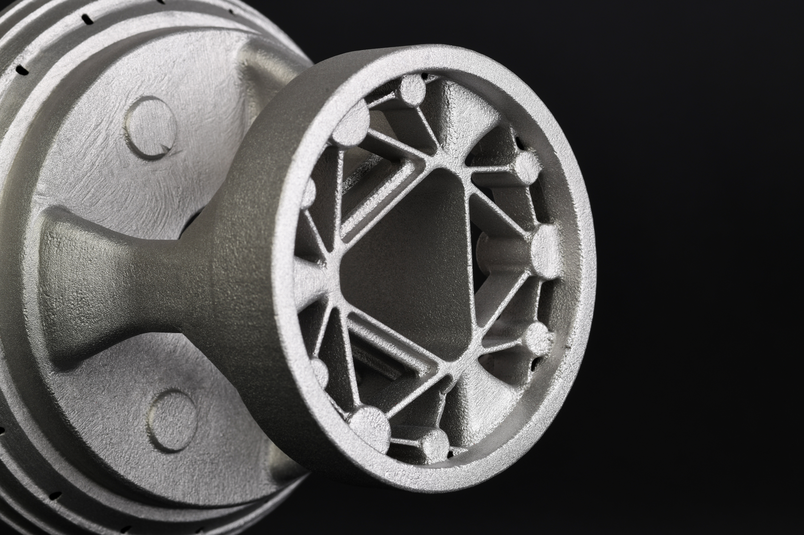
Hardness
EN ISO 6508 Heat Treated | |
---|---|
Value | 48 |
Unit | HRC |
Number of samples | 10 |
EN ISO 6508 As Manufactured | |
---|---|
Value | 10 |
Unit | HRC |
Number of samples | 10 |
EN ISO 6508 As Manufactured | |
---|---|
Value | 33 |
Unit | HRC |
Number of samples | 10 |
Impact Toughness
EN ISO 148-1, Charpy-V As Manufactured | |
---|---|
Typical Impact Toughness | 110 |
Layer Thickness | 20 µm |
Specific Exposure Set | Default |
HT description Impact toughness
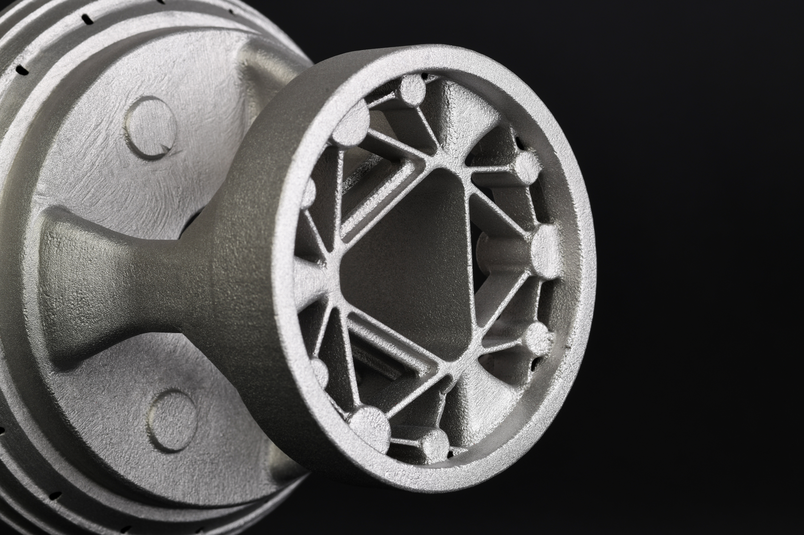
Footnotes Impact toughness
EN ISO 148-1, Charpy-V As Manufactured | |
---|---|
Typical Impact Toughness | 120 |
Layer Thickness | 30 µm |
Specific Exposure Set | Default |
HT impact toughness 2
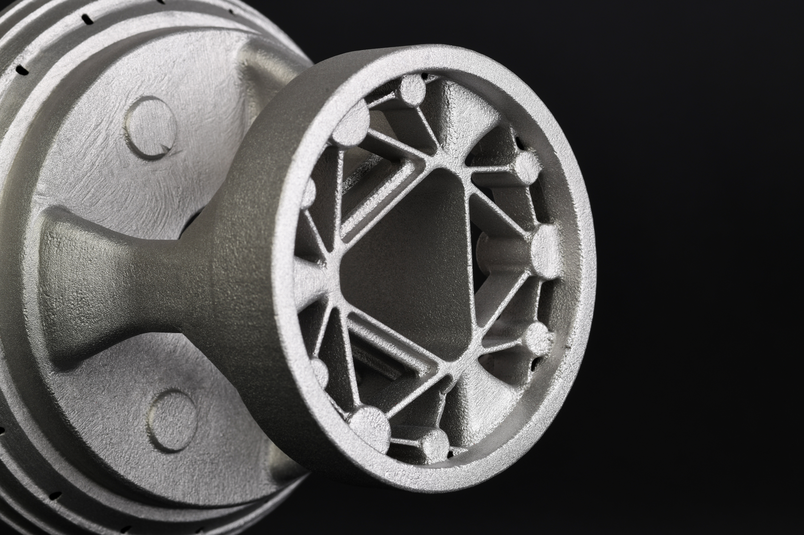
Footnotes impact toughness 2
AMS 2774 As Manufactured | Stress [Mpa] | Temperature [°C] | Time to Rupture [hrs] | Elongation [%] | RA [%] |
---|---|---|---|---|---|
Vertical | 10 | 25 | 1 | 15 | 16 |
Horizontal | 11 | 16 | 2 | 18 | 19 |
stress rupture performance description
Fatigue
HT Fatigue - NOT SHOWING UP!!
Low cycle fatigue performance of horizontally and vertically oriented samples at temperatures of 25 °C, 650 °C, 750 °C and 850 °C. The data represents cycles to failure for different strain amplitudes. No HIP was applied. Method, standard, cycles: axial, strain controlled testing according to ASTM E606
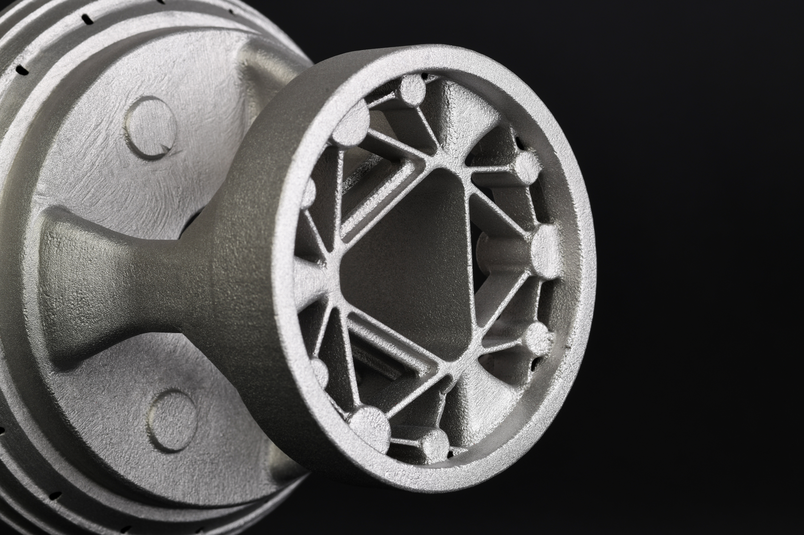
Footnotes for Fatigue 1
As Manufactured | |
---|---|
Fatigue Strength [MPa] | 550 |
HT description fatigue 2 - not showing up!
method fatigue 2
Footnotes fatigue 2
Thermal Conductivity
AMS 2774 | Orientation | [W/m*K] |
---|---|---|
As Manufactured | Vertical | 10 |
As Manufactured | Horizontal | 20 |
HT Description thermal conductivity 1
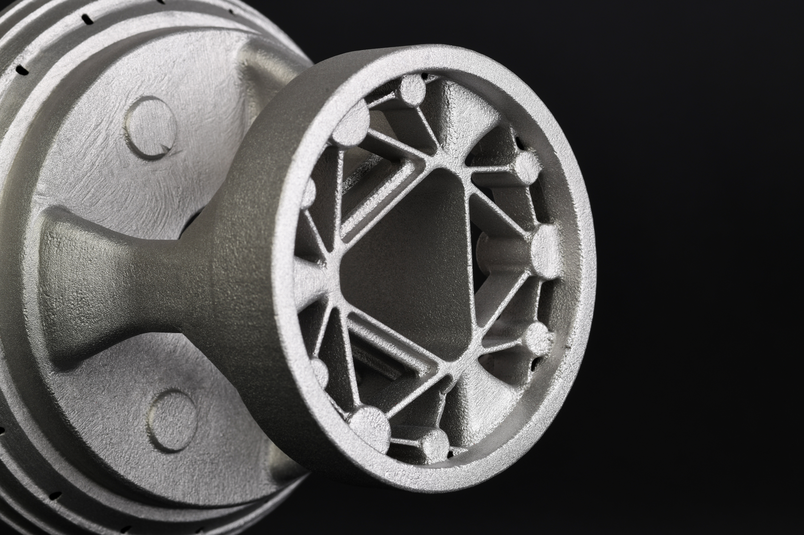
Footnotes Thermal cond 1
HT thermal conductivity 2
Foot notes thermal conductivity 2
Surface Roughness
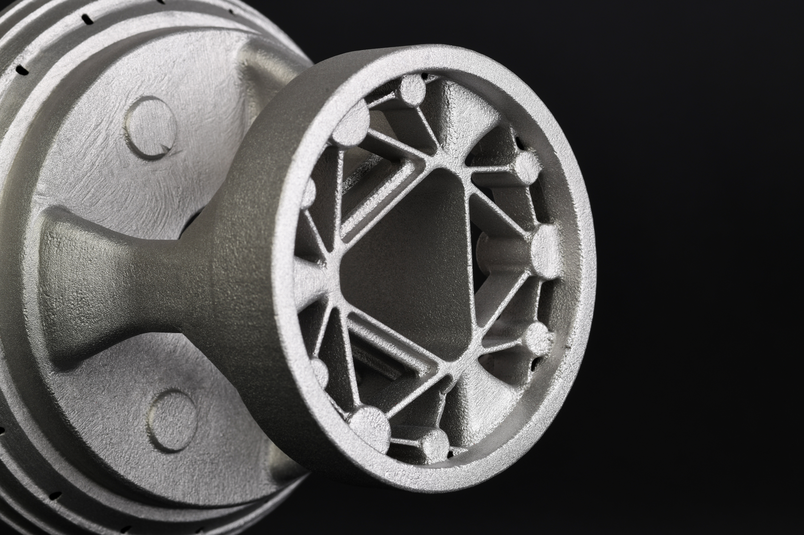
EOS NickelAlloy IN939 parameters were developed for optimized dimensional accuracy of internal cooling features, which are essential to hot gas path components in gas turbines. This comes with a compromise on downskin roughness. Whenever possible, for parts where optimized dimensional accuracy of internal cooling features is not needed, EOS recommends to switch off downskin exposure, to improve downskin roughness and buildability at low angles, and to increase process speed.
Creep performance
AMS 2774 As Manufactured | |
---|---|
Value | 110 |
Unit | MPa |
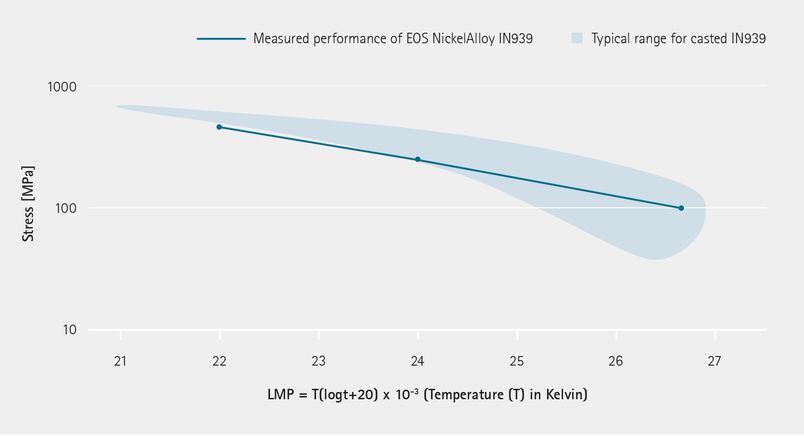
Footnotes Misc. add prop. 1 : The stress-rupture performance of EOS NickelAlloy IN939 was tested on vertically oriented samples, in heat-treated condition. No HIP was applied. The data presents the Larson-Miller Parameter values achieved at stress levels of 100 MPa, 250 MPa and 450 MPa. Standard: ASTM E139
add prop 2
Value | value |
Unit | unit |
footnotes prop 2
Electrical Conductivity
HT electrical conductivity 1
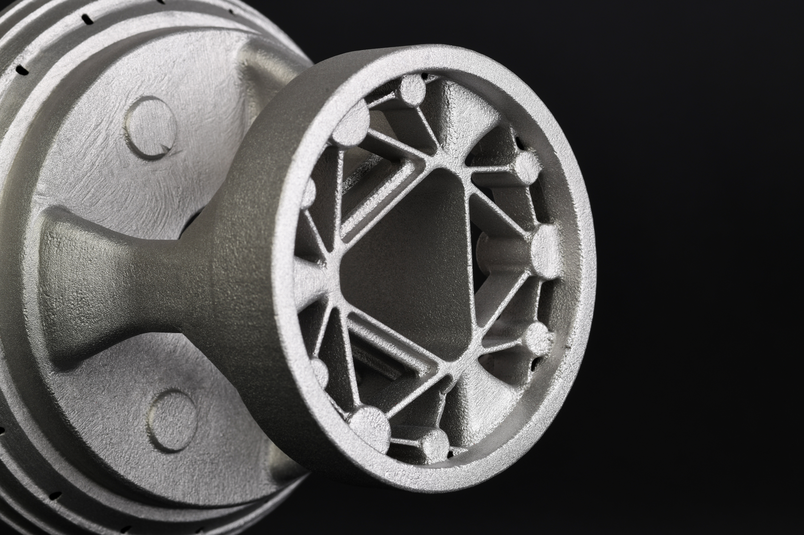
Footnotes electrical conductivity 1
AMS 2774 | Orientation | Typical Electrical Conductivity [%IACS] |
---|---|---|
HIP / 40 µm / Default | Vertical | 10-15 |
HIP / 40 µm / Default | Horizontal | 12-18 |
HT elect conductivity 2
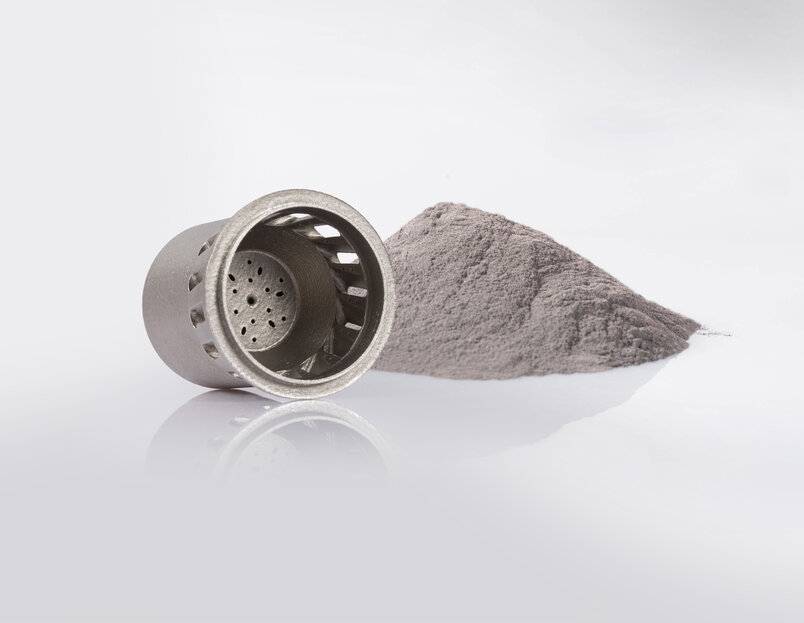
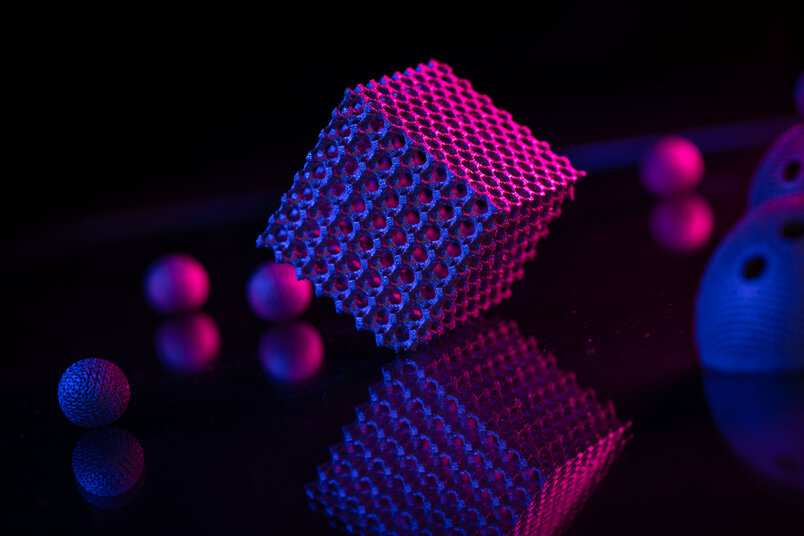
footnotes elect conduct 2
AMS 2774 | Orientation | Typical Electrical Conductivity [%IACS] |
---|---|---|
Heat Treated / 50 µm / Application optimised - Inductors | Vertical | > 5 |
Heat Treated / 50 µm / Application optimised - Inductors | Horizontal | > 6 |
HT elect cond 3
footnotes sample prep 3
Coefficient of Thermal Expansion
ASTM E228 As Manufactured | Temperature |
---|---|
12.18*10-6/K | 25 – 100 ºC |
12.89*10-6/K | 25 – 200 ºC |
13.78*10-6/K | 25 – 400 ºC |
13.49*10-6/K | 25 – 600 ºC |
13.99*10-6/K | 25 – 800 ºC |
15.06*10-6/K | 25 – 900 ºC |
Description HT CTE 25-100
Description HT CTE 25-200
Description HT CTE 25-400
Description HT CTE 25-600
Description HT CTE 25-800
Description HT CTE 25-900
Footnotes CTE 25-100
Footnotes CTE 25-200
Footnotes CTE 25-400
Footnotes CTE 25-600
Footnotes CTE 25-800
Footnotes CTE 25-900
ASTM E228 Heat Treated | Temperature |
---|---|
11.79*10-6/K | 25 – 100 ºC |
12.64*10-6/K | 25 – 200 ºC |
13.64*10-6/K | 25 – 400 ºC |
14.27*10-6/K | 25 – 600 ºC |
15.29*10-6/K | 25 – 800 ºC |
16.32*10-6/K | 25 – 900 ºC |
Description 2 HT CTE 25-100
Description 2 HT CTE 25-200
Description 2 HT CTE 25-400
Description 2 HT CTE 25-600
Description 2 HT CTE 25-800
Description 2 HT CTE 25-900
Footnotes 2 CTE 25-100
Footnotes 2 CTE 25-200
Footnotes 2 CTE 25-400
Footnotes 2 CTE 25-600
Footnotes 2 CTE 25-800
Footnotes 2 CTE 25-900